Table Of Contents
Lead Time Definition
Lead time is the period between the initiation of a process or order and its completion or delivery. It is an essential aspect of managing production, supply chains or inventories, and projects in any business, regardless of industry. Eventually, it helps them beat the competition and avoid stockouts.
Businesses calculate and reduce the lead period to meet consumer expectations and maintain their market presence. Besides, it enhances production efficiency and boosts sales revenues. However, many factors can contribute to long lead periods, such as delays in supply, production, and delivery, affecting manufacturing and sales. People confuse it with the throughput or cycle time, which is the amount of time taken at each stage to complete the process or order until the product reaches the customer.
Table of contents
- Lead time meaning refers to the period between the initiation of an order, process, or project and its successful delivery or completion.
- It is different from the throughput or cycle time, which is the time taken at different production stages to complete the process or deliver the order to the customer.
- The significance of the lead period varies depending on the sector or industry, whether it is manufacturing, supply chain management or inventory control, or project management.
- Operation overlapping and operation splitting can help reduce the lead period besides monitoring the production processes at each stage.
Understanding Lead Time
A company must fulfill consumer requests and orders on time to earn market credibility. Understanding demand for products and ensuring their availability in the market is the best approach to do this. It involves taking care of time invested in production processes and supply chain management.
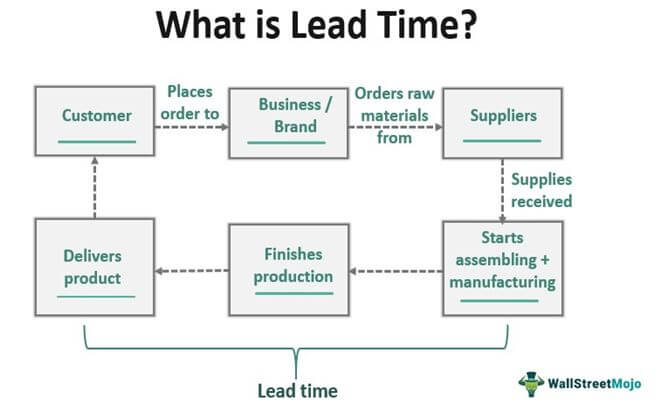
Lead time is a critical component in determining how long it will take a company to start and finish an order, process, or project. In short, this period directly affects how effectively a brand satisfies the needs of its customers. The smaller the lead period, the better it is for the business. Other benefits include increased productivity and profits.
The significance of lead time for delivery varies depending on the niche in which it gets applied. Whether manufacturing, inventory control, or project handling, knowing the lead period can make a big difference in every segment.
Manufacturing
In manufacturing, it refers to the total time taken to source raw materials, assemble pieces stage-by-stage, manufacture finished goods, and deliver to customers. These phases are:
- Pre-processing stage (receiving of supplies)
- Processing stage (manufacturing and assembling of parts)
- Post-processing stage (shipment and delivery of finished products)
As soon as the customer requests a product, the business places orders for raw materials from the supplier(s). Once the company gets the supply, the manufacturing unit assembles them to configure and create the final output.
When the final output is ready, it goes for shipping, which takes an ample amount of time. In this case, the lead period would range from order placement to its delivery to the customer.
Manufacturing Lead Period/Time (MLT) = Pre-processing time + Processing time + Post-processing time
A business needs to keep the manufacturing lead period shorter to witness a jump in product sales.
Supply Chain Management
A brand must take care of the supply chain management (SCM) to ensure the timely availability of products to customers. In SCM, the lead period is the latency between the demand created (order placement to replenish products) and the supply made (readiness of the order in the warehouse for delivery).
As delays might occur when the inventory is unavailable, reducing the lead period helps businesses avoid stockouts. The poor handling of stockouts could make a brand lose out on its customers. It will ultimately thereby affect its market reputation. In such a case, it would be better to reorder the stock and build the supply chain even before the current stock is over. Here, vendor management inventory software can help in the process.
For example, Kelly is looking for a moisturizer that she has been using for quite a long time. But the same is out of stock in the market. So, she might decide to go for some other brand, with no guarantee that she would return to the old one.
SCM Lead Period/Time (SCMLT) = Delay in Reordering (the period before ordering supplies) + Delay in Supply (the period between ordering and receiving supplies)
The COVID-19 pandemic has severely impacted the global supply chain. Not only did the virus force many manufacturers to place backorders, but it also resulted in reduced productivity and increased shipping rates. Contrary to popular belief, experts suggest businesses adjusting lead periods and supply chain costs for customer strategies to deal with the situation.
Project Management
Even though the concept of the lead period is prominent in industrial sectors, it plays a crucial role in project management. In this case, it considers the time taken to complete a particular task or a set of interdependent tasks from the moment of being assigned.
Based on the deadline, the task gets allocated to different teams. The team leader further delegates the assignment to fellow members and makes sure each member delivers the output on time. The teams try to include a buffer period if there is any delay caused due to any unpredictable circumstances. Once the result is in, they test it for final delivery to the client.
Project Management Lead Period/Time (PMLT) =
How To Reduce Lead Time?
If it exceeds a particular time, the lead period can hamper the market reputation of a business. Therefore, a brand must keep it as low as possible. Besides reviewing production stages at regular intervals, there are two established ways to do so - operation overlapping and operation splitting.
