Table Of Contents
What is Holding Cost?
Holding cost, also known as the carrying cost of inventory, refers to the cost that an entity incurs for handling and storing its unsold inventory during the accounting period (monthly, quarterly, annual) and is calculated as the total of storage cost, finance cost, insurance, and taxes as well as obsolescence and shrinkage cost.
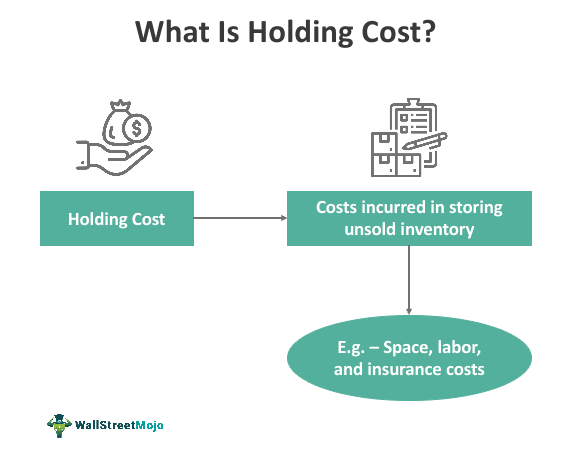
The holding cost includes the cost of any unsold item. The items that do not sell because of being damaged or spoilage also become the component of the holding cost. Having minimum holding cost is a positive thing for any business. Hence, firms try reducing this cost as one of the significant supply chain management strategies.
Holding Cost Explained
Holding cost, as the name suggests, is the cost of holding inventory that remain unsold due to any reasons, including spoilage and damage. A higher holding or carrying cost indicates more liability as the inventories not only occupy space, but also lead to waste of resources if they remain unsold for long. On the other hand, a lower value of such costs depict a better position of a business as it retains the efforts and resources utilized for the production or distribution or sale.
Holding costs are of two types – inventory storage costs and cost of capital. While the former includes costs incurred in resources and facilities required to store unsold items, the latter includes insurance costs, legal liability expenses, and interests incurred if it’s a working capital.
The cost incurred to handle and store the inventory generally ranges between 15%-40% of total inventory cost, which further includes the costs attributable to storage and material handling charges, the financing cost, the opportunity cost of holding inventories, and insurance, taxes, and obsolescence cost. Inventory holding costs may vary from business to business as it depends on many factors such as inventory holding days, buying the premises vs. financing warehouse facilities, the average cost of capital, etc.
Computing a holding cost is one of metrics for any business to assess their performance and sales figures. The businesses aim to reduce these costs as much as possible. Reducing the holding or carrying costs is a significant strategy that businesses adapt to have an efficient supply chain management. To reduce this cost, however, businesses have multiple methods to adopt. Applying these techniques help businesses minimize the cost of storing the inventory, thereby bearing the carrying cost.
Some of the ways in which the holding cost can be reduced or taken care of have been listed below:
- It is important to get rid of the dead inventory as soon as they are identified. Shifting them to the storage house and waiting for it get sold is a waste of time.
- The businesses must not overstock items. Overstocking leads to spoilage and damage, which hampers the sales figure.
- A firm must assess the demand for a product keeping in mind the present scenario. Studying market trends or following historical data for the current season does not help. Even if the past records help, it is risky. Hence, it is recommended that businesses refrain from relying on the past patterns solely, and study current demands to assess current demands.
- The businesses must ensure the lead time is less. Lead time is the time taken for the products to reach firms from the suppliers. If the lead time is low, the inventory would remain is sound condition for long, thereby assuring of a good quality when sold. Else, it may remain unsold.
Ensuring the above helps firms ensure they have a reduced holding cost as not many items remain unsold.
