Table Of Contents
What Is Kaizen Costing?
Kaizen costing refers to a method for controlling the cost incurred over unproductive business activities and resources that do not add value to the business. It aims to reduce costs below the standard level without negatively impacting staff, quality, safety, etc.
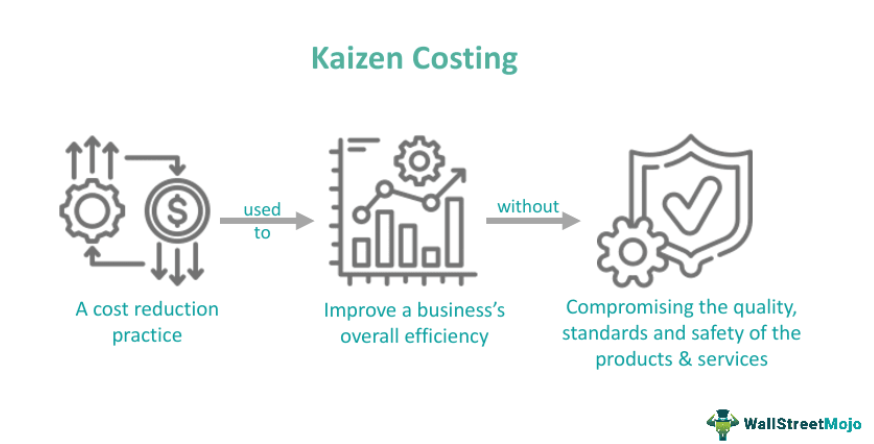
This method is based on the principles of ‘kaizen’, a Japanese philosophy; it emphasizes employees’ involvement and continuous improvement. This practice typically involves minimizing costs and eliminating the inefficiencies of an organization’s production process via several small, incremental alterations instead of extensive, disruptive changes. There are two types of kaizen costing — product-specific and asset-specific.
Table of contents
- Kaizen costing meaning refers to a process of continuous cost minimization that a business carries out to improve the production process without affecting product quality. This practice positively impacts a company’s overall efficiency.
- Asset-specific and product-specific are the two types of kaizen costing.
- There are various advantages of kaizen costing. For example, the technique is flexible and promotes communication among a company’s employees. Moreover, helps strengthen an organization’s bottom line.
- Kaizen costing is a continuous improvement method. On the other hand, organizations utilize standard costing once a year.
Kaizen Costing Process Explained
Kaizen costing meaning refers to a process companies use to continuously minimize production costs and improve the overall business efficiency by eliminating the activities that do not add any value. Organizations use this method when production starts after the complete product design stage.
This technique aims to remove losses and waste in a business’s production, distribution, and assembly processes by using this method. Additionally, they use this practice to eliminate the unnecessary steps involved in these processes and execute economic redesigns for their offerings. Hence, the technique helps organizations minimize extra costs at every stage.
Let us look at some of the costs businesses can control using this practice.
- Supply Chain Costs: These refer to costs associated with transportation, inventory, administration, and procurement.
- Production Costs: Production costs include the costs related to machinery, equipment, labor, tools, and raw materials.
- Human Resource (HR) Costs: This technique can regulate the incurred cost to hire, train, develop, and retain skilled workers.
- Other Costs: Businesses can also use the cost reduction technique to manage the cost of acquiring licenses, patents, trademarks, and expenses associated with other legal formalities.
5s Principles
The kaizen costing concept is based on five principles. These principles lay the foundation for utilizing the latest lean production processes and tools.
#1 - S1: Sort
According to this principle, companies must categorize every item based on necessity. They should label all unnecessary items red and sell them. Alternatively, organizations can dump such items. This approach can increase a business’s productivity by eliminating the unrequired clutter. Moreover, it opens up space that companies can utilize for other things.
#2 - S2: Straighten
Once organizations remove all unnecessary items, they are left with the crucial items, which they must organize well to simplify operations. In addition, this improves the accessibility, visibility, and availability of all the items and tools.
#3 - S3: Shine
Shine refers to thoroughly inspecting and cleaning equipment, tools, and other items. It establishes a positive work environment that empowers and engages operators by giving them more agency and responsibility. Moreover, it helps them spot emerging problems like material spills, fluid leaks, etc.
#4 - S4: Standardize
This principle is a bridge between the above principles. It states that businesses must establish standards for useability, cleanliness, and maintaining the placement of items in their daily operations. In addition, this principle makes the 5S methodology a reproducible series of activities instead of a one-time project.
#5 - S5: Sustain
This requires organizations to inform the employees regarding the changes made. This develops a sense of discipline and self-control among them to adhere to the set standards.
