Table Of Contents
What Is Traditional Costing?
Traditional costing is a method used to assign costs to products based on the volume of resources used, such as labor hours or machine hours. It aims to determine the cost of producing or providing a service by allocating indirect costs to the products based on the volume of resources consumed, such as direct labor or machine hours.
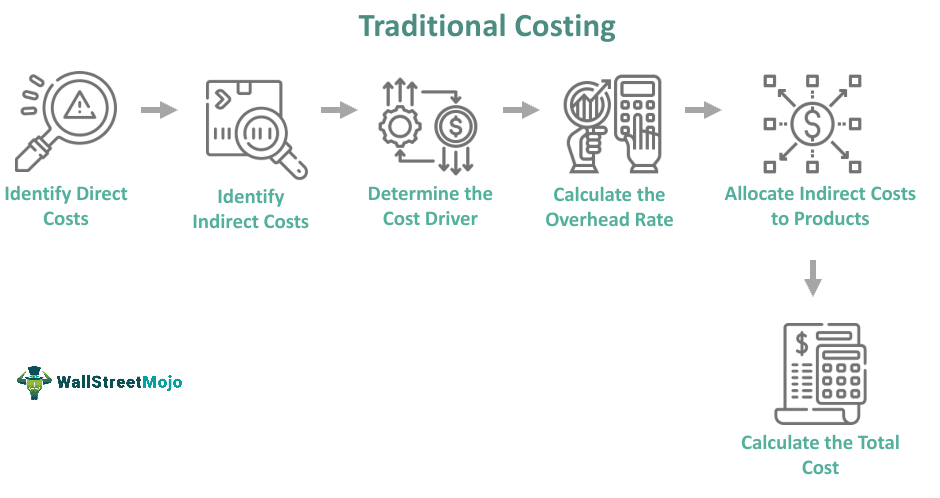
It aims to allocate indirect costs to products based on a predetermined cost driver. This method assumes that all overhead costs result from a single factor. For example, direct labor hours or machine usage, and this factor is the primary driver of overhead expenses.
Table of contents
- Traditional costing is a method that allocates indirect costs to products. This is based on a single cost driver, such as direct labor or machine hours.
- It is a simple method of cost allocation that is easy to understand and implement.
- It has limitations. It includes the potential for inaccurate cost allocation and the inability to account for the impact of non-volume-related cost drivers.
- It is less expensive and time-consuming than more sophisticated costing methods. This makes it suitable for small businesses or those with simple production processes.
Traditional Costing Explained
Traditional costing is a method of cost allocation popular in the business for many decades. It originated in the early 20th century and was developed by accountants who were looking to allocate indirect costs to products and services in a systematic way.
The method involves allocating indirect costs, like overhead, to products based on a predetermined cost driver, such as direct labor or machine hours. The cost driver choice depends on the assumption that the cost of producing a product or providing a service is directly proportional to the volume of resources available.
While the traditional costing method is already popular in business, its limitations have become more apparent in the modern business environment. One of the main limitations is that it needs to consider the complexity of contemporary production processes. And the diverse range of activities involved in producing goods and services. This can lead to inaccuracies in cost estimates, particularly for products that consume different levels of resources. Many companies use complex costing methods like activity-based costing (ABC). This provides a more comprehensive and accurate view of cost behavior. And thus is better suitable for modern business operations' complex and diverse nature.
How To Calculate?
To ascertain the cost of a product using traditional costing, you need to follow these steps:
- Identify direct costs: Direct costs can be traced to producing a specific product, such as direct labor and materials. These costs are typically included in the cost of goods sold (COGS) for a product.
- Identify indirect costs: Indirect costs cannot be traced to the production of a specific product, such as rent, utilities, and overhead expenses. Instead, these costs must be allocated to products using a cost driver.
- Determine the cost driver: The cost driver is a factor that allocates indirect costs to products. The cost driver can be any measure related to the consumption of indirect costs, such as direct labor hours, machine hours, or units produced.
- Calculate the preset overhead rate: The preset overhead rate is calculated by dividing the estimated total indirect costs by the estimated total amount of the cost driver. For example, if the estimated indirect costs are $100,000, and the total number of direct labor hours is 10,000, the preset overhead rate would be $10 per direct labor hour.
- Allocate indirect costs to products: To allocate indirect costs to products, you need to multiply the preset overhead rate by the actual amount of the cost driver used by each product. For instance, if the preset overhead rate is $10 per direct labor hour, and a product requires five direct labor hours, the allocated indirect cost for that product would be $50.
