Table Of Contents
Supply Chain Definition
A supply chain refers to a process beginning with the procurement of raw materials and the production of finished goods and ending with their distribution and sale. This system comprises suppliers, producers, distributors, vendors, retailers, and consumers. Proper channelization of these entities makes tangible or intangible items readily available to customers.
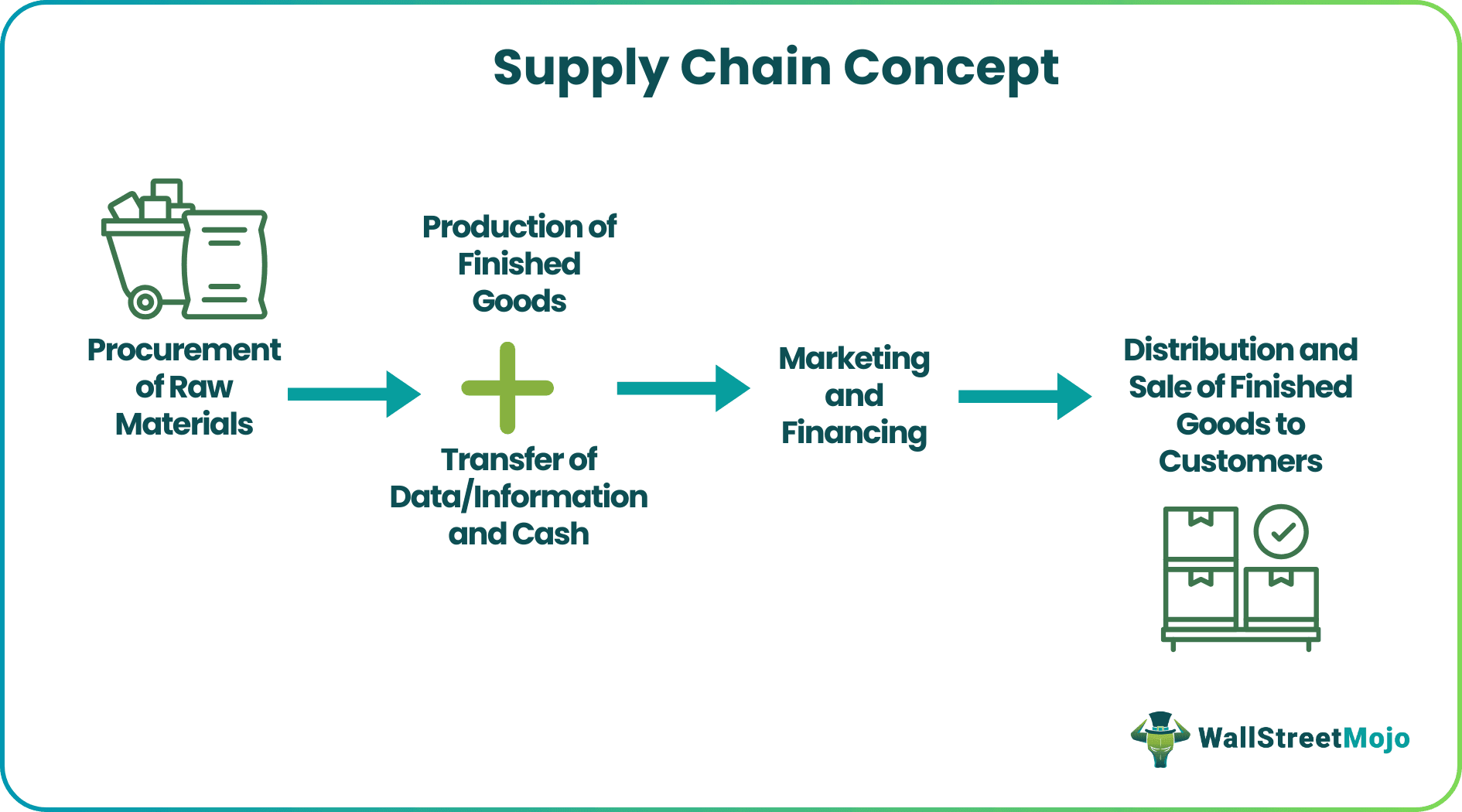
The various points through which these products pass on their way to customers form the supply chain network. This network includes entities, materials, information, and human resources required for the development, marketing, financing, and delivery of products to end-users. Besides physical products distribution, other activities may include data/information transmission and money transfer. It leads to cost-effective and efficient production for businesses while providing customer satisfaction.
Key Takeaways
- A supply chain is the orderly system of manufacturing and selling tangible and intangible commercial goods to end-users. Besides, it facilitates the transfer of data/information and cash flow.
- It consists of suppliers, producers, distributors, vendors, and retailers involved in developing, marketing, financing, and delivery of final products.
