Table Of Contents
What Is Work Measurement?
Work Measurement is the process of estimating the time a qualified and skilled worker needs to complete a task at a defined level of proficiency. This technique is crucial for evaluating factors like productivity, time consumption, and, most importantly, the quality of work. Through work measurement, improvements in these areas can be accurately assessed and managed.
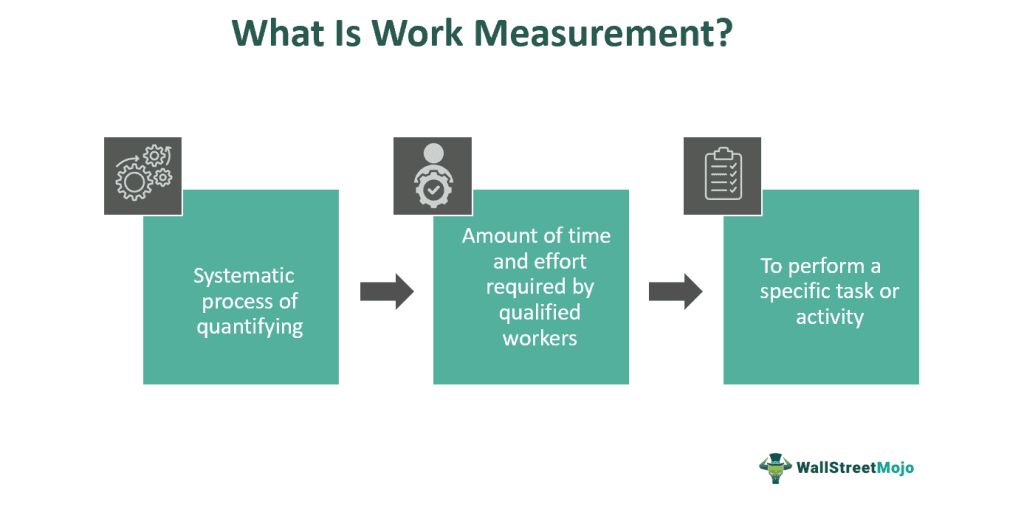
The objectives of work measurement involve gaining a comprehensive understanding and improvement of work processes. It is achieved by meticulously analyzing each task component in terms of quality and time requirements. Such detailed analysis is instrumental in defining tasks and setting standard performance levels. These standards are crucial for evaluating improvements and overall work efficiency, ensuring both productivity and quality are maintained. For businesses seeking innovative ways to improve efficiency, a Motion analytics alternative offers advanced options for tracking and optimizing work processes beyond traditional motion studies.
Key Takeaways
- Work measurement defines the standard of work with respect to aspects such as time, quality, skill, and improvement.
- The general work measurement methods are time sampling, standard data, PMTS, MOST, comparative estimation, and time study.
- It helps in cost control and reduction, work standardization, scheduling, gauging workers' skills, and improving efficiency and productivity.
- Directly or indirectly, the whole structure of company operations, production, supply, and distribution relies on effective work measurement.
Work Measurement Explained
Work measurement is the practice of gauging work and its standardization parallel to time, quality, and completion. In any workplace environment or production unit, workers spend most of their time operating equipment, running errands, operating machinery, working on tasks, and being involved in multiple activities at the same time. Apart from these, it has its scope in other aspects of work such as problem-solving, procedural work, action-based, planning, and insecurity work.
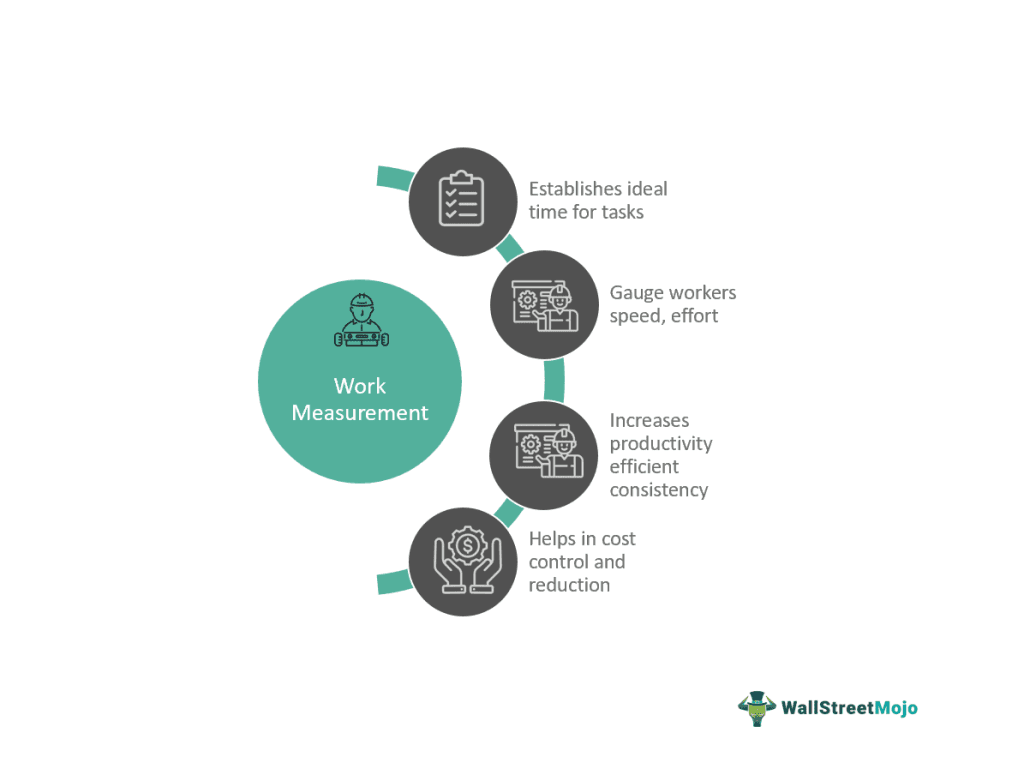
The work measurement definition given by the British Standard Institution states it as the application of techniques that deals with figuring out the time a qualified worker takes to carry out a specified job at a defined level of performance. However, the concept expands to help in making amendments, changes, and shifts of elements to increase efficiency and productivity and reduction of cost. With proper work measurement, companies can assess workers, compare their performance, and train them for better results and consistency.