1. Operation Overlapping – It is the beginning of the second operation even before the first one is completely over. After deciding lots and achieving the number, the second operation begins.
For example, if a business has to manufacture 50 pens, it can choose to move to the next set of operations, i.e., shipping the items as soon as production of 25 pieces gets done. This way, it can make pens available to customers even before the next set of products hits the market.
2. Operation Splitting – In this case, the order gets divided into two or more lots and is processed using multiple machines simultaneously. It reduces the lead period to a great extent.
Other strategies that can help a business reduce the lead period include:
- Placing smaller orders for raw materials or replenishing products
- Connecting with local suppliers to source inventory
- Switching to fast shipping methods
- Having a lead period contract signed with the supplier(s) to avoid supply delays
How To Calculate Lead Time?
The lead time calculator works differently for the order, process, or project because of their unique requirements. But its purpose remains to forecast inventory, avoid stockouts, and meet customer satisfaction.
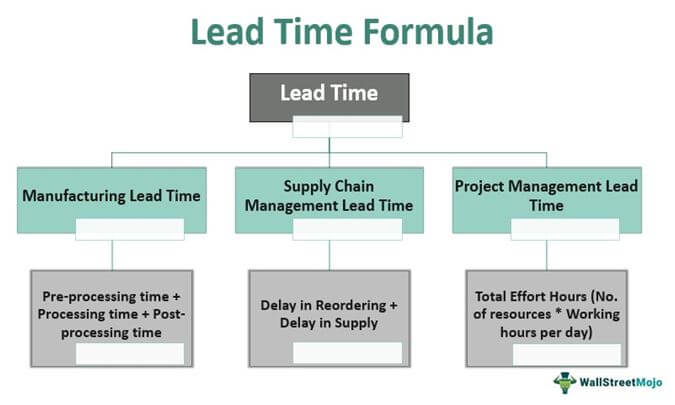
Let us take an example to understand how the lead time formula for manufacturing and supply chain management applies:
- The wholesaler A ran short of smartphones from Brand X on June 15. It places the order for the same after seven days on June 22 (delay in reordering).
- As soon as it places the order with X, the brand connects with its suppliers immediately. They promise the delivery of parts for product assembly in three days (pre-processing).
- After three days, X initiates the further operation of assembling and manufacturing the device. Order processing takes another five days.
- The company loads the finished products and ships them to wholesaler A. The delivery takes two more days (post-processing).
So, MLT for X = Pre-processing time + Processing time + Post-processing time
= (3+5+2) days = 10 days
Similarly, SCMLT = Delay in Reordering + Delay in Supply
= (7+10) days = 17 days
Lead Time vs Cycle Time
Let us say Maria orders 50 electric gas stoves of a brand for her wholesale shop. As soon as the order is received, the lead period counting begins.
- In the pre-processing stage, the manufacturer orders the needed parts from its suppliers.
- Once those parts are received, the processing stage starts, where the manufacturing unit assembles parts to design and develop electric gas stoves as per the order.
- In the next phase, post-processing occurs. The ordered electric gas stoves are loaded and shipped.
- Finally, the unloading of the product and delivery occurs.
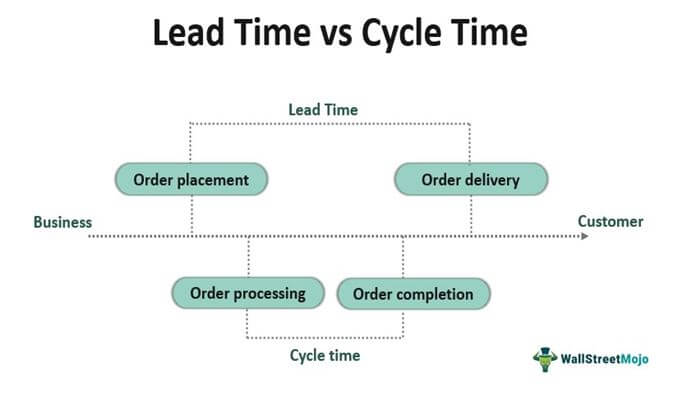
The time taken from the order placement to the delivery of products to Maria becomes the lead period. On the other hand, cycle time is the time taken for handling products at different production stages separately, i.e., the number of hours or days products remained in the pre-processing stage, processing stage, and post-processing stage individually. In short, the cycle time includes the time taken between order processing and order completion.
Frequently Asked Questions (FAQs)
Lead period or time is the amount of time taken to accomplish an order, process, or project from the time the customer places, requests, or assigns it. In short, it is the period between the initiation and completion of a task.
The lead time formula differs with the sector or industry it is used in:
a) MLT = Pre-processing time + Processing time + Post-processing time
b) SCMLT = Delay in Reordering + Delay in Supply
c) PMLT =
Calculating and reducing the lead period helps businesses enhance their operational efficiency and ensure consumer satisfaction by making products available to them. It also lets brands predict sales, maintain their market presence, boost revenues, forecast inventory, and avoid stockouts.
Recommended Articles
This has been a guide to Lead time for delivery and its meaning. Here we discuss how it works along with the formula and calculator. We also discuss how to reduce lead time. You can learn more from the following articles -