Table Of Contents
What Is A Make or Buy Decision?
A Make or Buy Decision refers to a decision made to either manufacture a product/ service in house or buy it from outside suppliers (outsourcing) based on cost-benefit analysis. This decision is made using quantitative or qualitative research and most of the time, the results of quantitative analysis (cost-benefit analysis) are enough to decide on whether to make the product in-house or buy (outsource) from outside suppliers.
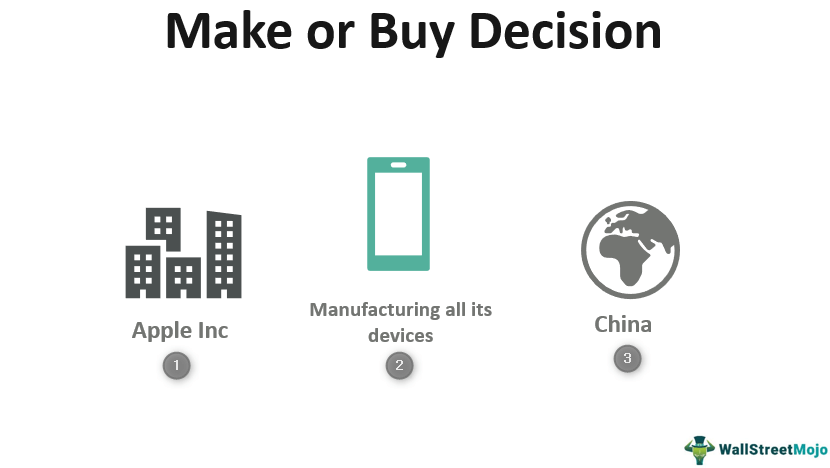
Whether an entity or economy decides to buy a product or service from external sources or manufacture it at its own unit completely depends on the expenses involved. If the manufacturing costs involved seem fine with respect to the benefits the products offer, the entities agree to manufacture it, else they prefer buying it from other entities or nations.
Make or Buy Decision Explained
The Make or Buy decision applies to both goods and services. Businesses compare the cost and benefits of producing the goods or services within the company and the cost and benefits of getting an outside supplier to supply the goods and services into consideration. The value here must include all the fees associated with manufacturing (including material, labor, cost of machinery and space), storing, moving, taxes, etc. and the corresponding benefits must include benefits in terms of increased margins (for in-house production) or low capital requirement (for outsourcing).
Let's discuss the analysis of make or buy decisions.
- Under quantitative analysis, businesses consider all the costs associated with producing the product or service in-house. These costs include buying and maintaining equipment, cost of the premises (lease, etc.), raw material cost, conversion cost, cost of fuel and electricity, labor cost, warehousing or storage cost, shipping cost, and the cost of capital. The benefits include higher margins from in-house production.
- The cost associated with outsourced production includes the product and service, transportation, warehousing, and storage and labor costs for managing the logistics.
- The decision becomes a little straightforward if the company does not have an idle capacity to produce the product or service. In this case, the management can opt to hire an outside supplier considering that it is not of critical importance, and the firm’s intellectual property is not endangered.
- Considering the company has the idle capacity, and it is already incurring a large part of fixed expenses, it can choose to manufacture in the house if the marginal cost of manufacturing is less than what it will cost to buy from outside suppliers.
Factors
The make or buy decision should be taken with utmost care keeping the long-term and short-term benefits into consideration. There are pros and cons to both making and purchasing; however, generally, businesses tend to outsource functions where they do not have a core competency or when the cost of procuring the components or services from outside suppliers is significantly cheaper.
There are multiple factors that make individuals, entities, and economies assess what option would be better for them – to make themselves or to buy from other manufacturers. When the entities decide to make a product or offer a service themselves, they inspect various aspects and assess the cost involved in conducting the manufacturing or production procedure. If the expenditure seems worthy of the benefits and usage frequency of items, the countries decide to do it by themselves.
On the other hand, if entities or nations find out that the benefits and usage frequency do not require them to invest so much into the production or manufacturing of items, they find it better to have an external source hired for the items.
Make Decision
The following are the major factors considered while deciding to make the good or service in-house.
- Cost concerns are one of the most important factors. If the businesses find it too expensive to outsource the manufacturing or production activities, they skip the buy idea and manufacture the products themselves.
- Their desire to enhance the manufacturing focus inspires them to manufacture their own products.
- Most businesses fear their intellectual belongings being roped. Such concerns disallow them to outsource processes.
- Many times, businesses are not sure of the quality the outsourcing company would offer. Any tampering with the quality directly hampers a business’ image or a nation’s image. The quality concerns, therefore, forbid them to buy from others.
- Not all suppliers are reliable. This is a reason enough to not trust a third party.
- The need for direct quality control over the product. When there is another unit working on the manufacturing of the products, the main business loses supervision control, which may affect the quality of the products and services offered.
