Table Of Contents
What is Prime Cost?
Prime cost is the direct cost incurred in manufacturing a product and typically includes the direct production cost of goods, including the raw material and direct labor costs. It is an essential part of total manufacturing expenses. Costing and effective pricing of the goods are primarily determined on their basis.
- It becomes a base for determining a price, including the margin of the product that is to be sold in the market.
- It is a factor of direct cost, which means the summation of all the expenses like direct cost, conversion cost, and manufacturing cost that are directly incurred in the actual production of goods.
- Any commission paid to a salesperson associated with particular sales is added to Prime Cost.
- The raw material is an industry-specific component, and it may vary according to the type of goods produced; like a car manufacturer company or an automobile industry require Tyre, glass, fiber, rubber, metal, nuts and bolts, and many other small tools as raw material for manufacturing a car.
- While direct labor is the same in all the industries, the wages paid to the workers who worked for manufacturing a car are also accumulated with the raw material cost to calculate the Prime Cost of a car.
- Any indirect cost like selling, administration, advertisements overhead is not a part of this Cost.
Table of contents
Prime Cost Formula
Prime Cost formula = Raw Material + Direct Labor
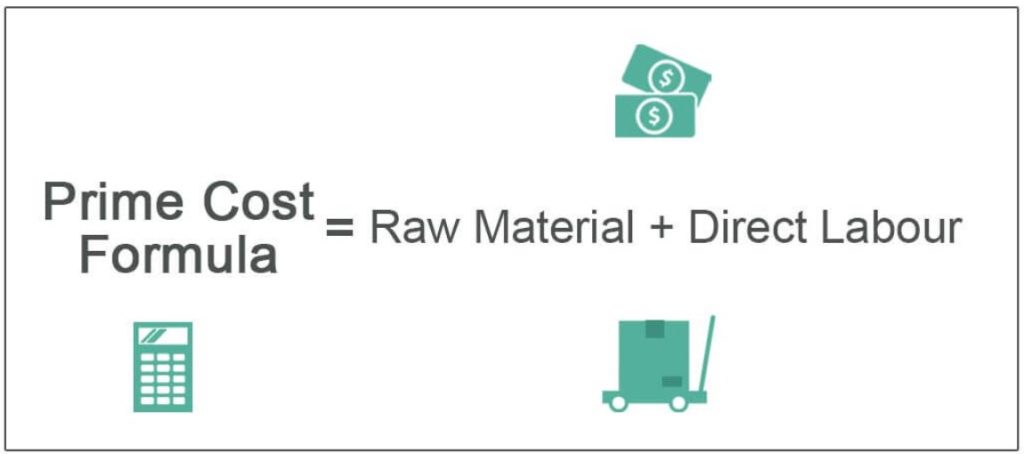
Prime Cost Explained in Video
How to Calculate Prime Cost?
Example #1
A Hypothetical Car Manufacturing Company in India has incurred below expenditures in the year 2016-17 for manufacturing various cars-
Expenditures for Yr 2016-17 | Amt in Rs Cr |
---|---|
Raw Material Consumption | 7500 |
Direct Expenditures | 4250 |
Other Manufacturing Expenditure | 2400 |
Indirect Expenditures | 3500 |
Administrative Expenditures | 5250 |
Finance Cost | 1300 |
Depreciation | 1800 |
To calculate Prime Cost, we have to take figures of raw material consumption and direct cost paid to the workers. In the above example, suppose the company pays 3200 towards direct labor cost out of entire direct expenditures;
- Formula = Raw Material + Direct Labour = 7500 + 3200 = 10700 Crore
Please note - 1 Crore (cr) = 10 million
Example #2
Let us take another example to calculate the Price Cost.
Calculate the Prime Cost of a hypothetical furniture manufacturing company that incurred the following manufacturing expenses for the completion of one of its assignments;
- 5 Labour worked for 30 days
- Labor charges are Rs 1000/- per labor per day
- Wood - 100 sheets @ a cost of Rs 1500/- per sheet
- Glue - 50 Kg @ a cost of Rs 250/- per Kg
Formula = Raw Material + Direct Labour
- = (100*1500) + (50*250) + (1000*5*30)
- = 150000 + 12500 + 150000
- = Rs 312500/-
For an industry like furniture, wood and glue are basic raw materials, and skilled labor is required for making the customized furniture as per the customer's need; without that, furniture could not be produced and turned into finished goods.
