Table Of Contents
Top 3 Types of Inventory
The three types of inventories are direct material inventory, work in progress inventory and the finished goods inventory where the direct material inventory includes the stock of raw material which the company has purchased for its use in production; work in progress inventory is the cost accumulated to the goods that are partially completed and the finished goods inventory is the stock that has finished all stages of production and is now available for sale.
Inventory means those current assets that have been or will be converted into the company's final products for sale shortly. In other words, inventory represents finished goods or goods in different stages of production that a company keeps at its premises or at third-party locations with ownership interest retained until goods are sold. The three most important types of inventory are the raw materials, the work in progress (WIP) inventory, and the finished goods.
Have a look at Colgate’s Inventory breakup for 2016 and 2015. There are three types of inventory listed – raw material and supplies, work in progress, and finished goods. Also, note that most of Colgate’s inventory is the Finished goods inventory.
Table of contents
- The types of inventories are direct material inventories, work-in-progress inventories, and finished goods inventories.
- Direct material inventories include the stock of raw materials the company has purchased for production; work-in-progress inventories are the cost accumulated to the partially completed goods.
- Finished goods inventories are the stock that has completed all stages of production and is now marketed.
- Inventory is the collective term for all current assets that have been or will soon be transformed into the firm's finished goods for sale.
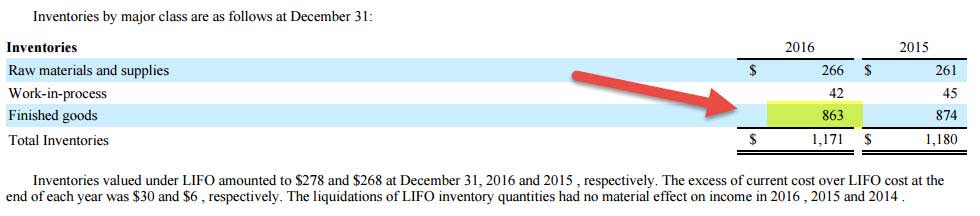
Following are the different types of inventory:
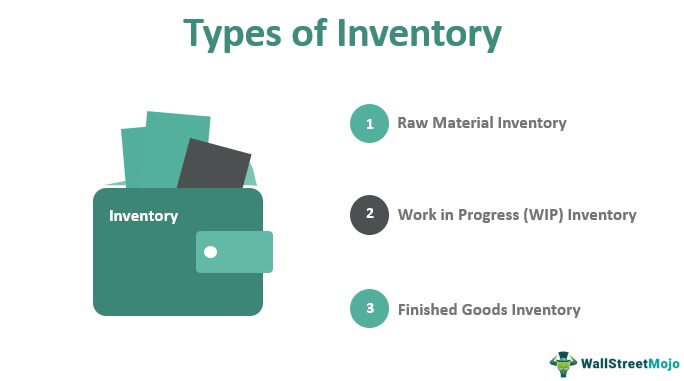
#1 - Raw Material Inventory:
Raw materials are the basic materials that a manufacturing company buys from its suppliers. The former uses them to convert them into the final products by applying manufacturing processes. For example, aluminum scrap is the raw material for a company that produces aluminum ingots. Flour is the raw material for a company that produces bread or pizza. Similarly, metal parts and ingots are the raw materials bought by a company that manufactures cars, and crude oil is the raw material for an oil refinery.
It is prevalent and easy to observe that the final products of one company are bought as raw materials for some other company. For instance, many oil drilling companies produce crude oil as their final product. But on the other hand, the same crude oil is bought by oil refining companies as raw materials to manufacture their final products, i.e., gasoline, kerosene, paraffin, etc.
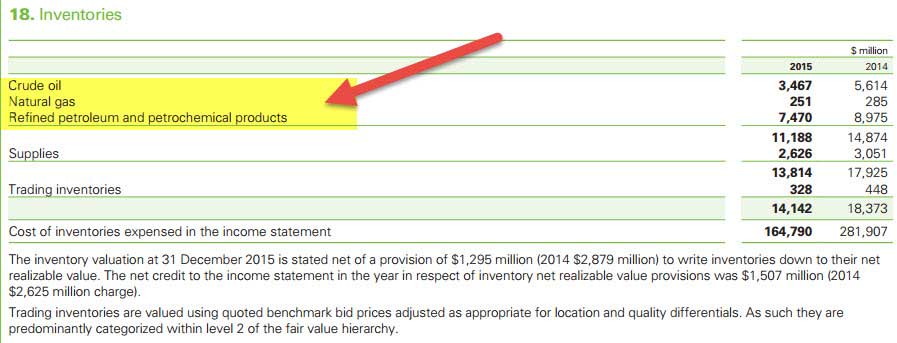
source: BP Annual Reports
As we note from BP's annual report, Crude Oil and Natural Gas are the raw material inventories included in the Types of Inventory Classification.
It is essential to optimize raw material inventory. If a company keeps too much raw material inventory in stock, it will incur higher carrying costs, and there is also the undesirable possibility of the inventory getting obsolete. For example, the raw materials may be perishable in the pharmaceutical or food industry. If not used within a stipulated time limit, they can expire and can’t be used in production. On the other hand, a company must have a certain minimum level of inventory to cater to the production volumes, which mostly follow the trend of the market demand. Thus, the optimization of raw material inventory is essential.