The three most essential elements of work measurement are time values, preferred methods, and reporting. Without work measurement, there can be no structure, allowed time, and dynamics around a workplace can be planned or executed. It is helpful in every aspect of professional life across sectors and industries, from schools, institutions, corporate setups, blue-collar jobs, staff and production units, and factory labor.
Methods
The methods of work measurement techniques are -
- Time study - It is the direct observation and gauging of a worker's time to perform separate elements of a task to understand the time consumption of the work and operations while measuring the speed of the worker.
- Work sampling - This allows an analyst to understand the time spent by workers on different operations and tasks over some time. It is a statistical technique built on random observations.
- Predetermined Motion Time Systems (PMTS) - This method includes predetermined tables of time requirements gauging every move, motion, turn, and reach of a worker and then measuring the total time consumption for a specific task.
- Maynard operation sequence technique - The whole task is defined in a sequence of small elemental work, and then it focuses on the sequence and predicts the required time consumption of the whole task.
- Comparative estimation - As the name suggests, it is a direct comparison between a task that is already measured and a new task to be performed, and based on the former task, the latter's time consumption is gauged. For instance, for a worker who can lay 90 bricks in thirty minutes based on it, the cement mixing should be at most eighteen minutes.
- Standard data - It is based on historical data and uses it to predict the time required to complete a task. So, for instance, if earlier some worker with reasonable skills completes a task in thirty minutes, it becomes the standard time requirement.
Procedure
The procedures of work measurement are as follows -
- Defining objective - It is the initial and most crucial step of the whole procedure. The objectives must be predetermined to have precise results. This step also includes the scope, participants, scale, time, and process is also defined.
- Technique selection - From all the methods discussed, the analyst or company has to choose the proper technique that fits the workplace, the nature of the work, and the whole structure, depending on the complexity, effort, and efficiency required for the operations. Accordingly, the method is chosen. It could be MOST, PMTS, time study, work standard, sampling, etc.
- Data collection and recording - This is the simple process of recording data in different forms using tools such as a camera, clipboard, stopwatch, software, scale, and even rating systems. It serves as the primary data to analyze workers and their work performance. Also, when collecting, the analyst must make sure that they have collected sufficient data for calculation purposes.
- Data evaluation - Once the data is collected, it is analyzed to arrive at various results, comparison points, and interesting insights and conclusions based on which the amendments in the work measurement, performance, and standardization are set. It is basically done using statistical methods such as mean, mode, range, median, standard deviation, etc. The anomalies, errors, and outliers are also eliminated in this step. Moreover, the adjustments and resettling of data considering fatigue, allowance, and other delaying factors are done as well.
- Standardization and improvement - Based on the results, the work measurement is performed, the standard time for performing a specific task is set, the speed and time spent by a worker is tested, and it is also used for making other decisions regarding cost reduction, scheduling, and task control, etc.
Examples
Let us understand the concept through some examples.
Example #1
Suppose a typing institute hires Katherine, who is an amateur typist. Initially, all the other employees at work can finish typing a full page of words in twelve minutes. The management can measure the time spent by Katherine on a full page of words. Now, if she can type a full page of words in approximately twelve minutes, Katherine follows the standard time.
Conversely, suppose Katherine spends about fifteen minutes finishing the paper. In that case, it indicates that there is room for improvement, and based on it, the institute can gauge Katherine's skills, encourage her to perform better, and set up a training program for her.
Example #2
Jamie owns a small restaurant, and the place is known for its burgers. Every day, Jamie sells almost 720 burgers. Jamie believes there is room for improvement, and therefore, apart from his regular chef, he is looking for another chef who can make a burger in approximately 90 seconds.
Jamie posts an ad for a chef's requirements, and every day at night after he closes the restaurant, he takes tryout interviews of people who applies for the job. Jamie sits with a stopwatch and practically tests the speed of the applicants to measure their performance. After nine days, he finally meets Alysa, who has been in the food industry for more than four years, and finishes making a burger in less than 81 seconds.
Jamie is impressed with Alysa and hires her. In this example, Jamie was determined to test the performance and consistency of the applying chefs and used the method of time study to calculate the results.
Advantages And Disadvantages
The benefits of work measurement include the following:
- It enables the establishment of tasks with predetermined timeframes and quality standards.
- It provides valuable insights for informed decision-making in areas like cost control, supervision, and strategic planning.
- It facilitates the assignment of suitable employees to tasks, enhancing efficiency and outcomes.
- It identifies skill gaps in employees, allowing for targeted training and development.
- It enables companies to evaluate and refine methods, thereby boosting productivity.
On the other hand, the drawbacks of work measurement are:
- It lacks detailed time data for individual task elements.
- There is criticism for its rigid standards, which may discourage innovation and experimentation.
- It can be cost-prohibitive, especially for smaller businesses.
- The process can be intricate and time-intensive, posing challenges for many organizations.