Table Of Contents
What Is Process Control?
Process control is a method for monitoring and managing industrial processes to ensure consistent quality and achieve desirable outcomes. It involves tracking various parameters and variables within a production or manufacturing process and making real-time adjustments to maintain quality, efficiency, and safety. It aims to minimize variations and deviations from the desired standards.
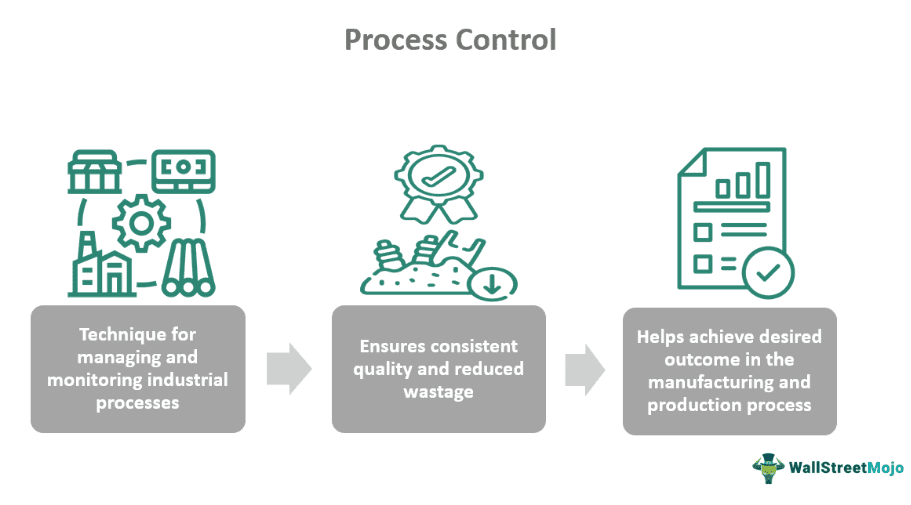
This control applies to several industries, including manufacturing, chemical processing, energy production, food production, etc. It contributes to higher product quality, increased productivity, and reduced operational costs by enhancing consistency, reducing waste, and efficiently allocating and utilizing resources.
Key Takeaways
- Process control is a technique of managing, monitoring, and optimizing various industrial processes to attain consistent quality products and meet predetermined outcomes.
- This control method closely tracks and manages the variables influencing the production processes to ensure they meet specific standards.
- It helps industries to achieve their production goals and ensure that the manufactured products meet the desired specifications.
- This process is essential for industries requiring high precision levels, including pharmaceuticals and food production. It aids in upholding production standards and achieving customer satisfaction.
Process Control Explained
Process control is a significant concept in the production and manufacturing process and encompasses a systematic approach to managing and optimizing various methods to achieve consistent and desirable outcomes. These outcomes are associated with quality assurance, efficiency improvement, and safety enhancement. The production process comprises several complex sequences of tasks and interactions among various components. This control involves closely tracking and managing the variables influencing these processes to ensure they meet the pre-established standards.
This control aims to adhere to the predetermined production goals. It strives to ensure the processes consistently produce products that meet the required specifications. This consistency is essential for industries requiring high precision levels, like pharmaceuticals and food production. It helps enterprises enhance product quality, increase operational efficiency, and reduce waste by utilizing technology, data analysis, and control algorithms. Furthermore, it aids in maintaining a competitive edge and drives customer satisfaction by delivering products that meet high market standards.
Objectives
The industrial process control objectives are as follows:
- It ensures that the manufactured products meet specified quality standards consistently. Deviations that could lead to defects or variations in product quality are minimized by closely monitoring and regulating the process variables. It is vital for industries where even minor deviations can result in significant financial losses or risks.
- Industrial process control optimizes resource utilization, like raw materials, energy, and time. Wastage and inefficiencies are minimized by maintaining precise control over the process. It leads to higher production rates, reduced operational costs, and more sustainable use of resources.
- It helps identify various challenges in the production process and warns of any complications. The control systems recognize issues early and help reduce any disruption in the production process.