#2 - Work in Progress (WIP) Inventory
Work in progress inventory can also be called semi-finished goods. They are the raw materials that have been taken out of the raw materials store and are now undergoing the process of their conversion into the final products. So these are the partly processed raw materials lying on the production floor. And they have also not reached the stage where they have been converted into the final product.
The extent of inventory locked up as work in progress is lower, the better. It is understandable as the inventory under process is of no use till it gets converted into the final product. It may be saleable at some price, but it cannot be sold to generate any revenue for the company’s core business. In fact, in lean manufacturing systems, the work-in-progress inventory is considered waste.
So it is most desirable that the volume of inventory lying in the form of work in progress be minimized. The time taken to convert it into the final is also minimized so that the locked-up value can be released as quickly as possible. The idea is that this capital, which is locked up in the form of work-in-progress inventory, can otherwise be invested somewhere else to achieve much better returns.
#3 - Finished Goods Inventory:
Finished goods are the final products obtained after applying the manufacturing processes to the raw materials and the semi-finished goods discussed above in the article. They are saleable, and their sale contributes fully to the revenue from the company's core operations.
Regarding the level of finished goods inventory, we need to look at two types of industries. First, we would take the industries in which the finished goods are mass-produced, and the sale happens after the production. Examples of such industries are the FMCG industry and the oil industry. For a company in such an industry, the correct approach is to maintain the finished goods inventory similarly to the raw material inventory maintained, i.e., at an optimized level per the demand in the market.
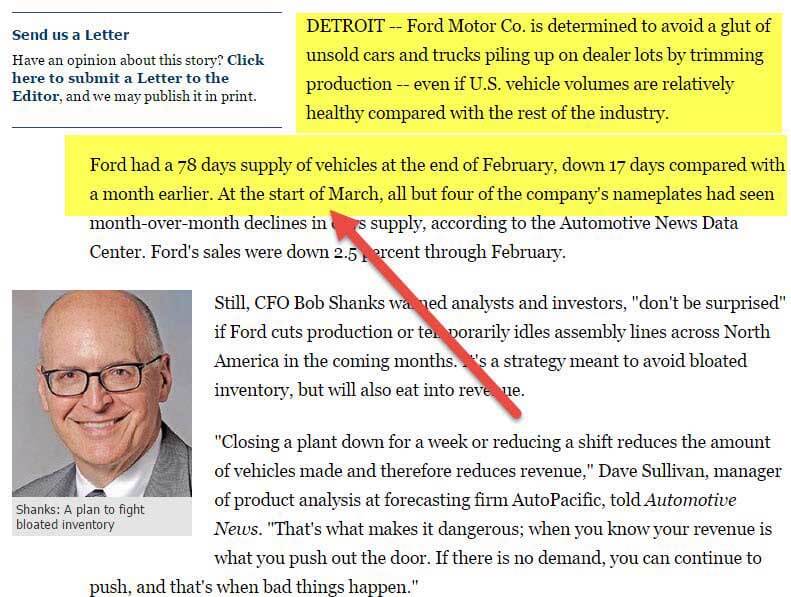
source: Autonews.com
Ford is reducing its finished goods inventory by trimming production. As we noted above, Ford had a supply of only 78 days in February compared to 97 days of stock in January.
The other type of industry is one in which the goods are manufactured on demand, i.e., the order is first received, and then the production starts. Examples of such industries are the capital goods industry and the customized goods industry. For a company in such an industry, it is neither necessary nor advisable to keep any inventory of finished goods because their finished goods kept ready in stock might never get sold even if they have the slightest deviation from the specifications of the new orders coming from the customers. So they may never get a return on their investment in making the finished goods ready.
Other types of Inventory:
There are two other crucial types of inventory, namely packing material inventory and MRO (maintenance, repair, and operating) supplies inventory.
As the name suggests, the packing inventory is the inventory of the company's materials to pack the goods. There is something called the primary packing inventory and the secondary packing inventory within this category. Primary packing is something without which the goods can’t be used. For example, the tube of an ointment is its primary packing.
Secondary packing is used to pack the goods so that they don’t get damaged during handling, transportation, etc., or to make the goods appear more appealing to the customers. For example, the carton used to pack an ointment tube is its secondary packing.
MRO supplies or simply supplies or consumables are those materials consumed in the production processes but do not form a part of the finished goods or form a tiny part of the finished goods. Instead, they are supporting materials for the production process. The maintenance and repair supplies include the lubricating oil, coolant, bolt, nuts, etc., that are used during the production of various machines and machine components. Operating supplies include the stationery and office supplies used by a company.
Frequently Asked Questions (FAQs)
Inventory is divided into three categories using the ABC analysis, with category "A" items being the most critical and type "C" items being the least essential. The ABC analysis can assist in deciding which inventory items should be prioritized regarding stock levels and reordering.
Supplies, replacement components, and other items required for regular maintenance, repair, and operation are MRO inventory (or MRO). The practical process of a business depends on this inventory.
Yes, inventory is considered a current asset as it is expected to be converted into cash within one year or within the normal operating cycle of a firm, whichever is longer. Hence, it is classified as a current asset on a company's balance sheet.
3 Types of Inventory Video
Conclusion
Inventories are the assets that will be converted 9into the final products of a company. They are of three major types: raw materials, work in progress, and finished goods. Inventory management calls for an optimum level of inventory that can be maintained by creating an inventory purchasing plan as per the strategy adopted by the company.