Table Of Contents
Just-In-Time Meaning
Just-in-time, or JIT, refers to an inventory management system where production happens in small batches as per the demand. The primary purpose of installing this system is to upgrade efficiency, control production, and reduce wastage arising during production.
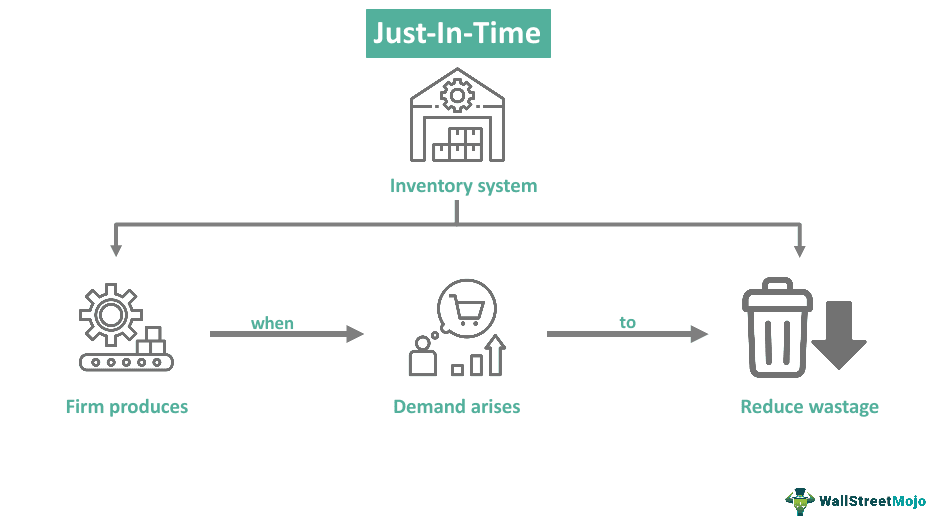
The just-in-time concept helps businesses produce the correct quantity and volume of goods. As a result, the market demand is met accurately. Plus, it serves as an essential metric to avoid excessive production. Also, there are no holding costs involved. However, a sudden rise in demand can disrupt the manufacturing process.
Key Takeaways
- Just-in-time, also JIT, is an inventory control system where the firm or manufacturing unit decides to produce goods according to the market demand.
- Its aim is to increase the efficiency of its existing products along with minimum wastage. It allows faster delivery of goods without any holding costs.
- The history of just-in-time (JIT) can be traced back to the late 20th century, particularly in the 1970s when the concept originated in Japan. Toyota was the first automobile unit to implement this model.
- The only difference between lean manufacturing and JIT is that the former operates on the organization level and later on the inventory level.
Just-In-Time Explained
The just-in-time concept is widely employed in manufacturing and production units. It involves production scheduling according to demand without rushing the process. As a result, firms can minimize wastage and reduce warehouse costs by producing only necessary goods in response to demand, automatically reducing the holding cost in a just-in-time method.
The origin and history of just-in-time inventory management can be traced back to the late 1900s in Japan. After the post-war crisis, the nation faced a massive shortage of oil. Also, there was a depletion of natural resources. As a result, Japanese industrial engineer "Taichii Ohno" invented this inventory system in the 1970s, wherein raw materials would be appropriately utilized and less wasted.
Later, Taichii implemented this system in Toyota Motors. From 1970 to the 1990s, Japan saw a considerable surge in auto exports. Before this model reached the United States, Henry Ford advocated a similar inventory system. However, Toyota cars had already captured the U.S. market. Thus "Taiichi Ohno" is regarded as the father of Just-in-time.
However, the central theme behind just-in-time inventory management is to always keep goods in the warehouses, maintaining low inventory levels that do not cause any wastage. Firms try to bridge the gap between suppliers, production levels, and demand. So, as the former estimates a particular demand, they will contact the suppliers for raw materials and other parts. As a result, they start producing goods without any storage costs. Thus, the firm's efficiency will increase, leading to no unwanted inventory.
