Table Of Contents
What Is Inventory Management?
Inventory management in business refers to managing order processing, manufacturing, storage, and selling raw materials and finished goods. It ensures the right type of goods reach the right place in the right quantity at the right time and at the right price. Thus, it maintains the product availability at warehouses, retailers, and distributors.
An effective inventory management system is an integral part of supply chain management (SCM). It plays a crucial role in overseeing purchases of production components from suppliers and fulfilling customer orders. Businesses use this strategy to meet consumer demands and grow sales effectively. It also helps them track the movement of products from manufacturing units to warehouses and then to points of sale.
Table of contents
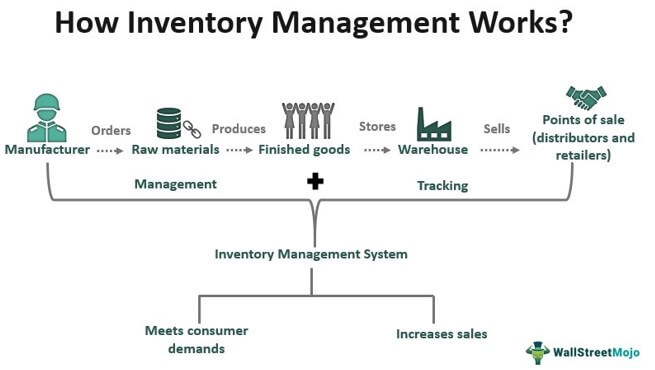
- Inventory management means a business strategy, which deals with managing order processing, manufacturing, storing, and selling raw materials and finished goods.
- It ensures product availability at warehouses, retailers, and distributors. Businesses of all sizes, including manufacturing, retail, e-commerce, restaurant, FMCG, logistics, etc., use it to meet consumer demands and grow sales.
- Small businesses manually track inventory using electronic spreadsheets. Large manufacturers use advanced software as a service (SaaS) or enterprise resource planning (ERP) software to manage stocks.
- The most effective stock management techniques include regular stock review, just-in-time, and ABC analysis.
How Does Inventory Management Work?
Inventory management is essential for any business concerned with the manufacturing and selling of products and services. Inventory is the core of a manufacturing company, a retail store, an e-commerce business, a restaurant, an FMCG firm, or a freight/logistics company.
While a shortage of inventory might be problematic, having too much can lead to damage and waste due to demand fluctuations. But if done correctly, it ensures a smooth flow of goods, from acquiring raw materials to selling finished goods.
Other inventory management objectives include addressing complex business decisions, such as reordering, restocking, pricing, and distributing products in response to market demand. All this is made possible by tracking inventory (inputs/ingredients and outputs/products) at every level, including warehousing and distribution. Eventually, it reduces the risks of scarcity or excess inventory at any given point in time. Furthermore, the timely availability of products reflects in customer satisfaction and increased sales.
Steps In Inventory Management
- A business must track the inventory in the market and warehouse regularly to balance demand and supply chain. Thus, it knows which items need to be available immediately so that customers do not have to wait.
- Based on supply and consumption, the business gets orders from different points of sale. It then manufactures finished goods and transports them to markets.
- Availability of stocks in the market is a significant aspect of supply chain management. Making them available at the right time, i.e., before the stockout, is even more critical.
- Until goods reach points of sale, the business tracks their movement at each step in the inventory and supply chain management processes. It does so using lot numbers, quantity and cost of goods, and delivery dates.
- Small businesses can manually track inventory using electronic spreadsheets. Companies producing large volumes of goods use advanced software as a service (SaaS) and enterprise resource planning (ERP) software.
Techniques Of Inventory Management
Inventory management is effective only when techniques applied are efficient and up to the mark. There are various strategies that a business can choose from, depending on its size, type, and product offering. Here are three techniques that can help small and big companies ready their inventory for supply.
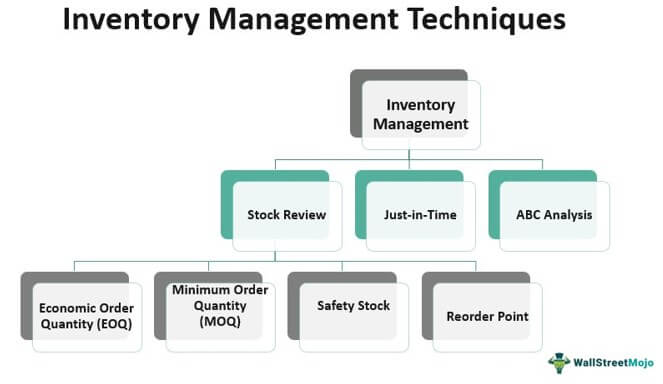
#1 - Stock Review
It is the most effective technique that involves reviewing stock availability. Small businesses with limited production can manually track available stocks. But large companies utilize advanced inventory management software like SaaS and ERP to monitor supply and consumption regularly.