Components
The types of costs that make up the holding costs become its components. Let us check what are included in the list below:
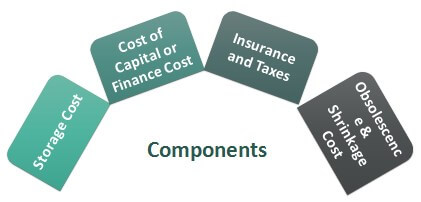
#1 - Storage Cost
It refers to the cost attributable to storing the unsold inventory. it includes:
- Warehouse rent or lease payments,
- Cost of personnel employed at the warehouse,
- Maintainance Cost,
- Material handling equipment cost,
- Depreciation
- Utility charges etc.
As per the CSCMP's 30th Annual State Logistics Report, the total storage cost of US businesses was the US $ 153.10 billion in 2018.
#2 - Cost of Capital or Finance Cost
It refers to the average cost of investments or financing the warehouse facility and include the following:
- Cost of Investments
- Working Capital Requirements
- Financing Cost: This is the cost of financing the storage premises. Often, the entities avail warehouse financing facilities to cover the cost of premises and pay interest payments to the lending institution.
- Opportunity Cost: Opportunity cost generally refers to the loss of other alternatives due to the chosen alternative. The unsold inventory represents the cash blocked which, if not invested in buying inventories, then could have generated a return at the rate of the cost of capital of the company. This implied loss is an opportunity cost for the businesses and, thus, added to the holding cost of the entity.
As per the CSCMP's 30th Annual State Logistics Report, the total finance cost of US businesses was the US $ 192.50 billion in 2018
#3 - Insurance and Taxes
It refers to the cost of insurance of inventory and premises as well as the cost of taxes.
#4 - Obsolescence & Shrinkage Cost
In the case of holding inventory, specifically technology or software inventory, there is always a chance of inventory becoming obsolete. It may not sell for an extended period due to technological advancements. Thus, Shrinkage cost is the cost incurred due to damage of inventory, or spoilage of inventory in case of perishable products, or loss incurred due to theft.
As per the CSCMP's 30th Annual State Logistics Report, the total insurance and incurs the cost of US businesses were the US $ 148.10 billion in 2018.
Formula
To know how to calculate holding cost, one can use the expression given below:
Examples
Let us consider the following instances to understand the holding cost meaning properly:
Example #1
ABC Inc is holding inventory worth US 400,000 and has a total carrying cost of 25%. Thus, the inventory holding cost for ABC Inc. will be $ 400,000 * 25% i.e. US $ 100,000.
Example #2
XYZ Inc. has taken a warehouse facility to store its inventories. The handling and storage cost is US $ 20,000, and the insurance cost is US $ 3,500. The total inventory of the entity for the years is US $ 200,000. In addition, the entity is paying interest of $ 7,500 as the cost of warehouse financing.
In this scenario, the inventory holding cost of XYZ Inc will be -
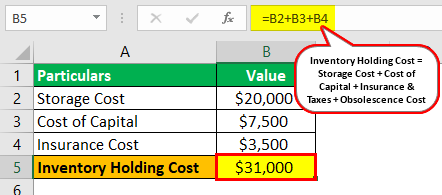
Inventory Holding Cost = Storage Cost + Cost of Capital + Insurance Cost = $ 20,000 + $ 7,500 + $ 3,500.
= $ 31,000.
Holding Cost vs Ordering Cost
Holding cost and ordering cost are two widely used terms in the context of inventory management. However, they share a couple of differences that one must know of. Let us have a look at some of them:
- Holding or carrying costs are costs incurred in storing inventory that remain unsold, while ordering costs are costs include costs of purchasing and receiving items, including logistics expenses.
- Holding and ordering costs are inversely proportional to each other. This means, if the holding cost is more, the ordering cost reduces, and vice-versa. It is because when the unsold inventory remains, the next order placed is less as the businesses try to utilize the remaining ones.
Recommended Articles
This article has been a guide to what is holding cost. Here, we explain the concept along with its formula, examples, components, and vs ordering cost. You can learn more from the following articles –