- The three supply network best practices include real-time inventory and production planning, technological advancements plus supplier, vendor, and customer relations.
- An efficient product distribution network results in faster product delivery, reduced cost of production and purchase, improved inventory management, increased sales, competitive advantage, and customer satisfaction.
How Does Supply Chain Work?
A supply chain process deals with the movement of raw materials from suppliers to manufacturing units for producing the final product. From producers, the finished product reaches the distributor and then to the retailer, who then sells it to the customer. The main components of a supply network are products, facilities, vehicles, and routes that assist in production and distribution.
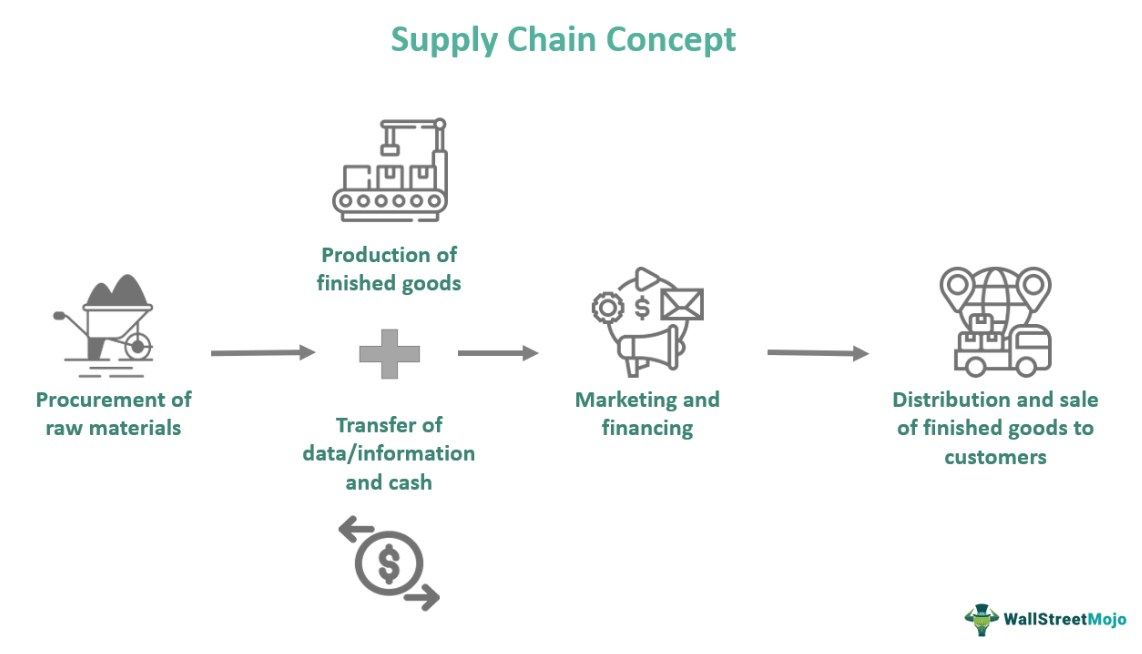
If the customer is happy with the product, the network becomes a pathway for money to flow from customers to manufacturers. On the other hand, if the consumer is unhappy with the product, they may request an exchange or refund from the manufacturer. Thus, the supply channel can effectively handle the reverse flow of items.
The supply network employs best practices such as real-time inventory and production planning, technological improvements such as automation, and supplier, vendor, and customer interactions. This effective product delivery system also allows participants to track products and cash.