Types
Some types of process control are:
- Open-Loop Control: In this control type, predefined parameters are established for the process. The control system operates without continuous feedback from sensors to adjust for changes in process conditions. Open-loop control is suitable for operations with stable conditions where the desired outcomes can be achieved by following a predetermined sequence of actions.
- Closed-Loop (Feedback) Control: This is one of the most common types of process control. It involves using real-time sensor data to continuously track the process conditions and compare them with the desired parameters. The control system then makes adjustments based on this feedback to maintain the process within acceptable limits. Closed-loop control is essential for functions sensitive to variations and requiring constant monitoring and adjustment.
Examples
Let us study the following examples to understand this process:
Example #1
Suppose Sarah owns a bakery named Sweet Treats. She bakes the cakes in an oven. The sensors inside the stove monitor the temperature. If the temperature falls below the ideal range, the controller makes the heating element raise the temperature. Once the temperature reaches the desired level, the heating element turns off. This process repeats as needed, maintaining a consistent baking temperature.
Example #2
Virtue Market Research published a report stating that in 2022, the Global Moisture Meter for Process Control Market was worth $1.57 billion. It is anticipated to attain a market size of $2.11 billion by 2030. From 2023 to 2030, the market is forecasted to increase at a CAGR of 3.8%. The Moisture Meter for Process Control Market has grown significantly over the past few years owing to long-term market drivers. Additionally, the COVID-19 pandemic's global impact influenced its growth.
Importance
The importance of a process control system is:
- It ensures that products are consistently produced with little quality differences. This process minimizes variations and defects, increasing product quality and customer satisfaction.
- Well-controlled processes optimize resource utilization, reduce waste, and enhance production efficiency. This results in increased output and decreased production costs.
- These control systems monitor the critical attributes and detect unsafe conditions, preventing accidents and hazards. It safeguards the employees and the environment.
- Many industries must adhere to strict regulations and standards. This control helps maintain operations within these guidelines, avoiding legal and financial penalties.
- Controlled processes are more structured, which allows accurate production scheduling, inventory management, and effective resource allocation.
Benefits
Some process control system benefits are:
- Controlled processes offer predictable results. It aids in accurate planning, scheduling, and inventory management.
- The control systems identify deviations and faults early, allowing timely intervention and minimizing disruption.
- Efficient resource usage contributes to sustainability and environmental responsibility. It helps organizations achieve corporate social responsibility goals.
- This control enables easy adjustments to changing conditions, facilitating adaptation to market demands and external factors.
- These methods generate valuable data that can be analyzed to identify trends, areas for improvement, and optimization opportunities.
- Industries with efficient control systems deliver high-quality products consistently, gaining a competitive advantage in the market.
- Automation in the control system minimizes the possibility of human error, resulting in more accurate and reliable outcomes.
- It encourages ongoing optimization through data analysis, leading to continuous process enhancement.
Difference Between Process Control And Product Control
The differences are as follows:
- Process Control: This control method focuses on managing and optimizing the various factors within an industrial process to ensure consistent quality and desired outcomes. It involves tracking and adjusting parameters during production to maintain quality, efficiency, and safety. It aims to minimize variations and deviations from the expected standards using sensors, data analysis, and control algorithms.
- Product Control: This process ensures that the final product meets predetermined quality standards and specifications. It involves testing and inspecting the finished product to verify that it meets the required attributes, like appearance, functionality, and performance. This control focuses on detecting defects and inconsistencies in the manufactured items before they reach the consumer. Product control often includes processes like quality assurance and quality control.
Process Control vs Process Capability
The differences are:
- Process Control: It involves actively managing and adjusting the various parameters and variables within an industrial process to maintain consistent and desired outcomes. It helps ensure the process remains within specified limits and meets the defined quality standards. It includes continuous monitoring, feedback, and real-time adjustments using control systems and automation.
- Process Capability: This is a statistical measure of a process's ability to produce products within specified limits consistently. It assesses how well a method can perform in terms of meeting quality requirements without considering external factors. This analysis helps organizations understand the inherent capabilities of their processes and whether they can produce products that consistently meet customer expectations.