Achieving the Perfect Balance: V-Curve Optimization in Modern Manufacturing
Table of Contents
Introduction
In the current manufacturing landscape that features rapid technological innovations, optimizing the efficiency of the production line is essential. After all, efficient management can minimize operational costs, accelerate time to market or TTM, and improve product quality, irrespective of whether it is a large-scale factory or a small-scale production line. That said, achieving high productivity and efficiency with regard to manufacturing processes can be challenging.
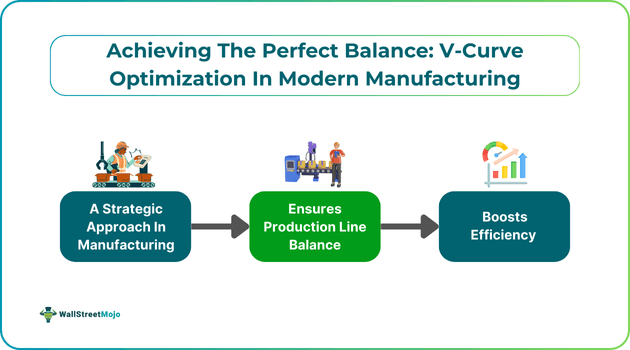
If you are looking for ways to streamline production lines, you are on the right page. In this article, we’ll discuss how V-Curve optimization can help in that regard and enhance the efficiency of your production line. But first, let us dive into why line optimization is crucial.
Importance Of Line Optimization
One can understand the importance of production line optimization by going through the following points:
- Optimizing Resources: Line optimization plays a key role in the efficient utilization of the available resources. Typically, the higher a product line’s efficiency, the better the company is at utilizing the resources.
- Enhancing productivity: Businesses need to generate more output while utilizing the same or fewer resources to achieve modern manufacturing efficiency. Finally, higher productivity will result in higher profitability.
- More Effective Fulfilment of Customer Demands: Line optimization ensures the timely delivery of high-quality products, which, in turn, fulfills customer demands and ensures customer satisfaction.
- Improving Employee Morale: Enhancing employee morale can lead to manufacturing process improvement as workers’ productivity increases when they are satisfied.
If an organization aims to achieve the objective of line optimization, it may consider using effective production optimization techniques, such as the following:
- Implementation of lean manufacturing principles
- Execution of total productive maintenance or TPM
- Deployment of robotics and automation technologies
- Inventory management optimization, etc.
Understanding the V-Curve Theory
The V-Curve theory refers to a strategic approach that involves balancing the machine speeds associated with a production line. It manages the product flow and optimizes the overall efficiency of the production line via the coordination of speeds related to different machines on the basis of the “critical” machine. This critical machine is usually the costliest equipment in the production line, and the accumulation production lines are often structured around it. Generally, it is the slowest equipment, and its performance measures the line’s overall performance.
The whole line functions without any issues when this machine is operational. On the whole line slows down if the equipment slows done. The remaining machines in the production line run at higher speeds compared to their adjacent pieces of equipment moving in the critical machine’s direction.
This approach can help optimize resource allocation and improve productivity in different ways. It minimizes idle time and eliminates bottlenecks. Moreover, it can help balance workload across different workstations, which can lead to a smoother manufacturing process.
Applying this theory in a real-world scenario is called V-Curve optimization, which we’ll explore in detail in the following sections.
How to Start With V-Curve Optimization?
One can follow these steps to carry out the V-Curve optimization:
- Identify the critical equipment on the line. In other words, spot the slowest machine.
- Set the baseline speeds. Generally, the critical machine’s speed serves as the baseline for the other machines.
- Make adjustments to a couple of machines immediately preceding and succeeding the critical equipment so that they run 10% quicker during recovery periods.
- Equipment further along the production line is adjusted in a way that makes it run incrementally quicker, generally by 10%.
- Lastly, utilize sensors on the machines’ outfeed and infeed. These sensors help manage flow dynamically as they detect alterations concerning the production line and respond to them.