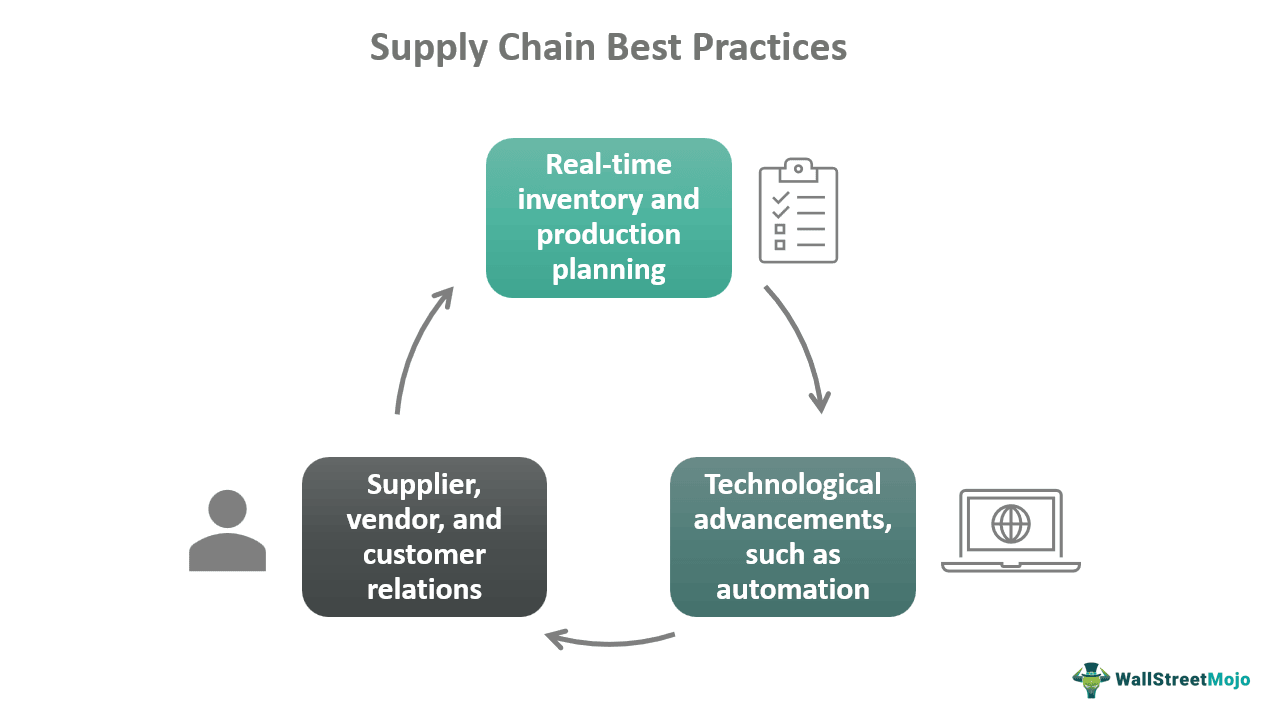
An efficient supply chain management (SCM) will ensure the flow of products and services from producers to consumers. Overall, it controls production planning, inventory management, and distribution processes for a specific product. It, thus, results in improved product quality leading to increased sales and a competitive edge. Additionally, efficient transportation ensures faster delivery and reduces the market price of the product or service.
Steps In Supply Chain
Various stages involved in a supply chain network include:
- Inventory management
- Supply and demand analysis
- Production planning
- Procurement of raw materials
- Production of the finished product
- Product testing and packaging
- Product delivery to the distributor, vendor, retailer, and consumer
- Handling product exchange or return
- Providing customer service support for returned items
Supply Chain Models
Based on its operation and objective, a business can choose from three supply network models to improve production efficiency:
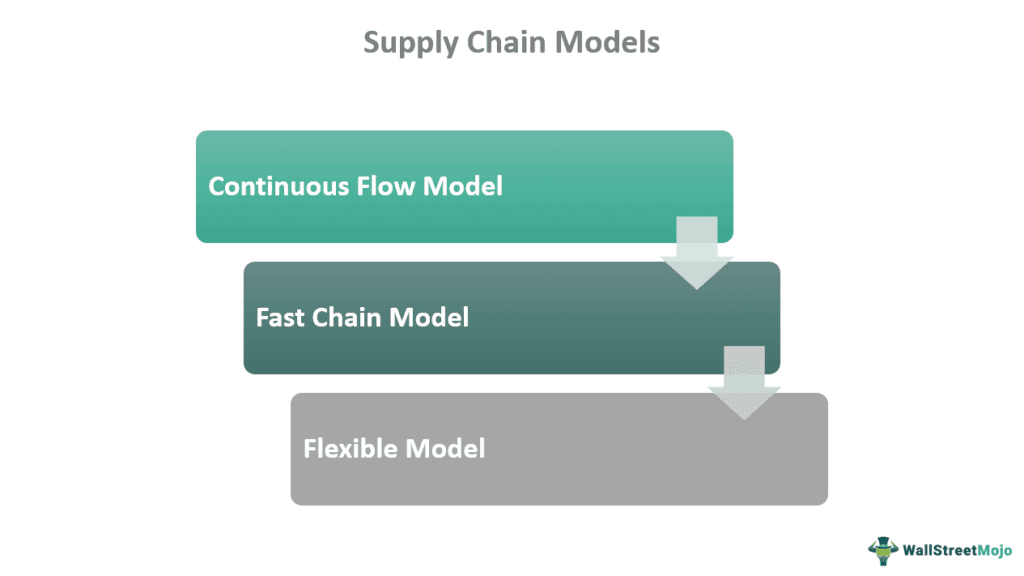
- Continuous Flow Model – To produce identical products with minimal differences to meet the demand and avoid bottlenecks.
- Fast Chain Model – To market, distribute, and sell products with high demand for a short period or based on a trend.
- Flexible Model – To manufacture high-demand products during peak seasons or holidays, followed by unpredictable consumption.
Supply Chain Examples
Let us consider the following supply chain examples to have an in-depth understanding of the concept:
Example #1
Karen owns and operates a pizza parlor. She sells a variety of pizzas to satiate the appetite of the locales. However, to create the most delicious pizzas, she must rely on a supply chain network that ensures the timely delivery of essential raw materials.
