Table Of Contents
What Is Input Cost?
Input cost, in economics, refers to the expenses incurred in producing a product or service. It encompasses the cost of factors of production as well as raw materials. The primary purpose of this cost is to determine the total expense incurred during the production stage.
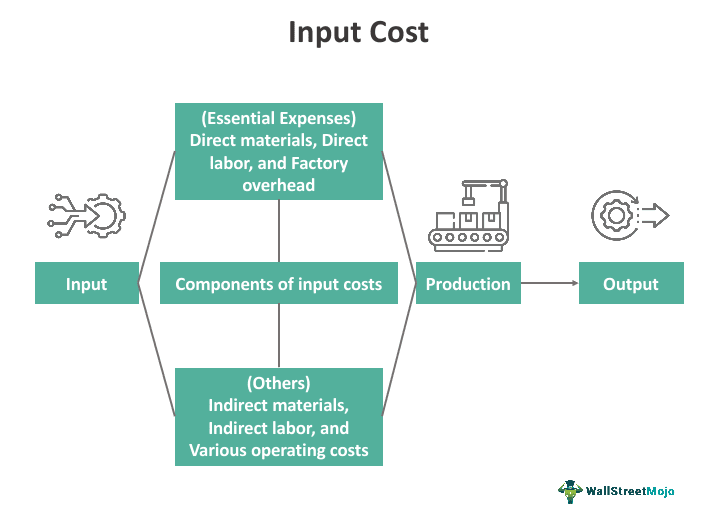
Input costs are a vital element of the manufacturing process, helping to ascertain the final cost of a product or service. Additionally, it is considered a variable cost due to fluctuations in the factors of production, thus forming a core component of input cost inflation.
Table of contents
- Input cost is a fundamental component of economics, encompassing the total expenses involved in the production process.
- It plays a crucial role in determining the output cost of the final product or service. Various factors, including macroeconomic elements like demand and supply, can impact input prices.
- It includes raw materials, wages, rent, energy, and other factors of production. The overall cost can increase with each additional unit.
- Several strategies to manage it include cutting expenses, passing downstream, absorbing costs, exploring alternatives, and other proactive measures.
Input Cost Explained
Input cost is a crucial component of micro and macroeconomics, encompassing all expenses directly related to the manufacturing process, such as raw materials, labor, technology, and factory overheads. As a firm decides to produce goods, the production cost automatically arises, later used to determine the output cost or total cost. Consequently, it plays a pivotal role in determining the prices of products and services, with any further fluctuation potentially influencing retail prices.
Various factors can influence input costs. Given their variable and direct nature, these costs can fluctuate with changes in demand and supply in the economy. Notably, raw material prices, energy costs, and wages significantly impact. Massive increases in factors of production prices contribute to inflation in later stages. Consequently, when a plant decides to manufacture a product, it may prefer large quantities or implement other methods to manage input prices, aiming to establish an equilibrium between input and output prices.
This concept is universally applicable across all sectors and industries engaged in production, including agriculture, where high input costs become input costs for other firms. Similarly, a high input cost in agriculture may lead to comparable costs for other industries.
The same principle applies to additional inputs. Firms increasing their production capacity will witness a rise in marginal input costs, which refers to the additional input increasing the overall price of the product. Even a slight increase can substantially impact overall revenues and demand.
Examples
Let us look at the examples to comprehend the concept:
Example #1
Suppose Cazey owns Chippey Chips Foods, a nachos-making factory on the outskirts of Los Angeles, and the production capacity is 50,000 units. Let us calculate the input cost using the provided data below.
Raw materials = $1,500
Wages= $400,000
Land (rent) = $100,000 per month
Electricity = $6,000 per month
Other factory overheads = $50,000
Total input cost = Raw materials + wages + rent + energy + other factory overheads
= $1,500 + $400,000 + $100,000 + $6,000 + 50,000
= $557,500 monthly cost.
Input cost per unit = Total cost / Total capacity
= $557500/ 50,000
= $11.15
Example #2
Imagine Sam is a baker making cupcakes. The flour, sugar, eggs, and other ingredients he uses to bake the cupcakes represent the input costs. The cost of these raw materials, the electricity for the oven, and wages for his time contribute to the overall cost. Understanding and managing these expenses is crucial to determining the total cost of producing each cupcake.
How To Manage?
Producers and firms can employ various strategies to manage rising costs in their plants effectively. Let's explore some of them:
- Cutting Costs: The primary approach to managing these costs is to reduce input expenses by exploring alternatives or replacing certain factors of production. For example, if a production process relies heavily on manual labor, introducing robotic machines can decrease the need for human workers, thereby reducing labor-related costs.
- Passing Rising Costs to Customers: In cases where cost inflation results in higher costs for factors of production and it proves challenging to reduce initial costs, firms may pass the burden onto customers by increasing retail prices. This adjustment helps offset the increased input prices. However, it can potentially impact consumers at the distribution level.
- Absorption of Rising Costs into Profits: Another method involves converting rising costs into profits through a process known as absorption costing. In this approach, firms use various methods to incorporate price increases into profit margins. For instance, a company might utilize waste generated from the corn input cost per acre to generate electricity or convert dairy waste (such as whey) into protein powder. This method is commonly preferred by chief financial officers (CFOs).
- Finding Cheaper Alternatives: Exploring cost-effective alternatives for raw materials is another viable strategy to reduce overall production costs. Occasionally, suppliers may charge more for materials, making it crucial to carefully evaluate the balance between quality and price before making decisions.
Input Cost vs Output Cost
Let's look at the differences between the two:
Aspects | Input Cost | Output Cost |
---|---|---|
Meaning | Refers to the cost incurred in the manufacturing process on factors of production. | Refers to the cost applied to the final product. |
Purpose | Aims to determine the total cost at the production stage. | Focuses on finding the total cost of the finished product. |
Inflation | Leads to input price inflation. | Constitutes a crucial component of output price inflation. |
Fluctuation | It may change due to various macroeconomic factors like demand and supply. | Primarily depends on input prices; any change in the latter can influence output cost. |
Place of occurrence | Occurs at the initial production stage. | Typically occurs after the entire production and distribution process is completed. |
Frequently Asked Questions (FAQs)
Optimum inputs and costs are vital for efficient operations. Businesses enhance productivity and profitability by carefully selecting the right inputs at the optimal cost. Striking the right balance ensures resource utilization, cost-effectiveness, and a competitive edge in the market.
It refers to the overall increase in the costs of raw materials, labor, and other production inputs worldwide. This phenomenon impacts industries globally, leading to rising production expenses, affecting profit margins, and potentially influencing pricing strategies to manage inflationary pressures.
It significantly impacts the supply of goods and services. When costs rise, it can lead to increased production expenses. In response, businesses might adjust their supply chains, production levels, or pricing. Fluctuations in costs can disrupt the delicate balance of supply and demand, influencing market dynamics and affecting consumers through changes in product availability and pricing.
Recommended Articles
This article has been a guide to what is Input Cost. Here, we explain its examples, how to manage it, and comparison with output cost. You may also take a look at the useful articles below –