Table Of Contents
What Is Joint Cost?
Joint cost refers to the price incurred by manufacturers that goes into producing more than one product or process. These costs include labor, material, and overhead costs towards the production of the joint product. Almost every manufacturer performs a joint cost allocation to ensure the input costs are regulated.
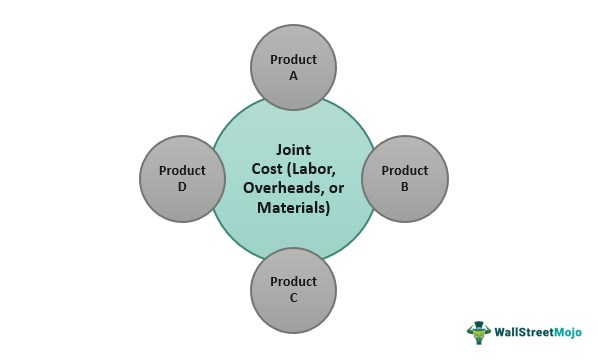
Using everyday materials for different products, the manufacturers can determine their final product much later. This stage of production is called the split-off point. The raw material or the processes used for multiple products in the manufacturer’s portfolio act as cost and time-saving agents. Cost accountants track back expenses to a particular product or process.
Table of contents
- Joint cost is the expense incurred by a manufacturer towards producing two or more products or processes. These products are similar and are usually interdependent.
- These joint products can only be differentiated once they take an individual shape at a certain point in production. This part is called the split-off point.
- Joint costs are calculated until the split-off point, where common expenses towards their production bind their expenses.
- Manufacturers need to calculate these costs to derive an optimum selling price, inventory management, and profitability of individual products.
Joint Cost Explained
Joint costs are expenses incurred toward the production of more than one product. These costs take time to be tracked back to one product or part of the process. Therefore, a cost accountant is bestowed with the responsibility of adjudging the back-tracking of production costs.
Calculating individual costs of products can be challenging in a manufacturing unit as more than one raw material or process is involved in multiple products since the costs of labor, processing, and raw materials are considered collective costs.
A joint cost function is applied to ensure each product's reasonable cost. Moreover, fixing an ideal selling point for each product is vital irrespective of combined costs.
When multiple products are produced under the same roof and using similar raw materials for numerous products, calculating the costs commonly incurred becomes crucial to derive each product's profitability.
Since there are different methods available for calculation, based on the nature of the business, resources, and type of products, companies can choose a method of calculating joint cost allocation. The different forms of calculation include:
- Survey method
- Average unit cost method
- Standard cost method
- Reverse cost method
- Sales value method
- Physical units method
- Contribution margin method
Formula
Let us discuss the formula to calculate the cost of production through the joint cost method through the average unit cost method.
Under this method, the total cost of all products jointly produced is divided by the total units manufactured. Therefore, the formula is:
Joint Cost = C/U
Where,
- C = Total cost of joint products
- U = Total units produced.
Another method to calculate the joint cost function is the survey method. Under this method, other factors such as material quality, marketing, and selling price are also considered. In totality, both qualitative and quantitative measures are considered before deriving the following formula:
Joint cost = Total Cost/ Total weighted units.
Calculation Example
Let us understand the application of the formula through the calculation below:
A Petroleum extradition company, Globe Oil Ltd., is one of the market leaders in petrol, diesel, and crude oil domains. Since their base product, through which all other by-products are extradited, they wanted to find the cost of production of each of their products.
They chose the average unit cost method for its simplicity.
From 100 gallons of petroleum, they produced 38 gallons of petrol, 35 gallons of diesel, and 27 gallons of crude oil, totaling 100 gallons.
The average cost of each unit was $200.
The following table represents the values -
Products | Units | Average Cost ($) | Apportioned Cost (Units x Average Cost) |
---|---|---|---|
Petrol | 38 | 200 | 7,600 |
Diesel | 35 | 200 | 7,000 |
Crude Oil | 27 | 200 | 5,400 |
Total | 100 | 20,000 |
Applying the average unit cost formula, we get:
Joint Cost = C/U
- = 20,000 / 100
- = $200/ unit.
Common Cost vs Joint Cost
Although joint and common cost is terms used interchangeably, they have differences in their fundamentals, application, and significance. Let us understand their differences through the points below:
Joint Cost
- Joint cost refers to the situation where the factors of production lead to two or more products due to their similar nature.
- These common factors could be labor, overhead costs, raw material, or a combination of all three.
- The products with common factors can only be identified as different at a certain point in production. Therefore, after a particular stage, when they start taking shape, it is referred to as a split-off point.
- Joint costs are the expenses incurred up to the split-off point. In situations like these, one product is more important than the others. Thereby, the products with lesser importance are called by-products.
- The products produced are similar, and the production of one product facilitates the out of the other products in the production mix.
Common Cost
- Common costs are expenses allocated toward more than one job, product, or territory. Therefore, they are challenging to identify.
- According to the National Association of Accountants, common costs are those expenses that, despite being allocated or apportioned towards producing more than one product, their outputs cannot be justified in quantitative terms.
- The characteristic that separates common costs from similar costs is that there is no established relationship between the cost incurrence and the objectives gained from using the facilities.
- Common costs apply to products and may be common for functions, responsibilities, processes, territories, or periods.
The apportionment of these costs is not bound by manufacturing or using raw materials. Instead, they can be allocated to different factors such as jobs, departments, or products.
Frequently Asked Questions (FAQs)
The cost of a missed opportunity led by choosing a particular process or investment is referred to as opportunity cost. On the other hand, joint cost refers to the shared resources used to produce or purchase more than one product.
Both these concepts are similar but have differences. Such as the fundamental difference in joint cost is an expense incurred in the production of two or more products or processes. On the other hand, common payments are more challenging to identify and accounting. The challenge arises because these costs include expenses that cannot be attributed to one department or product.
A joint cost is incurred by almost every manufacturer, as it brings down the average cost of production by involving common resources and allows having multiple products through a similar process or materials.
Recommended Articles
This has been a guide to what is Joint Cost. Here, we explain it with an example, formula, how to calculate it, and compare it with common cost. You can learn more about financing from the following articles –