Table Of Contents
What Is Material Requirement Planning (MRP)?
Material requirements planning or MRP is a computerized system that allows manufacturers to plan, manage, and control their inventories more efficiently. It, thus, helps them schedule the manufacturing per bills of materials and deliver the right product at the right time and the best possible price.
This manufacturing decision-making process compares existing raw materials and components required to produce goods with the production capacity based on the demand forecasts. Besides helping understand inventory levels, the system lets producers optimize labor requirements. Its purpose is to enhance the productivity of a business and reduce superfluous inventory while maintaining the supply-demand cycle.
Table of contents
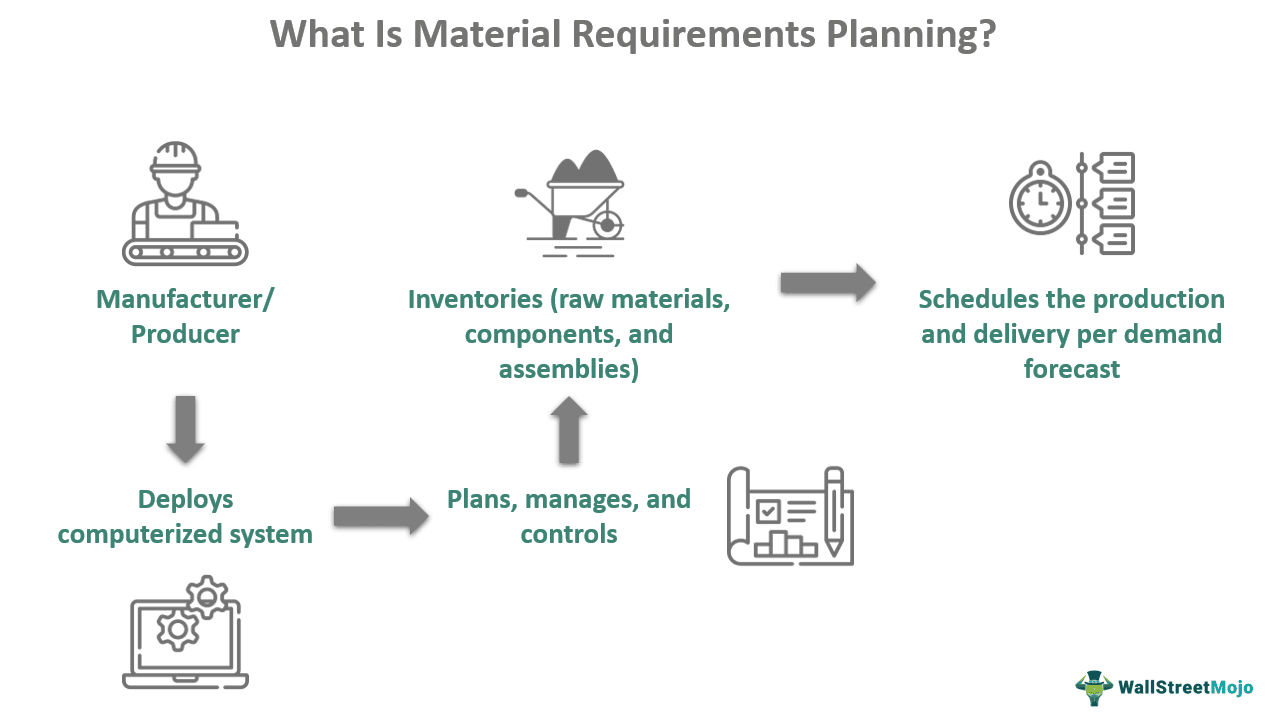
- Material requirements planning or MRP is sales forecast-based software that helps manufacturers plan, manage, and control their inventory based on the demand forecasts.
- It assists producers in scheduling production according to the bills of materials and delivering the right product at the right time and the optimal price.
- It improves production efficiency and reduces excess inventory and lead times while sustaining the supply-demand cycle.
- Other benefits of MRP include product customization, lower overhead expenses, and timely delivery of finished products to customers.
How Does Material Requirement Planning Work?
Material requirements planning software forms an essential part of inventory management. As long as raw materials are available, these could help develop finished goods. If they are more than required, other producers in the same niche or industry can use them.
Ideally, the demand and supply chain remains in sync when there are sufficient stocks. However, when there is an excess of final products produced and made available, it gets wasted. On the other hand, if stocks are short on supplies, customers are likely to switch to other brands. Loss of customers can result in loss of business. Therefore, it is crucial to have adequate stock or inventory to meet demand and keep the supply chain running smoothly.
MRP helps the producer analyze various factors to prepare the demand forecasts. It calculates the inventory, schedules the production, and ensures that finished products reach the right place at the right time and at the lowest possible cost. In other words, it allows the company to understand the type, quantity, and delivery of a given product to fulfill the consumer's needs.
