Table Of Contents
What Is Marginal Costing?
Marginal costing in economics and managerial accounting refers to an increase or decrease in the total cost of production due to a change in the quantity of the desired output. It is variable, depending on the inclusion of resources required to produce or deliver additional unit(s) of a product or service.
Calculating marginal cost enables managers to make decisions on resource allocation, optimize the production and operation, control manufacturing costs, plan budget and profits, etc. It considers expenses incurred at each production stage, except for overhead pricing. The practice is common in manufacturing industries, allowing companies to achieve economies of scale.
Table of contents
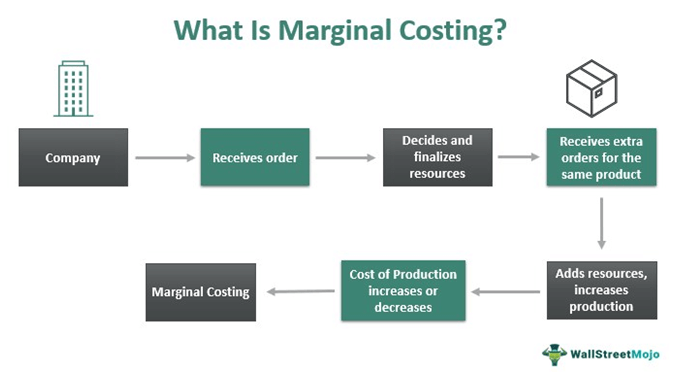
- Marginal costing is the increase or decrease in the overall cost of production due to changes in the quantity of desired output.
- Managers can use it to make resource allocation decisions, optimize production, streamline operations, control manufacturing costs, plan budgets and profits, and so on.
- In most cases, variable costs influence marginal costs. It can, however, consider fixed expenses in circumstances of increased output.
- When a company's marginal cost equals its marginal income, it maximizes profits while setting the selling price of a product or service.
How Does Marginal Costing Work?
The marginal costing technique is crucial for any business aiming to optimize the production of goods or delivery of services. The concept technically means extra costs added to the production cost due to additional unit(s). It helps companies determine the selling price of a product or service. Furthermore, they can estimate the desired output by understanding marginal and sales costs. It simply works like this:
- Sale or Unit price > Marginal cost = More production = Profit
- Marginal cost > Sale or Unit price = Less production = Loss
Moreover, entities can calculate the price associated with resources needed to scale up the production of additionally ordered items. Also, it enables managers to estimate production expenses and budget, avoiding last-minute resource shortages.
Marginal costing varies with the production level and volume. Based on this, it can be either short-run (i.e., fixed costs for additional production in a short time) or long-run (i.e., variable inputs for extra output in more time).
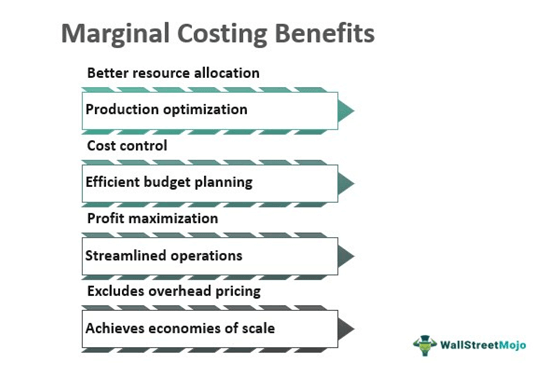
In the other context, it is an essential tool for companies to maximize profits and achieve economies of scale. It happens by producing to the point where the marginal cost equals marginal revenue. Manufacturing and selling an additional unit of a product or service generates marginal or sales revenue.
Marginal Costing vs. Absorption Costing Explained in Video
Marginal Costing Factors
In the production process, some resources remain constant regardless of how many extra orders the business receives. Such resources involve fixed costs that do not change with the production quantity, resulting in increased output. These mainly include overhead, administration, and sales costs.