Here they use 100 sheets of wood @ a cost of Rs 1500/- per sheet and 50Kg Glue @ a cost of Rs 250/- per Kg. Then five workers work for 30 days at Rs 1000/- per worker per day. We multiply all of these to calculate the amount of direct labor cost. The summation of all the costs is nothing but the Prime Cost.
Important Points to Note
We have taken only direct labor cost out of the entire direct expenditure to calculate Prime Cost. Other costs may be involved in direct expenditure like carriage inward and freight. All other expenditures are part of the indirect expenditure and were neglected at the time of calculating Prime Cost.
- A direct labor cost is a part of both Prime Cost and Conversion Cost. Conversion Cost is a cost needed to convert raw material into finished goods. It includes all the costs to convert the raw material into finished goods except the cost of raw material. Simply it includes direct labor cost and overall manufacturing overheads.
- The production department also uses this Cost as an important tool to effectively frame their costing budgets and implement the overall production process within the ambit of that budget. It also specifies the scope of improvement in the entire production line to reduce the cost of production by using economies of scale.
- Management then analyses the market and determines the customers’ demand, paying capacity, competitors’ pricing, and other strategies to enhance the supply of their products while offering the minimum selling price of the goods. They find break-even selling prices and set margins on the products; below that price, manufacturing, and selling of products would not benefit the company.
6 Reasons that will Influence the Prime Cost
Followings are a few reasons:
#1 - Inflation
Inflation increases the cost of raw materials, and direct labor is more costly during inflation. It is a macroeconomic factor, and the entire economy would be affected by it, and a single manufacturer would not be able to control it. In the case of a recession, the scenario will reverse. Thus price escalation would be the main driving factor of this Cost.
#2 - Shortage of Supply
A short supply of raw material or unavailability of skilled labor may increase the cost of a specific product. It is an industry-specific measure, and manufacturers of other products may not face the same problem.
#3 - Regulatory Actions
Changes in regulatory requirements are uncontrollable, and the entire industry can be affected by them. For Example, the Government makes it mandatory for car manufacturing companies to add pollution control components to their cars. This Cost will increase by the amount of that specific pollution control component available in the market.
Let’s consider the above-stated example of a Car Manufacturing Company in India. Say the company requires to spend Rs 850 Crore on that pollution control component. In such a case, the Prime Cost for production of the car will increase to Rs 11550 Crores in 2016-17.
Prime Cost Formula = Raw Material + Pollution Control Equipment + Direct Labour
- = 7500 + 850 + 3200
- = 11,550 Crores
Please note - 1 Crore (cr) = 10 million
#4 - Taxes
Applicable taxes to purchase a raw material will directly impact the product's Prime Cost. If the taxes and duties paid on the raw material rise, then the subsequent rise in the product cost will be reflected.
#5 - Technology
Technological changes directly affect the Prime Cost, and companies are ready to adopt such changes to compete with the rivalry. An increase in the utilization of high technology machines, instead of direct labor in the production process, improves the entire production cycle more efficiently and saves time and cost of production.
#6 - Exchange Rates
Multinational manufacturing companies operate their businesses in various locations across the globe, and they have to purchase raw materials from different destinations. In that case, foreign exchange rates of the importing countries could significantly impact the Prime Cost of the company.
- For example, a Laptop Manufacturing company in the United States purchases spare parts for a laptop, i.e., raw materials from a Chinese company. If in case, the rate of the Chinese Yuan increases against the US Dollar by 3%, the imported raw material would be more expensive in the hands of a laptop manufacturing company in the United States, almost by 3%.
- Hence the cost of manufacturing a laptop would rise, and the company's laptop gets expensive in the market by 3% or more. In such scenarios, the company may purchase the raw material from countries like Japan, with which currency rates might be stable to maintain the price of laptops in the market.
Conclusion
Prime Cost is the core production cost, including direct raw material and labor costs. It is completely variable as it’s a major component of Cost of Goods Sold. Being a direct manufacturing expense, it is directly related to the number of sales. Unlike a fixed cost, it may be changed according to the company's production targets.
Recommended Articles
This article has been a guide to Prime Costs and its meaning. Here we discuss how to calculate Prime Costs, its formula, examples, and important features. We also explore six primary reasons that impact these costs. You may learn more about accounting from the following articles –