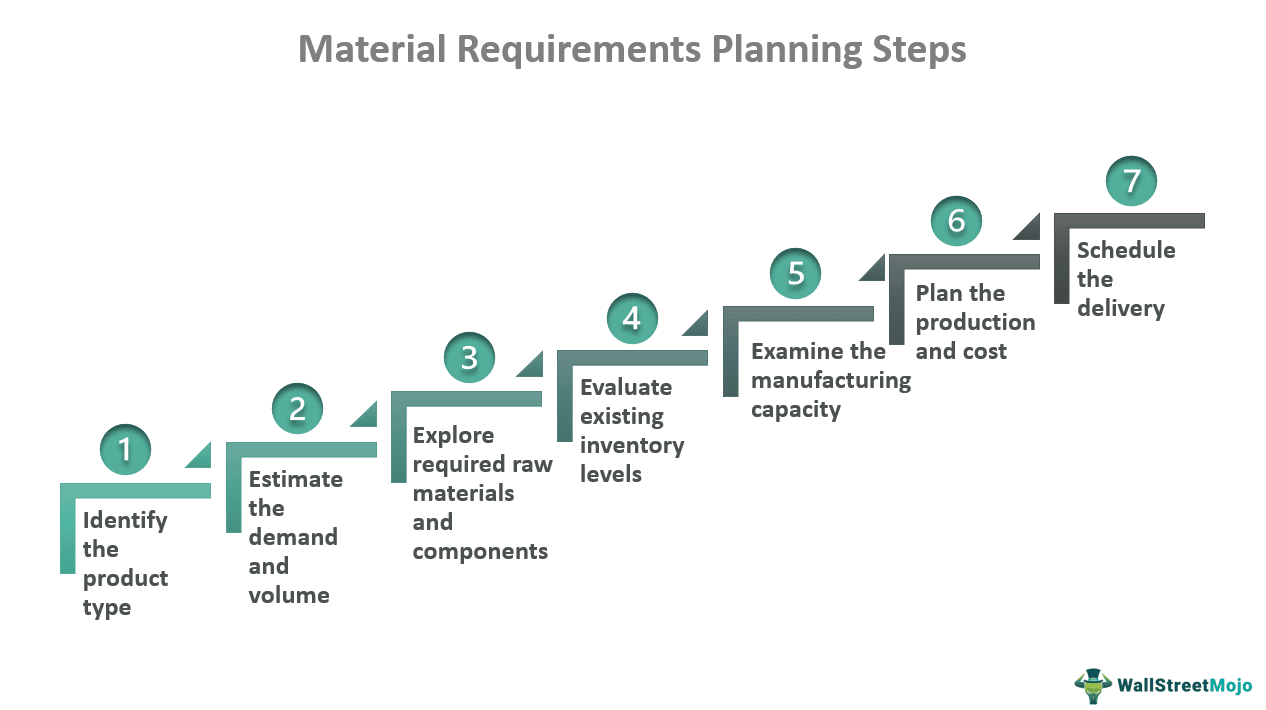
Examining existing inventory levels and the manufacturing capacity of a unit is critical to production. The first stage in the process is to determine what to manufacture to develop the inventory. MRP then examines the current market demand to determine the volume. The next step is to figure out quantities of raw materials and components required to produce finished goods. Finally, the unit plans the production (based on the bill of materials), cost, and delivery of products. Overall, it leads to efficient production and inventory optimization while satisfying the demand.
MRP Inputs, Objectives, And Benefits
Inputs for Production | Objectives | Benefits |
---|---|---|
Product type | Keeping the material and component levels as low as feasible | Reduced inventory and overhead costs |
Quantity and delivery | Making raw materials readily available for production | Improved production cycle |
Inventory status | Scheduling manufacturing, distribution, and purchases | Sufficient stocks to meet the demand |
Stock shelf life | Reduced lead times | |
Bill of materials | Customer satisfaction | |
Production plan |
You are free to use this image on your website, templates etc, Please provide us with an attribution link
Material Requirement Planning Examples
Let us consider the following material requirements planning examples to get an in-depth insight into the concept:
Example #1
Sharon, the proprietor of a clothing store, creates and sells a wide range of clothes. In a short time, her shop became well-known among the local ladies. However, when she began accepting online orders, operating the store became more difficult. Despite her best efforts, she could not deliver the products on time as she struggled to keep track of the demands. As a result, she produced more similar clothes based on the variety of demand resulting in excess production and further losses.
Her friend Lisa, who was more into using technology to solve business challenges, suggested using the material requirements planning system. Sharon did so and prepared a bill of materials to understand the type, quantity, and delivery time. The computerized system did all computations and let her know how to maintain the demand and supply chain.
Example #2
MRP enables firms to make well-informed decisions about inventory management, production planning, and delivery of finished goods. Using an outdated system, however, may cause manufacturing issues during supply chain disruptions.
