Table Of Contents
Spoilage Meaning
Spoilage can be defined as the waste material released due to the normal manufacturing process wherein the spoiled material so released is known as scrap material if it is of no use. Alternatively, it also means unintentional use of offensive material in production, leading to the spoiled output of finished goods.
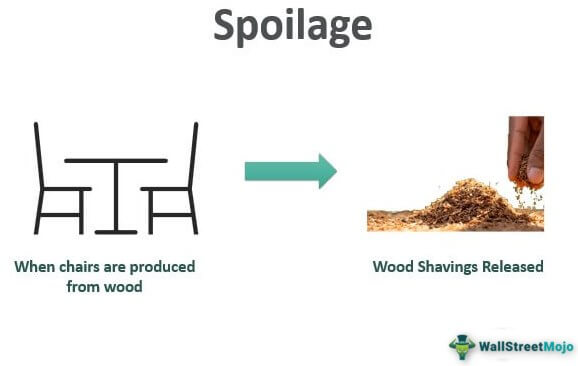
Manufacturers often have to pay spoilage fees to their clients if the products are not in the condition, they expect them to be. These norms are pre-determined through the agreement signed before the production of a large consignment. The added cost of spoilage is added to the cost of goods sold (COGS).
Table of contents
- Spoilage refers to the loss or damage of a product during production or while in storage or transit, rendering it unusable.
- Normal spoilage occurs during the production process due to factors such as evaporation, shrinkage, or breakage. At the same time, abnormal spoilage refers to the loss of products that is not part of the normal production process and occurs due to unexpected factors like machine breakdowns and operator errors.
- Furthermore, regular scrap avoids all the indirect expenses incurred by the company.
Spoilage Explained
Spoilage is the loss of material or wastage of raw materials during a production process. While chemical spoilage and other perishable spoilage are common in the food industry, it is important to note that this terminology is used for products with limited shelf life.
The calculation of spoiled or damaged products is done after the production of each batch of products. First, the total volume of production is determined. After this, the number of damaged products is set aside to arrive at the percentage of the damaged products.
It is a pivotal function to keep track of from a manufacturing unitโs perspective as it either depicts an inefficient production process or a need to upgrade machinery and other equipment.
For any production unit, irrespective of its level of technological advancement, damages, and spoilage is an inevitable factor that cannot be eliminated. However, through strict measures and regular updating, it can certainly be limited.
Spoilage is the wastage occurring due to the production process, and in the normal course, because not entire raw material can be utilized, some become scrap. It is unavoidable and is expected and therefore known as normal Spoilage. However, it can sometimes occur unknowingly and can be recognized only after production due to spoiled inputs.
Normal Spoilage is accounted for by increasing the per-unit cost of goods sold, while abnormal storage is accounted for in the income statement's profit and loss.
Types
The two types of damages that result in manufacturing units paying spoilage fee or adding it to their COGS are discussed in detail below.
#1 - Normal
This is the expected Spoilage due to the natural production process or and therefore, it is not recorded in the profit and loss statement. Instead, it is accounted for by increasing the cost of production. For example, if a company orders 100 liters of petrol for $1000 but can take out only 99.5 liters of petrol from its container, it will assume that the cost of oil is $1000 for 99.5 liters instead of 100 liters. Therefore normal loss increases the per-unit cost of production. It may also be the case that normal loss occurs after production but before the sale; this kind of loss is also adjusted in the same manner as the cost of goods sold.
The formula for calculation of the percentage of normal Spoilage is as follows:

Most of the time, there is a predetermined range within which this percentage should lie based on experience or industry best practices.
#2 - Abnormal
Some examples are the loss of raw material or finished goods inventory due to unexpected reasons such as theft, fire, or in transit. It can be avoided and occurs only due to the lack of precautions. Therefore, this type is not adjusted in the cost of goods sold, but it takes into account the profit and loss statement. Thus, the abnormal loss doesn't increase the per-unit cost of goods sold. There is no formula for its calculations, as it is not fixed or expected.
Examples
Let us understand the concept of chemical spoilage or other forms of spoilage with the help of a couple of practical examples.
- When chairs are produced from wood, the wood shavings are released; similarly, when the oil is transferred from barrels to smaller vessels, the oil remains stuck to the barrel walls. These types of Spoilage are expected, and therefore these are termed normal in accounting theory.
- However, suppose a certain inventory is supposed to be stored at a certain temperature, but this temperature level is not maintained due to power failure. It is an example of abnormal Spoilage, which was not predetermined or expected.
Importance
Despite the fact that it is an inevitable factor in the process, it is important to pay attention to this aspect of production to avoid spoilage fees or face other repercussions. Let us discuss why it is important to pay attention to this though the explanation below.
- Normal Spoilage needs to be paid attention to keep track of the percentage of the same. There is nothing to worry about if this is a stable percentage and equivalent to the competitor's or prevalent in the industry. Still, suppose a particular firm has a very high percentage. In that case, it is an indication for the company to revisit the production process or the points after production where it is occurring. It is done to pinpoint the cause of the same and assess how it can be improved. Any improvement will reduce the cost of production and increase the profit margin.
- Abnormal Spoilage is always a matter of concern. It is an avoidable loss, and therefore, it attracts a lot of flack from the higher-ups in the company. If the plant is not taking enough safety measures against fire or theft, then it is on the plant supervisor because such mistakes cost a lot to the company, which can be prevented.
Difference Between Spoilage and By-Product
There are multiple ways a product can get spoiled or damaged. Therefore, it is important to understand the difference between chemical spoilage or other kinds of spoilage and its difference in comparison to a by-product. Let us do so through the discussion below.
- Spoilage is the unusable material produced as a part of the manufacturing process. At the same time, the by-product is the usable material that is released from the manufacturing of another product. For example, in sugar production, several by-products are produced, such as molasses, beet pulp, and bagasse. These products are sold for a higher value than scrap as these are demanded in the consumer market.
- Abnormal Spoilage is minimized, and its occurrence is not wanted. However, the production of by-products is wanted to the degree that it doesn't affect revenues from the main product. The amount of by-products depends on how much raw material is used in the manufacturing process. The main product generally sells for a higher price. Therefore, the by-product level should not exceed the point where the main product produces lower than the available input-output ratio of raw material and the finished product.
Frequently Asked Questions (FAQs)
Since normal spoiling occurs frequently and is an expense, it should be capitalized into inventory. Spoilage that is uncommon should not be capitalized into the stock. Unusual spoiling needs to be charged at the time it occurs.
Debit the loss amount from the "loss on inventory write-down" account in your records. You can debit the "cost of goods sold" account instead if the loss isn't considerable to your small firm. These accounts, which are expense accounts, are increased by a debit.
The goal of spoiling accounting is to quantify costs associated with spoilage and make a distinction between typical and atypical expenditures. Spiling expenses should be managed, controlled, and reduced; they shouldn't just be added to production costs.
Recommended Articles
This article has been a guide to spoilage and its meaning. Here we explain its types & their formula, examples, and why do we pay attention to spoilage. You may learn more about financing from the following articles โ