Table Of Contents
What Is Setup Time?
Setup Time is the gap between which the machine is adjusted to make it ready to process a job. In operations management, setup is associated with a change in a production process. This change requires time and makes the process relevant for operations.
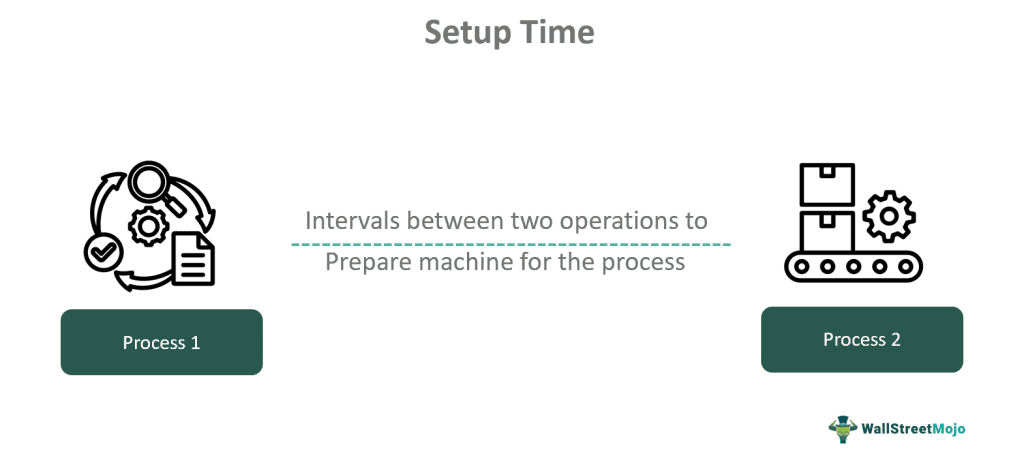
Minimizing this time helps in short production runs and assists businesses in just-in-time production. By doing so, a business can become profitable by running smaller batches of processes because each setup time has a cost linked to each incremental unit. This time, it reflects how flexible or complex the production process will be.
Key Takeaways
- Setup time is the amount of time spent to make a machine ready and fully able to run a process in business and manufacturing operations.
- Companies tend to reduce this time as it helps maximize production, efficiency, and, eventually, overall profit.
- A company facing increased set-up time reflects its poor utilization of the workforce, ignorance, lower productivity, and increased manufacturing costs.
- It is measured as the time elapsed between the last good run and the first good part of the new run.
Setup Time In Operations Management Explained
Setup time is the amount of time taken to regulate, set, prepare, or make a machine ready for operation. Factories, manufacturing units, and production facilities commonly observe the practice of optimizing the operation process. The productivity, efficiency, and capacity of a manufacturing unit are inversely proportional to the setup time. As a result, the longer the setup process takes, the less production will occur, as it simply takes more time to complete the tasks.
Reducing this time is one of the most crucial concerns and practices of any manufacturing unit. It has a series of benefits that ultimately help the company, such as less process variability, lower manufacturing costs, shorter lead times, improved cash flow, and increased capacity, along with less inventory usage and better quality and consistency. With minimal setup time, the company becomes successful in avoiding or delaying capital equipment purchases with increased flexibility and better utilization of the workforce.
Many corporations that are into bulk production and mass manufacturing pay close attention to their setup time servers because they must maintain their time and efficiency. It would add up to the time they have to supply goods into the market; the more delayed it gets, the more the company will take time to sell and generate revenue.
How To Calculate?
The steps to calculate this time are as follows:
- Establish the beginning and ending times for the setup procedure.
- Note how long the process took in total.
- Determine the precise actions needed to finish the setup procedure.
- Dissect the procedure and note how long each step takes to finish.
- Calculate how long it should take to finish each of the steps mentioned above.
- Determine the elements or possible roadblocks that could influence this time.
- Examine past data to find trends to increase productivity and reduce setup time and hold time.
- Keep an eye on and assess the setup procedure to find areas for improvement.
Examples
Below are two examples related to the concept; the first is hypothetical, and the other is from real-world news:
Example #1
John owns a bottling plant. He produces 90,000 bottles per day. The concern is that John produces multiple types of bottles in his plant, and his workers require setup time between processes to regulate, prepare, and make the machine ready for the next set of bottles every time they produce a batch of bottles.
The increased setup time negatively affects the productivity of John’s bottling plant. John decides to record the time taken to set up the process to seek out areas of wasted time. He came across several points where, during the setup, only one worker was tending to the machine. John believes that if two workers tend the machine, this will drastically reduce the time.
John instructs his workers on the same. As a result, the setup gets reduced by nine minutes. This example not only helps increase productivity but also offers better utilization of the workforce.
Example #2
PPG, an American Fortune 500 company and global supplier of paints, has recently completed its expansion of its plant in Sumare, Brazil. The plant focuses on powder coating manufacturing operations and is a $2.7 million project that has increased the production capacity of the firm by 40%. According to this report, this new plant made it possible by reducing the setup time along with the use of highly automated machinery and equipment, coupled with better process control for color matching and production.
The manufacturing unit is to reach its full potential within the first month. Powder coatings are one of the fastest-growing coating technologies across the world, and this investment aims to meet the growing demand for powder coating from local manufacturers of appliances, transportation, agricultural machinery, and other industries.
How To Reduce?
The ways to reduce setup time are as follows:
- The manufacturing unit can devise a setup time reduction program to follow and make changes with revisions.
- The factory management can record the setup process to spot areas that are a waste of time.
- By employing the SMED technique. It refers to the Single Minute Exchange of Die, a technique developed by Japanese industrial engineer Shigeo Shingo. The core concept of it is to minimize the setup time to less than 10 minutes.
- The factory can use a zero-point work-holding method.
- The manufacturing unit can invest in offline presenters that will help preset the machine and eliminate wasting time setting them in between intervals.
Setup Time vs Hold Time
The main differences between setup time and hold time are as follows:
Setup Time | Hold Time |
---|---|
It is the interval between manufacturing used to set or make a machine ready for the following process. | The period during which machine parts are held under specific conditions or as per requirements is termed hold time. |
Industries seek to reduce this time. | The hold time is mandatory and demanded by the process. |
It is observed as an interval between two running processes. | It is part of a manufacturing process. |