Table Of Contents
PDCA Cycle Definition
The PDCA cycle, or the Plan-Do-Check-Act cycle, also known as the Deming cycle, is a management technique used to evaluate and improve business processes and offerings. It is iterative and has to be practiced constantly to get better results. It is practiced by many organizations, especially at the onset of a change.
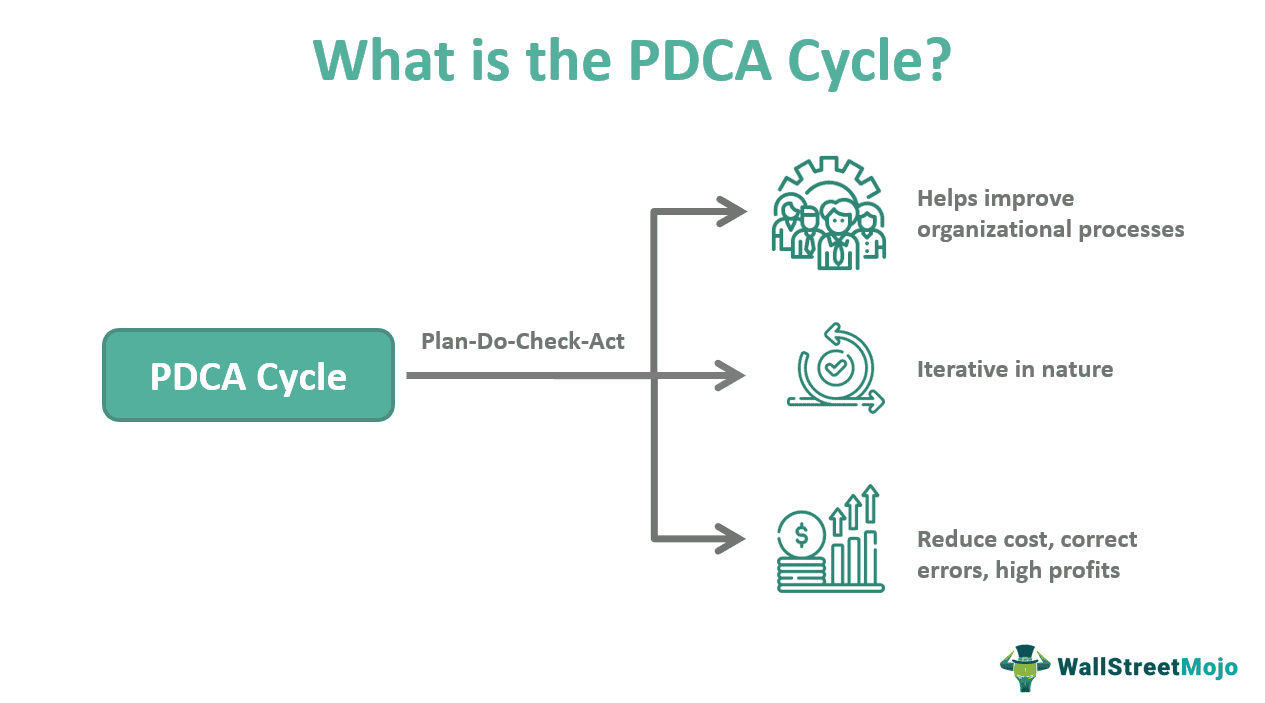
Though originally developed by physicist Walter A. Shewhart, it was popularized by Engineer W. Edwards Deming as a part of quality management. It closely resembles the Japanese management concept of Kaizen. It helps businesses minimize errors and controls performance by setting standards, thus reducing costs and increasing profits.
Key Takeaways
- The PDCA cycle, or the Deming cycle, is a well-known management technique consisting of four steps โ 'Plan, Do, Check, and Act.'
- Usually, there can be confusion between the 'do' and 'act' stages. But the difference is the time of implementation.
- The Deming PDCA cycle is a repetitive or cyclical process, i.e., it should be practiced frequently for successful employment.
- Though there are many PDCA cycle benefits, it has some disadvantages too. Some management philosophers and theorists argue that the system is sluggish and can hamper improvement by becoming routine.
PDCA cycle (Deming cycle) Explained
PDCA cycle was first developed by American physicist Walter A. Shewhart in 1939. However, due to the prominence bestowed by American Engineer W. Edwards Deming - after whom it was named - in the 1950s, many companies started adopting it. Some major examples include Nike, Toyota, Nestle, etc.
One of the features to note is the striking contrast between the Deming cycle and the Japanese business philosophy Kaizen. Kaizen, too, aims for the continuous improvement of organizational processes. Another important feature is that the cycle is not a one-shot technique; it is iterative. That is, it should be followed time and again. The planning especially is to be done considering the situation as and when required.
Apart from that, some processes are continuous. Like regular checks should be done, and countermeasures should be employed. An ideal Deming PDCA cycle calls for the disciplined implementation and the involvement of all parties and units.
How Does PDCA Cycle Work (Steps)
The four PDCA cycle stages are as follows:
#1 โ Plan
Planning is the key to all effective management concepts and business techniques. It is essential in running an organization's new product development, managing the market, and customer relations, communicating with employees, etc. Planning can be referred to as a framework or blueprint for doing things. However, in a company, it implies laying out a blueprint that adheres to the company's ethics, mission, and beliefs.
Planning usually involves setting the objectives, allocating the required resources, identifying the personnel appropriate for the program, laying out a procedure or scheme to manage the entire program, and finally, choosing a deadline. Budgeting, too, is an important part of planning.