This strategy also ensures the placement of reorders before existing stockpiles get exhausted. It helps identify the following order processing stages and arrange stocks accordingly:
Economic Order Quantity or EOQ
It refers to the minimum volume of stocks to reorder to meet the market demand before the existing supply depletes. Knowing this reduces costs of inventory holding and ordering due to excess production. The formula used to estimate EOQ is as follows:
Economic order quantity (EOQ) = √
Where,
- D = Demand per year
- K = Ordering cost per purchase
- H = Holding costs per year, per unit
Minimum Order Quantity or MOQ
It is the minimum volume of stocks that a supplier wishes to sell to a producer. The only aim of the supplier here is to earn more profits while getting rid of the inventory more quickly.
Safety Stock
Safety Stock is the stockpile of inventory that a manufacturer retains in excess to ensure they are available to customers when demand spikes unexpectedly. Besides, it protects businesses against the unforeseen shortage in supply.
Also known as a buffer or emergency stock, it lets manufacturers cover up for the lead time until the new inventory reaches points of sale. However, it never crosses the level that increases holding costs.
Safety stock = (Max Daily Sales x Max Lead Time in Days) – (Average Daily Sales x Average Lead Time in Days)
Reorder Point
Reorder Point is the level at which businesses realize to reorder new inventory from the supplier to avoid stockouts. The replenishment of stocks considers factors like existing and potential demand and lead time before new inventory arrives. The formula used by businesses to determine a minimum level of inventories is as follows:
Reorder point = (Average Daily Sales x Average Lead Time in Days) + Safety Stock
#2 - Just-in-Time
Most stock management techniques advocate the existence of sufficient inventories for an unpredictable rise in demands. But the JIT approach is more about having a zero inventory system. Under this arrangement, finished goods are made available at the right time. It, thus, helps businesses meet consumer demand without overstocking the inventory and bearing holding costs.
This strategy guarantees the delivery of raw materials to production units on time. It enables the manufacturing to begin at the scheduled time. Also, it encourages the pull system whereby order is initiated and attended only when required. In short, it acts as a real-time response to the market demand and is helpful in case of items that are likely to get obsolete.
#3- ABC Analysis
This technique helps businesses categorize inventories into three distinct groups based on their value, costs, and consumption:
- Category A comprises higher value products kept in a small amount. Hence, it cuts the warehouse space and cost requirements.
- Category B consists of items of moderate value and moderate quantity with regular sale records.
- Category C includes products that acquire smaller value but have high market demand. It makes the inventory occupy more warehouse space and requires businesses to pay more for the same.
A business can stay prepared with stocks as and when they receive orders from different points of sale based on the inventory category.
Examples
To understand inventory or stock management in a better way, let us consider the following examples:
Example #1
A soap manufacturer has already created a batch of soaps to dispatch to different points of sale. Given the high consumption of soaps, it reorders raw materials to start manufacturing the next lot.
Raw materials ordered beforehand, in this case, act as the inventory for the company. And the already delivered finished products are the inventory for retail units that will be selling soaps further.
Pre-ordering raw materials helps the company produce and supply soaps regularly to ensure the lead time does not keep customers waiting or making them switch to its competitor’s soap.
Example #2
Closure of brick-and-mortar stores due to the COVID-19 pandemic resulted in an unprecedented growth in online sales. It, thereby, put significant pressure on the supply chains of multiple brands. Furthermore, stockouts pushed firms to invest more in optimizing their product's search ranking on e-commerce platforms.
Significantly, failing to cope with increased demand for products online could lead to a drop in sales. Therefore, companies must implement an inventory management system to boost sales and avoid revenue losses and brand failure. For instance, they can consider selling products with higher sales value and a high in-stock rate.
Frequently Asked Questions (FAQs)
Inventory or stock management strategy concerns the supervision and management of raw materials and finished goods from manufacturing units to warehouses and then to their points of sale. It makes the right type of goods available at the right place in the right quantity at the right time and the right price.
Inventory management ensures inventory availability at warehouses, retailers, and distributors before stockouts. It, thus, becomes a crucial part of supply chain management. Also, it maintains the smooth flow of goods by reordering, restocking, pricing, and distributing products in response to market demand. Not only does it reduce risks of scarcity or excess inventory, but on-time delivery of products also leads to customer satisfaction and increased sales.
The most important techniques used for efficient inventory management include regular stock review, just-in-time, and ABC analysis.
Recommended Articles
This has been a guide to what is inventory management and its meaning. Here we discuss steps, techniques of inventory management, and how does it work, along with examples. You can learn more from the following articles –