- The absence/shortage of competent suppliers can be yet another reason.
- The volume of product required might not be significant enough for a prospective supplier to take orders.
- When the shipping and transportation costs are reasonable enough to handle, companies prefer making products rather than buying them from an external business.
Besides the above-mentioned major reasons, there can be other factors too affecting the make or buy decision. Such factors include environmental determinants, political reasons, etc.
Buy Decision
The following are the major factors considered when deciding to buy the goods or service from an outside supplier.
- The first and foremost reason that makes a business or nation opt for buying products and services from external sources is their own lack of expertise in manufacturing those categories of products and services. They know they cannot yield the best. Hence, they connect with the best providers for their consumers.
- When companies decide to outsource their manufacturing process, they do thorough research to check who’s the best provider of the required products and services. The research and specialized know-how of the supplier better than the buyer is what inspires them to delegate their manufacturing service to other brands.
- Cost considerations are always one of the main concerns. If the businesses or nations find that it is less costly for them to buy the products and services from an external source than to produce themselves, they consider the former option and hire a third-party service.
- There are situations where a business is incapable of manufacturing an item itself. This is when they have to look for some other entity that could look after its manufacturing obligations.
- When the goods are not required in large numbers, the businesses find it worth having an external source of production of the products. This is because there is no use in devoting much time and effort to arranging everything from scratch for producing an insignificant volume of goods. Hence, they prefer outsourcing services.
Besides the above-mentioned reasons to consider buying products from external sources, the company may also think that a particular product category is not much important to the firm’s strategy. Hence, they prefer outsourcing the production of the same. Plus, they may have a personal liking for the brand that inspires them to outsource the manufacturing to that particular external brand.
Examples
Let us discuss the following examples to understand the make or buy decision meaning better:
Example #1
As stated earlier, there may be some factors at play that may influence a company’s company’s decision to make an item in the house or outsource it.
Under such circumstances, two factors are to be considered:
- Whether surplus capacity is available and
- The marginal cost of per unit manufacturing
Assume a company is deciding between manufacturing a part in-house that costs $26 per unit, including direct cost, fixed overheads, and variable overheads, as given in the table below.
Cost Head | Cost per Unit ($) |
---|---|
Direct Cost | 15 |
Fixed Overhead | 4 |
Variable Overhead | 7 |
Total Cost | 26 |
The same part is available in the market at $23 per unit, including the cost of buying, shipping, and warehousing, as shown in the table below.
Cost Head | Cost Per Unit ($) |
---|---|
Cost of Part | 20 |
Shipping and Warehousing Cost | 3 |
Total Cost | 23 |
Should the Firm Make or Buy the part?
Analysis
If surplus capacity available will remain idle if the component is bought, out of pocket expenses will be $23 per unit, $1 more than the variable and direct cost of making component which is $22 ($15 + $7). Hence it is economical to make it. However, if the Firm is utilizing or can utilize the capacity in making some other part which contributes to say $4 per unit in profits, the effective cost of buying the component will be $19 ($23 less $4 contribution from other products). In that case, it would be economical to buy the Component at $23 per unit from outside.
The relevant calculation for making decision may be as follows:
Particulars | Make ($) | Per Unit Cost Buy & Leave Capacity Idle ($) | Buy and Use Capacity for Other Product ($) |
---|---|---|---|
Cost of Making/Buying | 22 | 23 | 23 |
Contribution from other Product | - | - | 4 |
Net Relevant Cost | 22 | 23 | 19 |
Example #2
The smartphone giant Apple Inc. outsources the manufacturing of all its devices to China because manufacturing is not its core competency. It is also significantly cheaper to assemble the tools in China due to substantially lower costs. Apple designs its produces in its office in the United States; the products are then manufactured in China and shipped back to the United States and other countries for sale.
Advantages and Disadvantages
Make or Buy decision has many benefits to offer to businesses as it gives them a chance to decide to either buy or make products and services, given the various factors or situations. However, at the same time, there are certain limitations to this process. Thus, companies and economies must understand which option would be fruitful for them in the future. To achieve this, they must consider all the factors mentioned above for making the right choice.
Let us have a look at both the advantages and disadvantages of the process below:
Pros
- The finding helps choose the most efficient option to go about in-house production or outsourcing.
- The decision helps in the strategic maneuvering of the business.
- The decision helps save the cost for many businesses.
- Businesses benefit from the lower cost of mistakes if they think strategically about this decision.
Cons
- In case the companies make a wrong choice, they have to bear huge losses. For example, if they are not an expert in producing something and still opt for it out of pride or emotional bent, they have to bear costly repercussions.
- They lose supervision control of products when an external source is handling the production.
Recommended Articles
This has been a guide to what is Make or Buy Decision. Here, we explain the concept with examples, factors, advantages and disadvantages. You can more about finance from the following articles –