Table Of Contents
What Is A Prevention Cost?
Prevention cost is the expense made by a company with the intention of product improvement and avoidance of any potential quality concerns in its products or services. Hence, it is a proactive approach to ensure quality control, increase customer satisfaction, and build brand reputation.
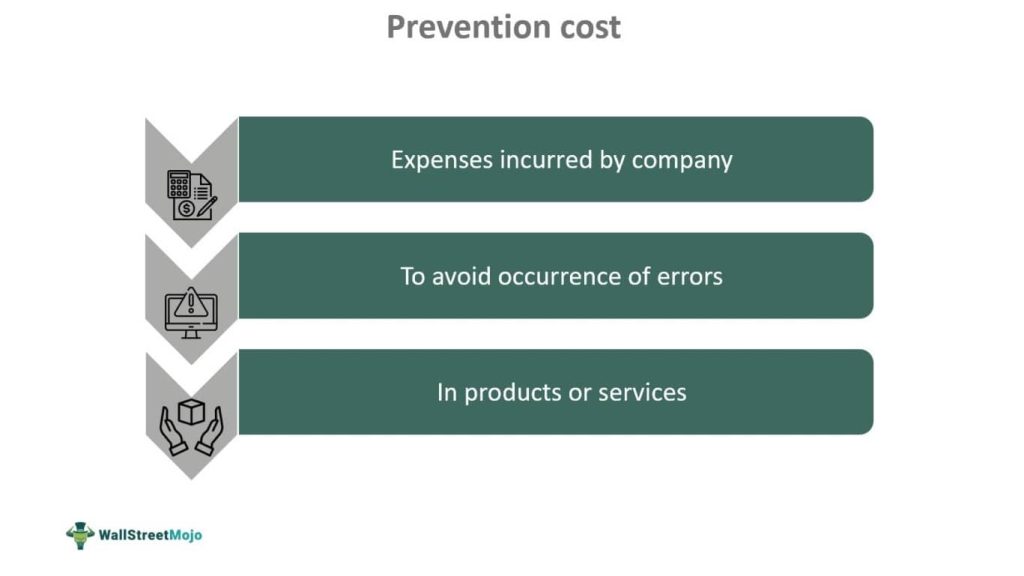
Companies can save time, effort, resources, and money on product or process revision by spending on quality checks, product trials, and other such prevention measures. By investing in prevention, companies aim to improve overall quality. Thus, they reduce the likelihood of defects and ultimately save costs associated with rework, warranty claims, and customer dissatisfaction.
Table of contents
- The prevention cost refers to the money a company invests in enhancing the quality of its products and services by reducing potential errors.
- Moreover, the various expenses made for preventing quality issues and defects include employee training, supply costs, protocol development, equipment maintenance, inspection costs, and quality control assessments.
- It is a proactive approach that differs from the appraisal cost, which involves measures like quality inspection and correction and is reactive to the quality concerns arising after the production of goods or services.
Prevention Cost ExplainedÂ
The prevention cost refers to the costs incurred by companies to reduce errors in the production process. While some industries have strict protocols for maintaining quality standards, many companies self-implement such measures. Hence, it enriches the customer experience and creates a brand image in the long run.
In a business setup, the whole organization is responsible for ensuring quality production. While the top-level management frames the quality standards, the operational-level staff takes charge of following these standards, policies, and protocols. The quality control department is primarily responsible and accountable for implementing the prevention cost, along with other cost of quality (COQ) measures. Furthermore, the engineering department ensures that the product design aligns with the desired quality requirements of usage convenience, reliability, sturdiness, and efficiency.
The companies foresee various challenges in effectively implementing these costs. Also, a small or medium-sized business may need more resources - financial and personnel, to accommodate these expenses. Such an implementation requires constant collaboration and communication, which is mostly between the quality control department and the other departments of the company. To overcome these barriers, the company must assign individual responsibilities and accountability. Indeed, engaging employees in quality improvement discussions can foster a positive approach towards such measures. Therefore, these costs are treated as anticipated investments made by the firm to minimize quality errors before occurring.
In addition, these costs aim to provide a solid quality management system by minimizing the occurrence of quality issues. Hence, they lead to long-term cost savings. Preventive cost accounting is a systematic procedure that includes determining, quantifying, planning, and disclosing expenses, which are related to averting errors and guaranteeing the general caliber of the good or service.
Types
Before launching a new product, the company takes various measures and incurs expenses to ensure that it meets all quality standards. Some of the categories of prevention costs are as follows:
- Employee Training: The company spends money on the training of its bottom-line workers, who are responsible for the production of goods, to ensure quality standards in the assembly and manufacturing process.
- Quality Control Assessment: Customer feedback plays an indispensable role in attaining product precision. Therefore, companies spend time taking feedback and responses from the end users to make further improvements.