- Calculate the total cost: To calculate the total cost of a product, you must add direct costs (step 1) to the allocated indirect costs (step 5).
Examples
Let us understand it in the following ways.
Example #1
Let's say a toy manufacturer produces two types of toys: simple and complex. The simple toy requires one hour of direct labor and incurs $10 of indirect costs per unit, while the complicated toy requires two hours of direct work and $20 of indirect costs per unit. Using traditional costing, the indirect costs are for each toy based on the preset overhead rate (e.g., $10 per direct labor hour). The total cost of each toy would then be the result of adding the direct costs (e.g., direct labor and direct materials) to the allocated indirect costs.
Example #2
In 2022, Ford Motor Company announced that it would be implementing traditional costing formula to allocate overhead costs to its vehicles. This decision was in response to supply chain disruptions due to COVID-19, making it challenging to accurately give overhead costs using Ford's previous costing method. Using traditional costing, Ford hopes to improve its cost allocation process and reduce overall costs.
Advantages And Disadvantages
While the traditional costing approach has advantages in simplicity and cost-effectiveness, its limitations make it less suitable for businesses with complex operations or those requiring more detailed and accurate cost allocation methods.
#1 - Advantages
- Simplicity: It is a simple method of allocation that is easy to comprehend and implement.
- Cost-effective: It is less expensive than more sophisticated methods like activity-based costing.
- Time-saving: It is a quick method of allocation that requires less time and effort than more complex costing methods.
- Applicable to many businesses: Many companies use it, including small businesses and those with simple production processes.
- Allows for cost comparison: It will enable cost comparison between different products, making it easier to identify areas for cost reduction.
#2 - Disadvantages
- Inaccurate cost allocation: It may inaccurately allocate indirect costs, assuming that all products consume indirect costs similarly.
- Ignores non-volume-related cost drivers: It does not account for the impact of non-volume-related cost drivers, such as quality or customer service, on producing a product.
- Limited accuracy: It may need to provide accurate cost estimates for products that consume different levels of resources.
- Difficulty in determining cost drivers: It may be challenging to decide on the most appropriate cost driver to allocate indirect costs to products.
- Not suitable for complex business operations: It may not be ideal for businesses with complex production processes or diverse activities producing goods and services.
Traditional Costing vs Activity Based Costing
While the traditional costing system is a simple cost allocation method, activity-based costing (ABC) is a more accurate and comprehensive view of cost behavior. This makes it more suitable for businesses with complex operations or those requiring more precise cost allocation.
Here are some key differences:
- Cost drivers: Traditional costing uses a single cost driver, such as direct labor or machine hours, to allocate indirect costs to products. ABC uses multiple cost drivers, such as several setups, inspections, or orders, to give indirect costs to products.
- Accuracy: Traditional costing may allocate indirect costs inaccurately, assuming that all products consume indirect costs similarly. ABC provides a more accurate view of cost behavior by identifying and giving costs based on the activities that generate them.
- Complexity: Traditional costing is a simple method of allocation that is easy to understand and implement. ABC is a more complex method that requires more time and effort to implement, but it provides a more detailed and accurate view of cost behavior.
- Cost-effectiveness: Traditional costing is less expensive to implement than ABC, requiring fewer resources and less time. ABC may be more costly to implement due to its complexity.
- Applicability: Traditional costing is suitable for businesses with simple production processes or those with a limited range of activities. ABC suits companies with complex operations requiring more detailed and accurate cost allocation methods.
- Emphasis: Traditional costing emphasizes direct costs, such as direct labor and direct materials. ABC emphasizes indirect costs, such as overhead expenses and support costs.
Frequently Asked Questions (FAQs)
Traditional costing has several problems, including inaccurate cost allocation, limited accuracy for products that consume different levels of resources, and difficulty in determining appropriate cost drivers. It also needs to account for the impact of non-volume-related cost drivers, which can lead to an overemphasis on cost reduction at the expense of other important factors, such as quality and customer satisfaction.
Many manufacturing companies use traditional costing, as it is a popular method of cost allocation in the industry. Examples of companies that use traditional costing include Ford Motor Company, General Motors, and Procter & Gamble. However, some companies are shifting towards more sophisticated costing methods, such as activity-based costing, to improve their cost allocation processes.
Traditional and absorption costing are similar methods of allocating indirect costs to products based on a predetermined cost driver. However, absorption costing is a more comprehensive method that includes variable and fixed overhead costs, while traditional costing only includes variable overhead costs.
Recommended Articles
This has been a guide to what is Traditional Costing. We compare it with activity based costing and explain it with examples, advantages, and disadvantages. You can learn more about from the following articles โ