For instance, the COVID-19 epidemic halted the import of raw materials and components, affecting the manufacture of products worldwide. As a result, manufacturers have little choice but to switch to advanced software or integrate modern functions to deal with such incidents. One method is to optimize raw material management and leverage diverse systems to cut costs while developing responsive supply chains.
Pros and Cons
Here are a few advantages and disadvantages of the material requirements planning process:
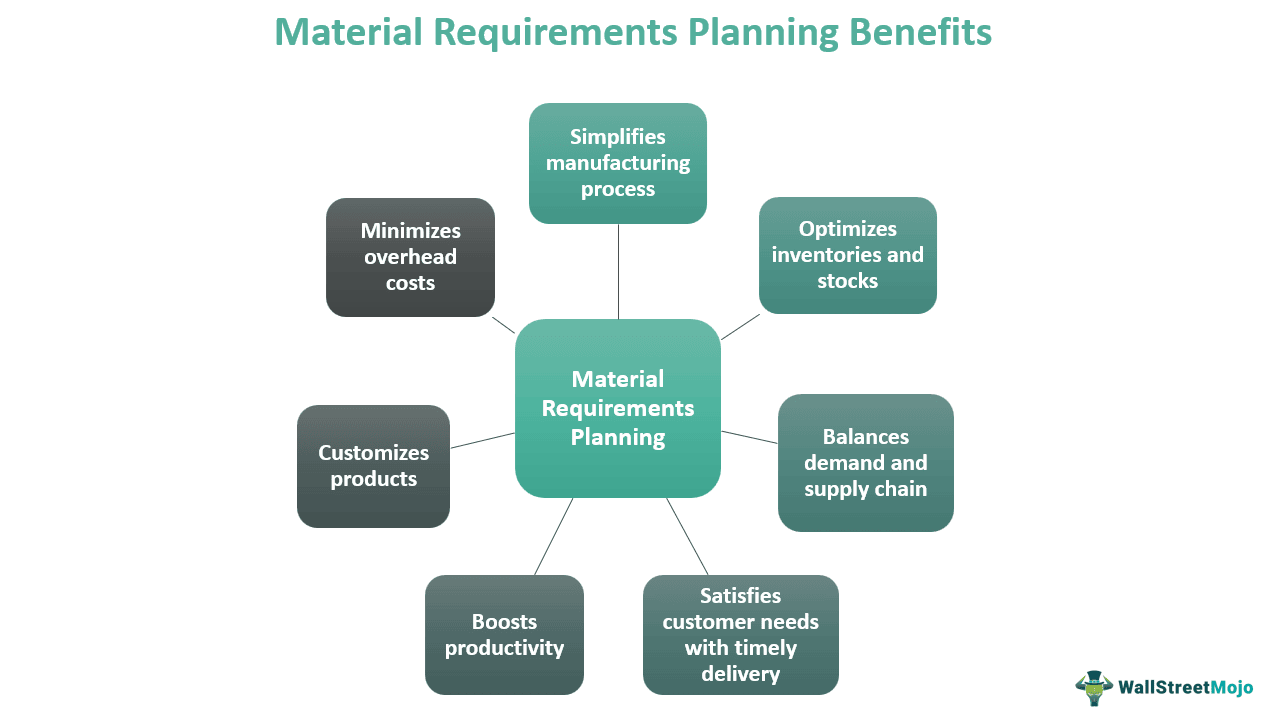
Pros
- Assesses the volume beforehand
- Balances the demand and supply chain
- Enhances the productivity
- Guarantees customer satisfaction
- Helps in product customization
- Maintains inventory levels
- Turns complex manufacturing processes into simple
- Minimizes overhead costs
- Delivers products on time
- Prevents wastage of inventories and stocks
- Provides a time estimate for production and distribution
- Reduces lead times
Cons
- Expensive to deploy and complicated to use
- Incorrect data can provide inaccurate demand estimate
- Needs proper training and regular maintenance
- Requires accurate data
- Wrong inputs can delay production and shipment
Frequently Asked Questions (FAQs)
Material requirements planning is a digitally controlled inventory management system that enables manufacturers to compare existing raw materials with production capacity based on demand projections. After which, they can plan and schedule the production and distribution of finished goods. Its main advantage is to help businesses avoid excess inventory and boost productivity.
The basic steps of MRP are as follows:
- Determining the product type
- Calculating demand and setting volume
- Identifying required raw materials and components
- Checking existing inventory levels
- Examining the manufacturing capacity
- Planning production
- Scheduling delivery
MRP assists the producer in analyzing several parameters to develop demand forecasts. It enables a company to understand the type and quantity of a specific product, estimate inventory, schedule manufacturing, and ensure that finished goods arrive at the appropriate location at the right time and at the lowest possible cost to meet the market demand.
Recommended Articles
This has been a guide to material requirements planning and its definition. Here we discuss how does MRP work, along with examples, objectives, benefits, and pros & cons. You may also have a look at the following articles to learn more -
- Inventory Control
- Inventory Management
- Inventory Shrinkage