- Supply Costs: The quality of raw materials is crucial for maintaining the quality standards of a product. Therefore, the firm may incur some additional costs to source premium quality input.
- Protocol Development: Also, businesses incur expenses on making internal protocols for strictly complying with the quality standards of all employees.
- Inspection Costs: Another critical expense is the inspection of the product at the production stage to check that each component of the product fulfills the desired quality requirements.
- Equipment Maintenance: To ensure the proper functioning of the machinery and equipment, the company incurs expenses on its frequent examination, repairs, replacement, and overhauling.
Examples
Let us understand the concept better with the help of examples.
Example #1
Suppose Silicon Ltd. is engaged in the manufacturing of heaters. The firm implements the following prevention cost to improve the quality and durability of its heaters:
- Sources the heating rods and plugs from a premium supplier at an elevated cost to increase the life of the product;
- Inspection of each component, including plugs, heating rods, switch, and auto cut button, before assembling the heater; and
- Training the engineers to develop new designs that provide better heating solutions and are more energy efficient.
Example #2 - Toyota
Toyota has earned a reputation as a leader in manufacturing durable and reliable SUVs. Building a brand like that is the outcome of its constant investment in the cost of quality, including the prevention cost.
The integration of Toyota Production System (TPS) principles illustrates the prevention cost of quality, ensuring the delivery of high quality at every stage. Additionally, team members are accountable for maintaining excellence within their processes. The principles of Kaizen drive proactive problem prevention and enhancements to the quality management system, fostering creativity and collaboration with suppliers to meet new targets.
Benefits
Prevention costs increase the short-term burden of the company. But they offer way more advantages in the long run. Some of its benefits include:
- Improves Quality Standards: As the company focuses on product precision, it aims to excel in the industry standards. Thus it ensures zero-defect, high-quality offerings.
- Higher Customer Satisfaction: While the customers receive curated products that outperform their expectations, they find it a valuable purchase. Thus, they develop a sense of loyalty and commitment towards the brand.
- Decreases Return: When the customers are happy with their purchase, there is no question of returning the same. Hence, the business may need more return requests.
- Streamlines Manufacturing Process: Spending on prevention can enhance the production process of a firm while bringing down the overall defects and issues in the product.
- Better Brand Reputation: When customers develop trust in an organization for its constant efforts to deliver quality products, the brand value of the company rises tremendously.
- Levels Up Sales and Revenue: Customers have now become quality-conscious rather than being concerned more about the product's price. Such measures can thus directly surge the sales and profitability of the business.
- Provides Competitive Edge: Moreover, investing in quality can distinguish a brand from its competitors in the market, thus enhancing its customer base.
- Reduces Future Cost: If a product fails the market expectations on a quality basis, then recalling, reviving, and relaunching the product after necessary changes involves considerable expenses.
Prevention Cost vs Appraisal Cost
The prevention and appraisal costs together contribute to the quality control and improvement of a company's product or service offerings. However, they differ in the following ways:
Basis | Prevention Cost | Appraisal Cost |
---|---|---|
Definition | It is the early stage expense incurred on reviewing and improving the product quality to decrease the chances of defect or error when it is launched. | Appraisal cost is the expense made on finding any defects or errors in the product and making the necessary corrections after its production. |
Approach | Proactive | Reactive |
Emphasizes On | Avoiding potential quality issues, errors, and defects before the product reaches the market. | Identifying quality issues and suggesting corrective measures after the problem occurs |
Incurred During | Early stages of production | Inspections, tests, and audits conducted during or after the production process for quality issues |
Benefits | Provides long-term advantages like risk management, increased sales, high profitability, substantial brand value, competitive advantage, and cost curtailment | Offer short-term benefits by identifying and rectifying defects before the product reaches the customer, preventing further issues. |
Examples | Employee training, quality control assessment, supply costs, protocol development, inspection costs, and equipment maintenance | Inspecting finished product, examining work-in-progress, staff inspection, quality audits, etc. |
Frequently Asked Questions (FAQs)
Considered as prevention costs, expenses like warranty costs and opportunity costs such as lost sales are excluded. Additionally, these expenses exclude various external failure and appraisal costs.
The prevention cost of quality is the sum of all the expenses directly incurred on performing the actions related to quality checks or improvement of a product before it is introduced in the market. Moreover, it contributes to the total cost of quality (COQ).
Although such expenses add to the production cost, they are critical for the long-term success of a product or service and for building a company's goodwill for quality offerings. Moreover, it can reduce potential future losses and expenditures related to product recalls, returns, improvision, and relaunch.
A quality audit is an appraisal cost since it assures the manufacturer that the product's quality is appropriate for the end users after it is introduced to the market.
Recommended Articles
This article has been a guide to what is Prevention Cost. We explain its examples, compare it with appraisal cost, types, and benefits. You may also find some useful articles here –