Visually, the overall configuration is V-shaped, with the critical equipment at the bottom, while the other machines remain on either side.
Besides following the above steps, organizations need to distribute tasks in a manner that balances the workload. Precisely, they should factor in the complexity and the expected time required before allocating. Also, entities must have clear standards for workstations and tasks to ensure efficiency and consistency. They need to define the standard work procedures, quality control measures, and guidelines to ensure uniformity concerning task completion.
Strategizing for High-Mix, Low-Volume (HMLV) Production Challenges
The HMLV approach involves the organization producing an extensive range of products, but the quantities manufactured are small. Some of the noteworthy challenges of this approach are as follows:
- There is a chance of a mix-up concerning the production procedures. Also, there’s a risk of employee burnout. These things can negatively impact quality and raise cycle times.
- Balancing lead times and product variability is usually challenging.
- Lastly, maintaining quality across all the different production lines is difficult, given the different kinds of quality control procedures.
Companies can overcome these challenges and ensure efficiency by using these production optimization techniques:
- Standardization: This involves developing different standard operating procedures or SOPs for repetitive tasks. With these SOPs, manufacturers can enhance the quality of the output and minimize mistakes. This, in turn, can result in manufacturing process improvement.
- Communication: Considering the immense activity associated with HMLV manufacturing, effective communication among workers is essential for modern manufacturing efficiency.
- Lean Manufacturing: This refers to a production process that is based on a philosophy that involves maximizing productivity while reducing waste within manufacturing operations at the same time. It can result in minimized lead times, better product quality, and lower operating costs.
Lean Manufacturing and V-Curve Optimization
While both approaches are used for manufacturing process improvement, there is a key difference between them. Lean manufacturing is based on the idea of maximizing productivity while minimizing wastage. On the other hand, V-Curve optimization focuses on improving efficiency by focusing on speed and striking the right balance in relation to the production line.
Line Balancing Software
Companies are now taking the help of software solutions to implement manufacturing approaches efficiently and improve output. Smart line balancing software solutions like LineView can allow companies to optimize their production line dynamically. It acts as a vigilant assistant for the entire manufacturing process. This software continuously scans to identify changes in supply or demand and proposes immediate adjustments that the organization can make to balance the load without any hassle.
In addition, this type of solution simplifies the production line analysis and automates the data accumulation. Note that the data analysis takes place in real-time via the software so that the manufacturers are able to track the resource utilization and line balance.
Human Factors and Ergonomics in Achieving the V-Curve Balance
The human factors are key aspects that are an integral part of any organization’s manufacturing processes. Let us understand them via these pointers:
- Businesses need to establish a workforce that comprises individuals who are motivated and engaged. They should do their best to ensure the efficient execution of the V-curve optimization processes.
- The workers must have relevant strengths that are key to boosting the efficiency of the factory.
- Entities need to establish production lines while considering their workforce’s well-being. Precisely, the workstations should minimize injury risks.
Taking into account the human factors is vital to strike the V-Curve balance and ensure manufacturing efficiency.
Adapting to Market Demands with V-Curve Flexibility
V-Curve optimization concerningmanufacturing processes allows for a high level of flexibility with regard to the allocation of resources. Since the workload remains balanced in the case of this approach, it is easy for organizations to make adjustments that are necessary to fulfill the changing customer demands.
Future Outlook
With technological advancements in the manufacturing space, it is highly likely that soon, more solutions will be introduced that can further improve manufacturing processes to boost efficiency. Indeed, with the use of artificial intelligence and machine learning, companies can come up with better solutions that can facilitate manufacturing process improvement. This can enable companies to produce higher levels of output that too of higher quality, while ensuring the optimal allocation of resources.
Conclusion
Ensuring an optimal level of productivity and efficiency requires manufacturers to maintain production line balance. The achievement of this balance is possible via V-Curve optimization, a systematic approach that can minimize cycle times, improve product quality, and increase the efficiency of workstations. That said, like all other approaches, this process comes with certain limitations. Hence, one must consider weighing the pros and cons before deciding to use the approach during the production process.