On the other hand, the company may require a few resources to enhance the production speed for additional orders. Buying and maintaining these resources involve variable costs that keep changing with the output volume, increasing expenses. These usually include raw materials and labor costs.
For example, baker Maria, on regular occasions, bakes 20 cakes per day. Hence, she has a small plant, 2 baking machines, and 7 employees to handle daily orders. However, during the Christmas season, Maria receives the order of 50 cakes per day for as long as the New Year hangover continues. To speed up the process, she employs 8 more employees, who she needs to pay for the season, along with buying 3 more machines, which involves another significant investment from her side, while her plant does not change.
In this example, adding new staff and machines involves variable costs. It eventually adds to the total cost of production, contributing to Maria’s marginal cost. The cost of the plant, on the other hand, remains fixed without affecting the overall manufacturing cost.
Marginal costing typically considers variable costs in its calculation. However, it can include fixed expenses in the cases of enhanced production.
Equation Of Marginal Costing
Marginal costing signifies the change in the overall production cost due to a variation in the desired quantity of goods or services. Companies perform financial modeling to maximize cash flow generation using the following equations:
Marginal Cost (MC) = (Change in Total Costs) / (Change in Quantity)
Or,
MC = ΔTC/ ΔQ --------------------------------- Equation (I)
Where,
- TC = Total cost
- Q = Quantity
- Δ = Incremental change of producing one additional unit
The total cost of production is the sum of both fixed and variable costs, depending on the desired output. Marginal cost is directly proportional to the variable cost occurring at every production level. So, let us have a look at another equation to check out the interrelation between both:
TC = FC + (Q x VC) ------------------------------ Equation (II)
Where,
- FC = Fixed cost
- VC = Variable cost
Combining both equations I and II together, we get:
- MC = ΔTC/ ΔQ = VC --------------------------- Equation (III)
Equation III shows how TC is directly proportional to VC. It means the total cost will automatically increase if the variable cost increases and vice-versa.
Calculation Example
Calculating marginal cost involves dividing the change in production costs by the variation in the desired output. Here is a marginal costing example with the step-by-step calculation:
Sam owns an automobile company. He manufactured 10 four-wheelers worth $400,000 in the first year of business. The total cost involved in the making of those sedans was $180,000. In the second year, he sold 20 vehicles worth $800,000. This time, the total cost he incurred in manufacturing them was $360,000.
Here, the change in the total cost of production:
- = $360,000 - $180,000
- = 180,000
The change in quantity:
- = 20-10
- = 10
Using the marginal costing equation,
MC = ΔTC/ ΔQ
We get,
- MC = $180,000/10
- = $18,000
Therefore, $18,000 is the MC per sedan.
Advantages And Disadvantages
Correct marginal costs estimation can help managers develop budget and profit plans for the next production cycle. It means an inaccurate calculation can lead to massive losses to manufacturing units. Thus, it has both pros and cons, which are as follows:
Advantages | Disadvantages |
---|---|
Classifies costs as fixed and variable | Efficiency of resources and other factors could also affect the marginal cost |
No overhead pricing included | Does not consider time as a factor |
Easy cost ascertainment | Not suitable for all sectors |
Helps in effective decision-making, whether it is to replace a machine or discontinue a product or service | |
Cost comparison becomes easy |
Frequently Asked Questions (FAQs)
Marginal costing calculates the change in the overall production cost owing to variation in the volume of the targeted output. The price varies depending on the number of products. Marginal costs include expenses incurred at each production stage due to changes in resources needed to create the required additional quantity of products or services.
In accounting, marginal costing is a variable expense applied to the unit cost. The quantity produced by removing marginal cost from the product's selling price is referred to as a contribution. In this situation, the contribution completely offsets the fixed cost.
The marginal costing technique considers variable costs as the actual production cost. In contrast, absorption costing is the method that considers both variable and fixed costs as part of the production cost.
Recommended Articles
This has been a guide to what is Marginal Costing and its definition. Here we discuss how it works along with its formula and example. You can learn more from the following articles -