Table Of Contents
What Is Production Order?
Production Order refers to triggering a series of actions that procure raw materials, convert an order from raw materials to finished goods, and deliver it to the customer. Since many factors and pre-conditions are involved, it is usually automated and uses enterprise software such as SAP.
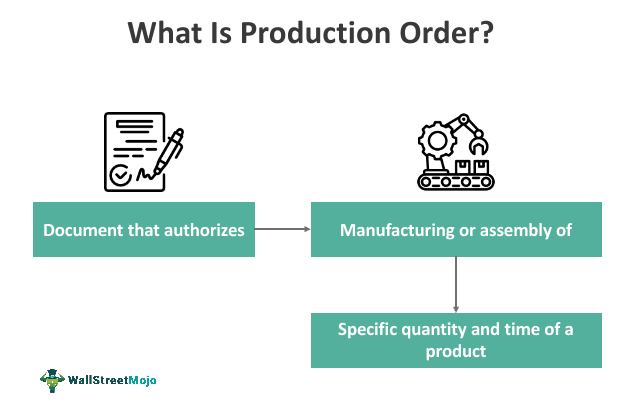
It is also called manufacturing or work order and integrates the availability of raw materials, labor for manufacturing, production capacity, etc. It aims to ensure cost minimization, optimum resource utilization, profit maximization, and customer satisfaction through order fulfillment and quick delivery. Thus, it is an integral part of supply chain management.
Table of contents
- A production order is a document in supply chain management that initiates the activities from raw material procurement to manufacturing to customer delivery.
- Also known as a manufacturing order or work order, its objective is to reduce the cost of production through the integration of tasks and collaboration of stakeholders.
- Having the right product in the correct quantity and at the right time will ensure customer satisfaction.
- SAP production order is a planning and execution tool many companies use. Considering the ton of associated tasks, automated software can help.
Production Order ExplainedÂ
Production order is an essential action in the supply chain, especially in inventory management. It initiates the production process by considering the amount of raw materials available, the number of laborers for production, funds required, goods already manufactured, and the time required. It also initiates a supply order for the production of the required quantity.
The use of production order management software is increasing in manufacturing industries, as multiple stakeholders and many activities are involved. Most of these should be done in coordination and often simultaneously. SAP is the market leader in this area. Automation and artificial intelligence go a long way in adding collaboration and organization to the production process.
It is also essential in inventory management, as it maintains the level of stocks by avoiding piling up or understocking. Optimizing inventory costs (stock holding and ordering costs) is another eliminated concern when ordering the quantity. It is a great way to reduce wastage without unnecessarily holding up stocks. It also allows a streamlined process to ensure production is consistent with customer demand.
ExamplesÂ
Refer to the examples given below for a thorough understanding of the concept.
Example #1
Suppose Autolux, a distinguished premium automobile company, follows a unique manufacturing approach. The company initiates the production of cars exclusively upon customer order placement, coupled with a mandatory pre-payment of at least 50% of the estimated car value.
Automating this process, Autolux employs a sophisticated manufacturing order system that systematically coordinates the supply of parts, assesses labor availability, and addresses fund requirements promptly upon customer order placement. This automated system ensures a seamless and efficient workflow, aligning manufacturing resources precisely with customer demand.
Example #2
In February 2023, Boeing announced a noteworthy order from India for 220 aircraft, encompassing various models such as the Boeing 737 Max, 787 Dreamliners, and 777X. While the exact nature of the order wasn't labeled as Boeing's third largest, it undoubtedly signifies a substantial commitment and an uptick in manufacturing order commitments for the company.
The intense competition between Boeing and Airbus is evident, with Airbus securing a larger order of 250 aircraft from India. These announcements emphasize the pivotal role of manufacturing orders in the aviation industry, showcasing the ongoing efforts by major manufacturers to secure commitments and streamline their manufacturing processes to meet global demands.
Production Order vs Process OrderÂ
First, let us define process order. A process order is a document that is also involved in the production of goods and services. It enables resource planning and allocation, control of processes, and order assignment. Next, let us analyze the differences between production and process order:
- Process order is prominent in process industries, where constituent parts cannot be separated, touched, or seen individually. Examples of processed industry products are peanut butter, cookies, etc. Manufacturing order, on the other hand, is standard in discrete industries that produce goods that can be assembled as discrete individual units, such as cars, computers, etc.
- The following distinction is the master data, which is the data source for the preparation of documents and analysis. Sources of master data for process orders include the master recipe, material master, bill of materials, production version, etc. Master data for manufacturing orders consist of the bill of materials, work centers, material master, etc.
It is possible to create both production and process orders from planned orders. The planned order is explained in the next section. Also, using software facilitates creating, updating, and deleting both documents.
Difference Between Planned Order And Production OrderÂ
The differences below highlight the distinct roles and stages in the manufacturing process that production and planned orders play, emphasizing planning and execution aspects, respectively.
- A planned order is a document that functions as a procurement proposal or a material requirements planning (MRP) request, primarily used in manufacturing plants. A production or manufacturing order is a document utilized in the execution phase, focusing on the actual manufacturing activities derived from the planning order.
- Planned order is often used to generate both production or process orders and purchase requisitions, serving as a precursor to actual procurement activities. Production order, on the other hand, is used in the execution phase for the actual procurement of supplies and manufacturing activities based on the planning order.
- Only after conversion can manufacturing orders and purchase requisitions be generated, emphasizing the planned order role as a preliminary, planning-focused document. production order represents a fixed receipt element, indicating its role in the concrete execution and fulfillment of the planned order.
- Planned order is essential in planning manufacturing activities, procurement, and related processes. Production order holds significance in the practical execution and realization of the planned order, ensuring that manufacturing activities align with the established plan.
Frequently Asked Questions (FAQs)
It is a mathematical technique that helps determine the number of goods a company has to order or produce to minimize inventory costs while balancing ordering and holding costs. It is also known as the economic production quantity model.
Yes, It can be generated from planned orders. A planned order serves as a preliminary document outlining the materials and resources needed for production. When the planned order is converted, it results in the creation of a manufacturing order, initiating the actual manufacturing process. This seamless transition ensures that production activities align with the initial planning phase.
To delete a production order in SAP, follow these steps:
1. Access the SAP system with the account.
2. Navigate to the 'Production' option.
3. Locate the specific production order to be deleted.
4. Use the appropriate functionality within SAP to delete the production order.
Note: Ensure that one has the necessary permissions to perform deletion actions in SAP.
Recommended Articles
This article has been a guide to what is Production Order. Here, we explain its examples and comparison with process order and planned order. You may also take a look at the useful articles below –