Table Of Contents
What Are Direct Costs?
Direct costs refer to the cost of operating core business activity—production costs, raw material cost, and wages paid to factory staff. Such costs can be determined by identifying the expenditure on cost objects.
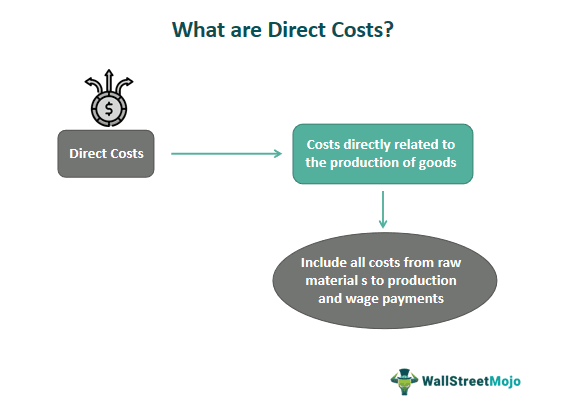
Direct costs are output costs and operational costs. They contrast with indirect costs. Indirect costs are not concerned with the production or purchase of merchandise. Indirect costs are attributed to the running and managing of a business entity.
Table of contents
- Direct cost comprises all manufacturing expenses incurred in producing final goods or services. Alternatively, it could be the procurement of goods for wholesale reselling.
- It includes various overheads like direct labor, direct material, manufacturing supplies, freight, and fuel or power consumption.
- Direct cost is used to determine the per-unit cost of production. The aggregate of direct expenses is called prime costs.
Video Explanation of Direct Costs
Direct Cost Explained
Direct cost refers to any expense that is directly associated with a company’s production facility. These expenses vary, depending on quantity, but certain fixed costs like factory rent can also be considered direct expenses.
Costs objects about direct expense are output costs and operational costs. Cost objects determine the exact product cost and selling price.
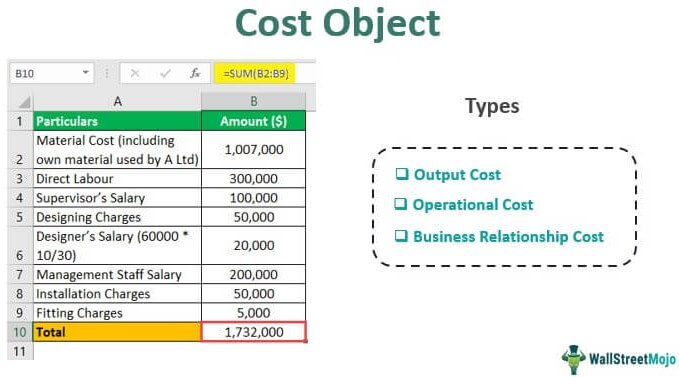
The output cost object determines the per-unit cost of production of each product or service. Overall production cost is distributed among departments, projects, and processes—operation cost objects. Thus, we can say that the company’s direct expenses can be allocated to each unit of the cost object.
Direct expense is essential for budgeting, decision making, selling price estimation, and profit evaluation. A firm’s direct expenses determine the cost of goods sold (COGS). When companies attain economies of scale, they successfully reduce COGS. Alternatively, direct expenses can be reduced by finding suppliers who provide higher discounts. Also, manufacturers try to eliminate inefficiencies in production processes.
Types
The different types of direct costs are as follows:
- Direct Labour: Wages paid to factory workers directly involved in the production of goods or services add to the direct expenses accrued by a business. Such expenses vary—increase or decrease depending on production quantity.
- Direct Material: Raw material is a variable cost. It is either used in the production process or purchased for reselling purposes.
- Manufacturing Supplies: These refer to various consumables used in a factory—even registers, pens, paper, and other stationery goods.
- Transportation: Whenever goods are moved in or out of a factory, the freight paid by the company is considered a direct expense.
- Consumption of Power, Fuel, and Utilities: The various sources of fuel and power used for running the machinery and equipment are direct expenses—diesel, gasoline, natural gas, electricity, or coal.
- Factory Rent: Factory rent is a fixed and direct expense.
Formula
In accounting, the total direct cost or prime cost is computed with the help of the following formula:

Here,

Example
Let us assume ABC Manufacturing furnishes the following cost information:
- Raw materials – Opening stock: $100,000;
- Closing stock: $70,000;
- Purchases: $225,000
- Direct labor – $120,000
- Work Overhead – $35,000
- Administration overhead – $26,000
- Selling & distribution overhead – $38,000
- Finished units – 200,000
Now, based on the given data, calculate the overall direct expense and cost of sales per unit.
Solution:
The Cost Statement of ABC Manufacturing is as follows:
Particulars | Details ($) | Amount ($) |
---|---|---|
Cost of Raw Material Consumed: | ||
Opening Stock | 100000 | |
+ Purchases | 225000 | |
(-) Raw Material | (70000) | 255000 |
+ Direct Labour | 120000 | |
Prime Cost (Total Direct Cost) | 375000 | |
+ Works Overheads | 35000 | |
Works Cost | 410000 | |
+ Administrative Overheads | 26000 | |
Cost of Production | 436000 | |
+ Selling and Distribution Overheads | 38000 | |
Total Cost of Sales | 474000 |
Cost of Sales Per Unit = Total Cost of Sales/Finished Units
Cost of Sales Per Unit = 474000/200000 = $2.37
Interpretation:
- Each component of prime costs is a direct cost. It included explicit material and direct labor—easily attributed to finished products.
- The overheads mentioned after prime costs are indirect and do not contribute to the production of goods—work overhead, administrative overhead, and distribution overhead.
Frequently Asked Questions (FAQs)
Examples are as follows:
1. Direct labor
2. Factory or warehouse rent
3. Cost of raw material
4. Cost of merchandise
5. Manufacturing supplies
6. Fuel consumption
7. Freight
Given below is a step-by-step method of computing:
1. First, Identify the cost items that facilitate the manufacturing of goods or services. Make a list of the costs.
2. Segregate direct expenses and indirect expenses from cost items. Some expenses like electricity costs cannot be divided into costs per unit of production.
3. Finally, add all the individual costs to determine the total direct cost.
The direct expense comprises manufacturing overhead on the production of goods or services. In the case of reselling, direct expense comprises expenditure made for wholesale purchases—direct labor and raw material.
On the contrary, indirect cost refers to expenses incurred for the functioning, management, and maintenance of a business. Overheads like showroom rent and manager’s salary are not considered for the computation of unit cost of goods or services.
Recommended Articles
This article has been a guide to what are Direct Costs. Here we explain the concept with examples, formulas, types, and its interpretation. You may learn more about accounting from the following articles –