Table Of Contents
What Is Order Cycle Time?
Order cycle time in logistics represents the average duration required to dispatch an order from the moment it is placed. Notably, this metric excludes the actual shipping time, making it a paramount Key Performance Indicator (KPI) for vigilantly monitoring a business's order fulfillment process.
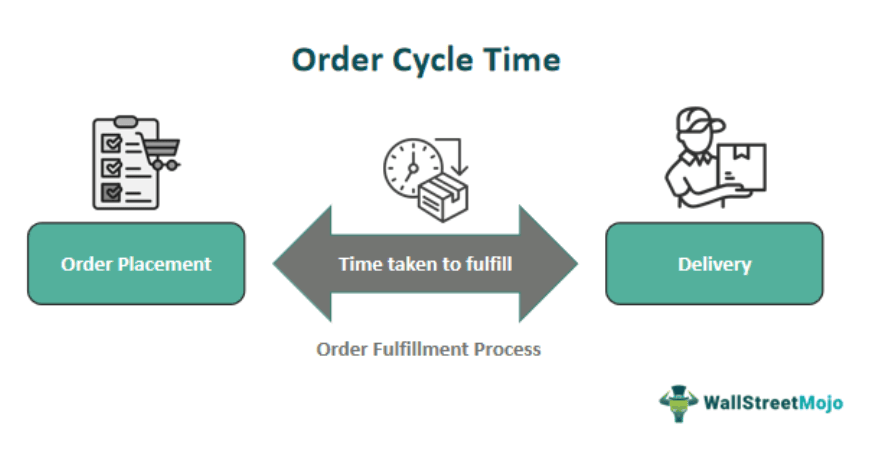
This is a critical parameter for evaluating the effectiveness of fulfillment and impacts other KPIs, such as order lead time and the rate of on-time shipping. Longer cycles cause delays and longer delivery periods, leading to customer dissatisfaction or unhappiness. Shorter cycles reflect higher client satisfaction and help companies be competitive.
Table of contents
- Order cycle time is the average time it takes to ship an order from the moment it is placed to the time of delivery.
- To improve cycle time, businesses can streamline the process, implement an order management system, collaborate with reputable companies, train employees, and optimize warehouse management.
- Enhancing cycle time through the removal or reduction of unproductive tasks can raise customer satisfaction levels.
- Order cycle time and lead time are different concepts. Lead time measures the time it takes for a product to pass through the entire value stream.
Order Cycle Time Explained
The order cycle time in logistics is the time between order placement and delivery. This includes the time required for processing, preparing, sending, and shipping the order. Assuring customer satisfaction in logistics often depends on lowering order cycle time.
It can be measured in various ways. The first method includes calculating the time from when an order is placed until it is shipped. It can be broken down into individual stages, such as receiving the order from the warehouse, picking and packing it, and shipping it. Other methods involve measuring the time of the order placed until the order is invoiced or when the order invoice is received until payment is received. Other techniques include timing the order from when it is placed to the time it is invoiced. It could also be from when an invoice is received to when it is paid for.
In a business process, real work takes up very little of the time elapsed; the remainder is devoted to unproductive tasks. Enhancing cycle time by removing or reducing these tasks can raise customer satisfaction. In addition to quality, cost, delivery, and technological performance, organizations compete on timeliness and performance. Increases in customer satisfaction are a direct result of shorter delivery times for goods and services. Businesses should identify the common reasons for cycle time performance to increase performance.
Formula
The formula for calculating order cycle time is:
Order cycle time = (Delivery date โ Order date)/ Total orders shipped
The calculation involves subtracting the delivery date from the order date, which can be calculated for different periods like monthly or quarterly. Comparing the results to the company's goals helps identify areas for improvement.
Examples
Let us look into a few examples to understand the concept better.