Factors
Two crucial factors or elements of the JIT are continuous improvement and the best utilization of inventory. Businesses intend to stay focused on the quality of their products. Therefore, they refrain from engaging in mass production to avoid product degradation. Besides, firms use just-in-time methods to reduce activities that do not serve any value. Also, they aim to decrease the wastage of resources to attain maximum efficiency.
However, they are more dependent on the supply chain. For example, in the automobile sector, car manufacturers use the JIT system only to produce when they reach components from the suppliers.
Examples
To better understand the concept of the just-in-time system, let us consider some examples.
Example #1
In 2021, the demand for cars was 2000 units. Based on this demand, Steffen estimated a demand of 3000 units. The manufacturing unit then contacted the supplier for the necessary parts to produce the cars.
Once the batch of cars was completed, they were supplied directly to the dealers, eliminating the need for holding inventory in a warehouse. This approach reduced or eliminated the costs of storing and managing excess inventory. Steffen's business achieved optimum efficiency by producing and supplying only the necessary units.
The example highlights the importance of matching production with demand to avoid waste. If the firm had produced 4000 units despite the demand being 2000 units, it would have resulted in excess inventory and potential wastage.
Example #2
According to a 2023 Global Seafood Market Conference report, the just-in-time method is dead and replaced with the "just-in-case." It is because supply chain difficulties arose during the Covid-19 pandemic. Thus, to maintain inventory, the seafood companies switched to the latter.
Advantages And Disadvantages
The just-in-time model is essential for businesses seeking a quick and efficient consumer experience. First, however, it is crucial to consider the advantages and disadvantages associated with its implementation. Let's examine some of them:
Advantages | Disadvantages |
---|---|
Reduces wastage as inventory levels are low. | It is difficult to forecast future demand and start production. |
Increases efficiency since the focus of the firm is on quality. | Hurdles arise when there is a sudden rise in market demand. |
Optimum utilization resources as production takes place only when the demand arises. | During times of global crises, it becomes imperative to establish enhanced control over the supply chain. |
Firms incur no holding costs as the inventory is supplied immediately. | A strong supply chain and coordination team is required. |
Improves customer service as firms provide a faster and speeder delivery of goods. | Difficult to match the customer's expectations. |
Production errors are easily noticeable in smaller batches. | Need for multiple or flexible suppliers. |
The inventory turnover is also high. | |
The production process occurs smoothly. |
Just-In-Time vs Just-In-Case vs Just-In-Sequence
While JIT, JIC, and JIS all have significant importance in manufacturing, they differ in terms of their inventory approaches. Therefore, let's explore the distinctions between these inventory management strategies:
Basis | Just-In-Time | Just-In-Case | Just-In-Sequence |
---|---|---|---|
Meaning | JIT refers to the inventory control system where firms manufacture goods when demand arises. | As the name suggests, just-in-case is an inventory control that keeps safety stock levels in case of sudden demand. | Just-in-sequence works in collaboration with JIT and ensures inventory moves in proper sequence. |
Purpose | To increase efficiency and reduce wastage. | To produce enough goods to meet uncertain market demand. | Ensure inventory arrives timely and is in the correct order. |
Emergency inventory | No | Yes | Yes |
Need for sequence | Not necessary | Yes | Highly recommended |
Effect of demand | Increased demand can disrupt a firm's operations. | Here, firms are already prepared for such a situation. | A sudden demand can affect inventory levels. |
Also known as | JIT | JIC | JIS |
Just-In-Time vs Lean Manufacturing
Although JIT and lean manufacturing have similar characteristics, they have equal differences too. So, let us look at them:
Basis | Just-In-Time | Lean Manufacturing |
---|---|---|
Meaning | JIT refers to the inventory system for producing only those in-demand units. | Lean manufacturing is a structure where firms install a systematic method that reduces wastage. |
Objective | To increase efficiency and minimize wastage. | To eliminate errors during the process without affecting productivity. |
Area of practice | Inventory management | Management and operations |
Focus | Producing goods according to the market demand. | They are producing products with fewer resources. |