Types
The two types of kaizen costing are as follows:
- Product-Specific: The product-specific technique emphasizes enhancing the productivity and efficiency of a company’s production process for a particular product line or product. This approach involves examining the complete production process for a product, spotting the areas of inefficiency and waste, and then executing the alterations to enhance the process.
- Asset-Specific: This cost management technique focuses on enhancing the productivity and efficiency of certain equipment or assets involved in production. The approach involves spotting the assets that are increasing production costs or causing inefficiencies. Then, it involves executing changes to enhance their performance.
Examples
Let us look at a few kaizens costing examples to understand the concept better.
Example #1
Suppose a company named Amacon engages in manufacturing a particular product. It realizes that the product’s high scrap is behind the high costs. So Amacon’s kaizen team conducts a detailed analysis of the manufacturing process and finds out that the inadequate training for workers responsible for assembling the product is the main cause of the high scrap rate.
The kaizen team executes the following changes to address the issue:
- A regular assessment of the product’s cost and scrap rate
- Keeping a suggestion box for the workers to give feedback regarding the assembly process
- Executing a ‘stop the line’ strategy that allows the workers to halt the assembly process when they spot an issue without hesitation
- Providing additional training to workers on how they can assemble the product properly
- Executing a visual management system that can help workers to spot and rectify errors during assembly
The product’s scrap rate drops significantly owing to these changes, leading to cost savings for Amacon.
Example #2
In March 2019, the Andhra Chamber of Commerce held a workshop to elucidate the government benefit and schemes available to the MSME or micro, small, and medium enterprises sector. During this workshop, cost and management accountants explained strategies that MSMEs could utilize to maximize profits by improving the business and minimizing costs without negatively impacting product quality.
P. Raju Iyer, an eminent cost and management accountant, said that new strategic cost management techniques like kaizen and strategic costing play a crucial role in various MSMEs’ growth. Businesses can manage costs efficiently by making simple alterations in production planning, for example, waste reduction and effective space utilization.
Advantages & Disadvantages
Let us look at some benefits and limitations of kaizen costing:
Advantages
- Kaizen costing involves continuously seeking ways to minimize costs and increase efficiency.
- This practice helps improve product quality and increase productivity.
- It is a flexible technique that businesses can apply to any production process, whether a service, administrative, or manufacturing process.
- This method promotes a continuous improvement culture that helps organizations become more sustainable and efficient over the long term.
- It promotes critical thinking and problem-solving. This encourages teams to spot and rectify issues in a systematic and structured way.
- The practice encourages better communication among a company’s employees.
- It focuses on customer satisfaction.
Disadvantages
- This technique requires extensive analysis and data, which makes it challenging for organizations to execute.
- It mainly focuses on short-term enhancements. As a result, organizations may fail to address long-term strategic problems.
- This method is primarily applicable in production and manufacturing environments; it may be ineffective in other businesses.
- While this technique can help minimize costs, the savings can be limited.
- It may fail to address the broader organizational issues.
- Applying this technique is time-consuming. Moreover, it requires extensive resources.
Kaizen Costing vs Target Costing vs Standard Costing
Individuals new to cost management often do not have a clear idea regarding kaizen, target, and standard costing. This often leads to confusion, which one must avoid at all costs. To eliminate any confusion, individuals must know the distinct features of these concepts. So, let us look at them.
Kaizen Costing | Target Costing | Standard Costing |
---|---|---|
It focuses on continuous improvement. | Unlike standard costing, target costing is a continuous approach. It involves setting a target cost that is lower than the production cost. | Standard costing is a yearly approach. Companies set cost standards at the beginning of a financial year. |
It helps a business reduce costs and increase overall efficiency. | This approach aims to acquire a product at the lowest possible cost. | It helps in estimating a product’s cost in the future. |
Frequently Asked Questions (FAQs)
It is a technique that focuses on eliminating waste to increase productivity and minimize costs through the total involvement of every employee in an organization. Since the construction space has a lot of waste, there’s ample scope for improvement. Some of the wastes spotted in construction are inefficient workflow, safety losses, rework and change orders.
The term ‘kaizen’ is Japanese. It means continuous improvement or change for the better. The term kaizen costing refers to a continuous improvement technique businesses use to positively impact business efficiency without affecting the quality of products.
A Japanese organizational management consultant and organizational theorist named Massaki Imai introduced the concept of ‘Kaizen’ after World War II. He was influenced by TPS or Toyota Product System, an integrated socio-technical methodology that comprises the company’s management practices and philosophy.
The concept is based on the belief that nothing can be perfect. Hence, it is always possible for an organization to minimize and improve the variable costs involved in the production process.
Recommended Article
This article has been a guide to what is Kaizen Costing. We explain its types, examples, 5s principles, advantages, disadvantages, & comparison with target costing. You may also find some useful articles here -