Example 1
Suppose Daisy owns an online shoe store and wants to track and improve her order cycle time in supply chain management. Let's consider a specific order placed by a customer:
The date the order was placed: Monday, 7:00 AM
Delivery date or date received by customer: Thursday, 2:00 PM
To calculate order cycle time, we use the formula:
Order cycle time = (Delivery date โ Order date)/ Total orders shipped
= (Thursday, 2:00 PM - Monday, 7:00 AM)/1
= 3 days and 7 hours
=79 hours
=284, 400 seconds
Example 2
Another example is drawn from a study investigating the impact of order cycle time on the Bullwhip Effect. The study delves into the intricate relationship between order cycle time and the notorious bullwhip effect, considering four pivotal factors: order batching, price fluctuations, demand forecasts, and shortfall anticipation. The "bullwhip effect" manifests when demand variability amplifies as it traverses from end customers to suppliers along the supply chain. Our findings underscore that reducing order cycle time concurrently addresses all four primary causes of the bullwhip effect.
The close interplay between lean production theory and the bullwhip effect, which escalates waste, variation, and costs, forms the backdrop of our investigation. In the realms of supply chain management and the lean concept, time emerges as a paramount performance metric. Specifically, our focus centers on the interval between placing two ordersโorder cycle time. A shorter order cycle time not only aligns with the principles of Kanban but ensures continuous improvement, and quality control, accelerates material flow, diminishes inventory levels, and fosters uniform workloads in production. This strategic reduction in order cycle time is a potent tool for mitigating the bullwhip effect in supply chain management and curtailing system variability.
How To Improve?
Outlined below are key measures to enhance cycle time efficiency:
- Streamlining the Process: Initiate the efficiency enhancement process by meticulously analyzing each step in the order process. Identify areas that can be optimized and simplify and streamline these procedures to reduce downtime and boost overall efficiency.
- Efficient Order Process: Implementing an advanced order management system, fostering strong supplier relationships, ensuring precise inventory management, and incorporating real-time tracking are essential steps to enhance efficiency in procurement and delivery processes.
- Shipping and Logistics: Collaborate with reputable shipping companies to ensure prompt and effective delivery. Establish efficient product handover and tracking procedures while negotiating competitive pricing.
- Employee Training: Provide comprehensive training for employees involved in order fulfillment, equipping them with necessary skills. Regularly monitor cycle time metrics to identify areas for improvement and promptly implement necessary changes.
- Warehouse Management: Optimize warehouse layout to reduce order picking and packing time. Strategically arrange products based on popularity and address inventory management bottlenecks. This streamlines operations, enhances customer satisfaction, and minimizes walking paths.
Order Cycle Time vs Lead Time
Differences between these two concepts are outlined below:
Concept:
- Order Lead Time (OLT): Measures the time it takes for customers to physically receive their orders after placing them.
- Order Cycle Time (OCT): Measures the time it takes to prepare items for shipping.
Essence:
- OLT: The duration for a product to traverse the entire value stream, from order placement to the receipt of the last payment.
- OCT: The interval between order date and completion of order processing, encompassing order receipt and processing.
Consumer's Role:
- OLT: This begins when a consumer places an order. Customers experience lead time, even if a business is aware of its lead and cycle times.
- OCT: This represents the time it takes for a client to receive a purchase order, with customers generally not directly involved in the computation. It focuses on the manufacturer's readiness to dispatch the product.
Frequently Asked Questions (FAQs)
It is crucial for assessing efficiency in the fulfillment process. It measures the time from order placement to delivery, influencing customer satisfaction and operational effectiveness. A shorter cycle signifies streamlined processes, quicker deliveries, and enhanced competitiveness, contributing to improved customer experiences and increased operational agility in today's fast-paced business environment.
Flow time and order cycle time are concepts used to measure the time aspects of processes, especially in supply chain and operations management. Flow time represents a product or service's total duration to move through an entire process, encompassing all production or service delivery stages, excluding any waiting or idle time. On the other hand, order cycle time specifically pertains to the time required for customer order fulfillment, from the order placement to the final delivery.
Optimizing it without sacrificing accuracy involves streamlining processes and leveraging technology. Implement efficient order processing systems to reduce manual handling, automate repetitive tasks, and minimize errors. Utilize advanced inventory management to ensure accurate stock levels. Opt for real-time tracking and monitoring tools to enhance visibility across the supply chain. Continuous process evaluation and adjustments will help balance speed and accuracy, enhancing overall order cycle time efficiency.
Recommended Articles
This article has been a guide to what is Order Cycle Time. Here, we explain its formula, comparison with lead time, its examples, and how to improve it. You may also find some useful articles here -