#2 โ Do
In the management context, to do means to execute the plan and work. This is probably the part that requires a lot of action and activity. Execution is to an organization what a train is to the people, as it carries the organization forward. But effective planning is significant for proper execution and performance. Every unit should stick to the plan and continuously check the boxes. Apart from working, it is also necessary to record the performance data.
#3 โ Check
To check means to track the performance data. Once a plan is in motion, merely keeping the engine running won't be beneficial in the long run. No system is perfect, and therefore, there is only a certain level of error that an organization can afford to make. Otherwise, it can cost the entity a great deal. This step compares the performance to the standards set up while planning.
First, the management should identify if the objectives are being met. Then it should check on the usage of resources and the cost. The important point is that the management or the team should regularly check the performance. Monthly or biweekly checks would be fine for a long-term project, but for a short-term project, a weekly or a daily one would be necessary.
#4 โ Act
The last step brings the cycle to completion. Acting means correcting the errors identified. The second step of doing can be easily confused with this step. Though the verbal meaning might be the same, they differ in the time of execution. Acting on the mistakes makes a system efficient and the project a success. Mostly, organizations already have a plan to rectify the mistakes or use a new system. Acting can help organizations reduce costs, utilize resources effectively, and achieve better results.
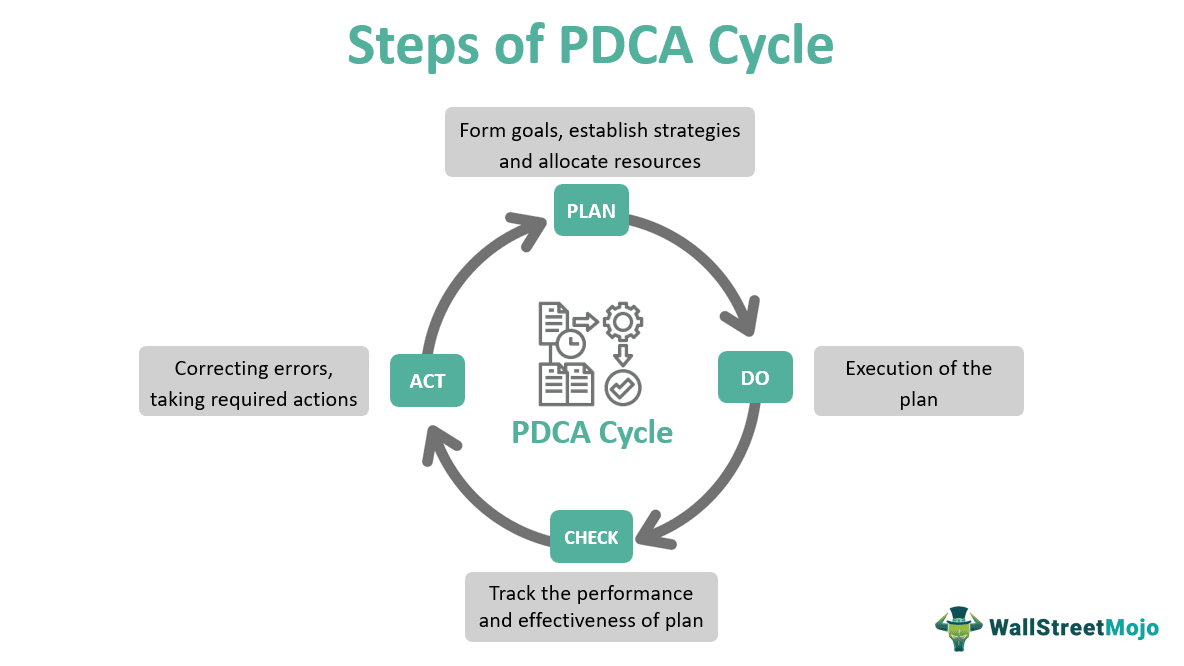
Examples
Now let's discuss some examples of the PDCA cycle.
Example #1
Let's begin with a simple hypothetical example. Company XYZ is well-established in the United States and has around 100 stores. It wants to expand its market to Canada. The management selects a team of 50 people from different departments and gives them a deadline of 6 months.
The team recruits ten individuals from Canada to initiate the project. They employ the Deming cycle, and within a month, the blueprint of the operation is ready. They execute the plan well within the deadline. However, they must constantly follow the cycle for better goal achievement.
Example #2
Recently, the Chinese software company, Infobird's subsidiary company Shanghai Qishuo Network Technology Co., has partnered with one of the world's leading sports footwear brands. The aim is to enhance the digital analysis features of the footwear seller, which reportedly has a presence in more than 150 countries.
The partnership is likely to employ the PDCA cycle of quality management to manage the data. It will also apply other techniques like the GROW (Goal โ Reality โ Options โ Will) model to facilitate the integration and analysis of data. As a result, it is expected that the market revenue of the company will increase by 10.41% from 2020 to 2025.
Deming Cycle Benefits and Drawbacks
Now, let's discuss some of the PDCA cycle benefits:
- It can help cut down costs and reduce the wastage of resources
- It can increase profits and achieve objectives
- It also supports the constant improvement of organizational processes
- It also aids in the faster recognition of errors, thus enabling quicker correction.
Some of the demerits of the PDCA cycle are:
- An improper implementation can be counterproductive
- Some also believe it can hamper out-of-the-box thinking in certain situations and restrict focus to the four steps
- There are arguments that the process might be time-consuming
- The process may not focus much on the human resources involved.