As soon as she receives ingredients from the seller/supplier, she prepares orders and serves consumers at her outlet. She also ensures timely delivery for those who want their pizzas to their homes. Thus, the taste and timely delivery make Karen’s pizzas the most preferred over other outlets around.
Example #2
The supply channel is critical to the business process. The global COVID-19 pandemic, however, has disrupted this traditional product distribution system. As the situation might lead to nationalism, trade wars, and greater reliance on domestic manufacturing, businesses must restructure their supply networks to minimize disruption and revenue loss. Furthermore, it will help companies address the shortage of essential supplies and avoid international conflicts.
In this case, technological advancements could be a game-changer. Digital transformations, such as automation, data analytics, artificial intelligence (AI), and blockchain can reshape supply channels. Also, processes like risk management, inventory control, waste reduction, transparency, and fraud prevention will all benefit from this.
Importance of Supply Chain
A supply network organizes everything from supplying raw materials to manufacturing units to distributing finished items to end-users. It, thus, streamlines the entire process and keeps all SCM points connected. However, the lack of connectivity can lead to product unavailability, making consumers switch to other brands. With that said, the following are some of the advantages of having a supply chain strategy:
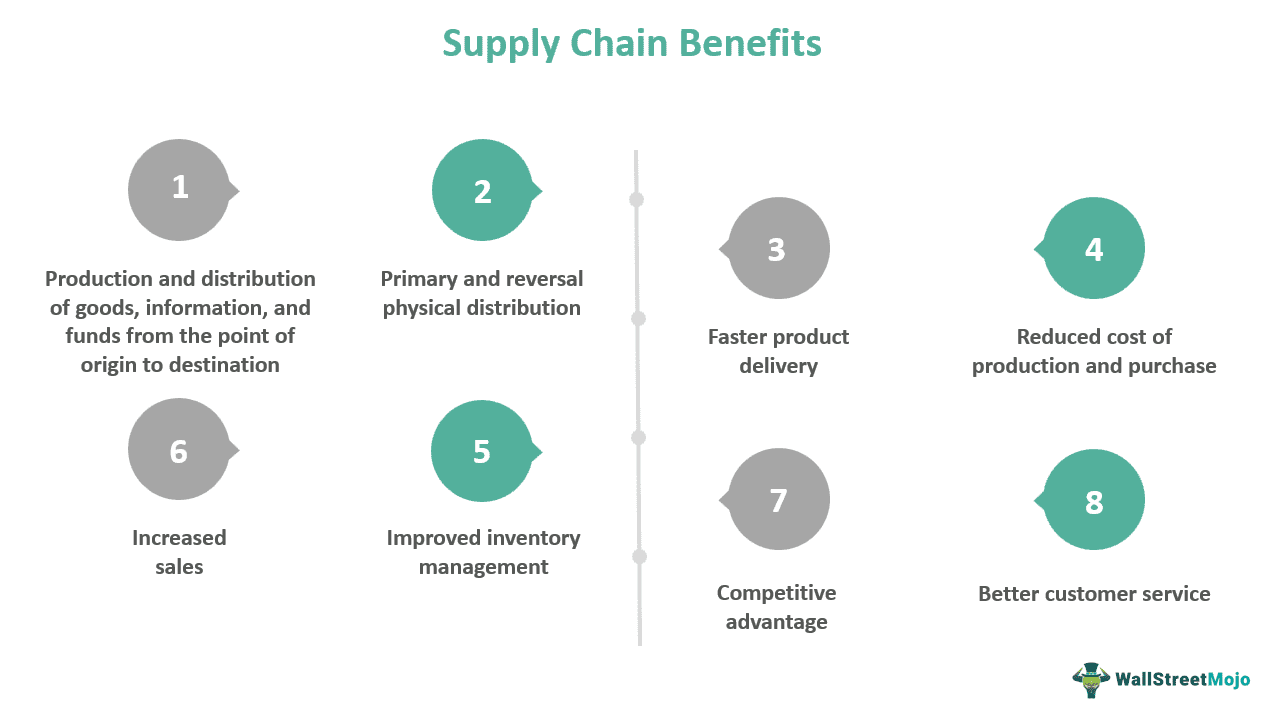
- Facilitates the production and distribution of products from the point of origin to destination
- Allows the transfer of goods, information, and funds along with primary and reversal physical distribution
- Offers competitive advantage and increases customer value
- Interconnects departments, systems, and organizations
- Decreases the impacts of inflation
- Helps in the inventory control and management
- Keeps every point of distribution connected, and hence maintains transparency
- Ensures faster delivery of products and services
- Reduces excess cost, including the cost of production and purchase
- Provides better customer service due to transparent system