Table Of Contents
What Is An ISO 9000?
ISO 9000 is a series of international standards concerning quality management and assurance developed to help organizations establish and maintain an effective quality management system (QMS). The standards can help business entities fulfill regulatory requirements, improve continuously, and ensure customer satisfaction.
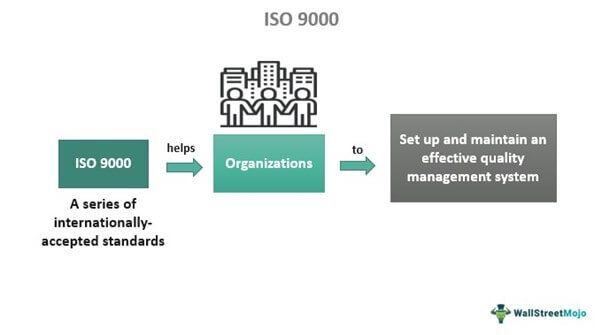
ISO 9000 series lays out the principles, best practices, and guidelines for quality management systems. It leads to improved documentation of organizational processes, making the production process more efficient, reducing wastage, and minimizing costs. The standards are not specific to any particular industry and can apply to companies irrespective of their size.
Key Takeaways
- ISO 9000 meaning refers to a series of international standards describing the best quality management practices. It helps to fulfill the requirements of customers and shareholders while meeting regulatory needs.
- The series has seven principles. Leadership, relationship management, engagement, and customer focus are some of them.
- Companies must clear a third-party audit to procure an ISO certificate. Also, they must renew the certificate after the end of every three years.
- ISO 9000 benefits include reduction in manual work, improvement of brand image, minimization of errors in recurring processes, etc.
ISO 9000 Certification Explained
ISO 9000 meaning refers to a set of globally-accepted standards introduced by the International Organization for Standardization (ISO) to help organizations establish, maintain and continuously improve their QMSs. An ISO certification enables businesses to provide their customers with the best products and services. Therefore, one should consider it the base level of any quality system.
ISO published these standards for both profit and non-profit organizations. The series covers the fundamentals and vocabulary of an ideal QMS. Moreover, it describes the seven quality management requirements or principles.
A business can get ISO certification only after a third party carries out a successful audit. All organizations must fulfill the following requirements to clear the audit and obtain this certificate:
- Companies must develop and implement a QMS that aligns with the principles of the relevant series of standards.
- Organizations must get an audit performed by a certified body to evaluate their QMS’s performance against the set standard.
Once businesses obtain the certificate, they have to recertify it every three years to ensure that they are up to date with the latest standards.
ISO 9000 Standards
The series comprises the following standards:
- ISO 9000:2015: This standard defines the specifics of QMSs while clearly stating the terms utilized in such standards.
- ISO 19011:2018: It offers guidance regarding internal audits, which confirm and increase the efficacy of a QMS and external audits.
- ISO 9004:2018: This standard offers guidance for continuous success per the seven quality management principles or requirements. It specifies the principles that the senior members of the company’s management team must utilize to boost performance while considering shareholders’ requirements.
- ISO 9004:2018: It offers companies guidance on fulfilling the relevant regulatory and quality requirements while increasing shareholders’ satisfaction. Moreover, it offers guidance to organizations on how to have an effective technique for spotting and implementing improvements.
ISO 9000 Requirements
Let us look at the ISO 9000 series requirements.
1. Customer Focus
Organizations must understand the requirements of existing and future customers and aim to exceed their expectations. They can ask for feedback from customers and monitor complaints.
2. Engagement
Everyone at every level of an organization should improve the business’s capability to create customer value.
3. Leadership
A company’s leaders should establish a unity of direction throughout the organization to equip and empower the employees to achieve quality-related objectives.
4. Process
Organizations must manage their activities as interrelated processes that work as a well-organized system. Moreover, they must utilize process analysis tools to measure their capability and spot relations between activities to improve the processes.
5. Evidence-based Decision Making
Companies must make all decisions after thoroughly analyzing and evaluating the necessary data and information for the best results. One must remember to balance data analysis with qualitative evidence and practical experience.
6. Relationship Management
For short-term and long-term success, business entities must manage their relationships with related parties, such as vendors, partners, and contractors.
7. Continuous Improvement
Organizations must adopt an approach that focuses on continuous improvement; they should empower workers to make improvements and celebrate the same. Moreover, they must measure the improvements consistently.
Example
In May 2022, a popular EV technology company, Cenntro Electric Group Limited, announced that it would take over a new production facility in Changxing for roughly $19.5 million. This new acquisition will significantly improve the company’s production capacity. Moreover, it will help Cenntro obtain ISO 9000 certification enabling the company to establish and maintain an effective QMS. This, in turn, can improve business efficiency and ensure customer satisfaction.
Trial production will begin from Q3, 2022, per expectations.
Benefits
ISO 9000 benefits businesses, their employees, and customers. Let us look at the advantages.
- A business becomes well-equipped to address feedback efficiently and quickly. Resultantly, customer satisfaction increases.
- ISO certification serves as a badge of reliability and improves brand image. It helps in gaining customer trust.
- The series of standards encourages preventive thinking, which enables businesses to address issues before they arise and impact customers.
- It minimizes the errors in recurring processes.
- The standards help businesses save time through the efficient management of resources.
- The cumulative effects of implementing these standards can result in increased market share and profit potential.
- The set standards reduce manual work through process automation and process integration.
- Job security increases as these standards improve business performance.
- Employees have a clear idea regarding their roles and responsibilities. This improves job satisfaction.
- Employees feel more responsible for their jobs owing to accountability and process ownership. As a result, process quality improves.