Table Of Contents
What Is Deferred Maintenance?
Deferred Maintenance is a planned or unplanned delay in the repair and upkeep of real estate, infrastructure, machinery, or any other fixed asset. Since many companies operate on a shoestring budget, repairing or maintaining all their properties, machinery, and equipment in every financial year is challenging.
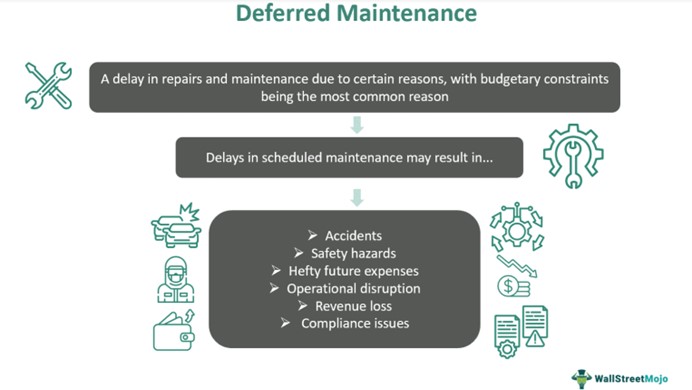
A tangible asset with a long useful life is prone to wear and tear with regular usage. If its overhauling is postponed for a long time, it may cause machinery breakdown, property damage, or destruction. This, in turn, might lead to a hefty capital expenditure or high future cost to the company.
Table of contents
- Deferred maintenance or deferred corrective maintenance is the delaying or postponement of the repair and overhauling of tangible assets like machinery, plant, building, or other property.
- The purpose of a deferred maintenance plan is to save money or avoid unproductive costs.
- It is a result of inadequate funds, non-visibility of a problem area, repair tasks being listed as low-priority, management hesitation to halt production, or a lack of resources like skilled labor, time, parts, or material.
- Delayed maintenance may cause property damage, machinery breakdown, low productivity, high replacement costs, and personal injuries, posing multiple safety risks on the premises of an office, factory, or other buildings.
Deferred Maintenance Explained
Deferred maintenance is the backlog of asset repair and overhauling activities over a significantly long period. In an organization, the maintenance of assets is often underrated. Hence, management does not want to spend on these activities unless necessary.
Due to a lethargic approach towards maintenance, repairs, and overhauling, senior executives responsible for these tasks cite multiple reasons for not undertaking them. A low budget, limited resources (i.e., labor, material, or parts), a lack of skills, management’s unwillingness to allow production breaks, etc., are reasons for maintenance shortfalls.
An overall lack of awareness about operational processes and financial concepts may result in executives being unable to identify the role repairs and maintenance play in ensuring process productivity and cost-effectiveness. Also, if a company follows a reactive strategy, it will not prioritize maintenance.
Though postponing such activities may give companies temporary financial and operational relief, the consequences of such negligence or mismanagement can be tricky. They may lead to personal injuries, property damage, machinery breakdown, significant and immediate replacement costs, low productivity, considerable cost of repairs in the future, and shrinkage of the asset's useful life.
It is essential to understand that spending money on the maintenance of assets is not an expense but an investment. Hence, achieving organizational goals is nearly impossible without efficient and productive assets. Therefore, reducing maintenance backlogs is crucial for the firm's growth. For this purpose, a manager should:
- Prioritize the repair and maintenance of various assets as critical, less critical, and non-critical.
- Use asset management software and a Computerized Maintenance Management System (CMMS) to document asset condition and upkeep status.
- Conduct regular audits, i.e., every week, month, quarter, or year, to gauge the condition of assets.
- Perform more preventive maintenance tasks to avoid deferred and emergency maintenance situations.
- Keep aside a portion of the profit for the overhauling of assets.
Here is a diagrammatic representation of how such maintenance decisions are made.
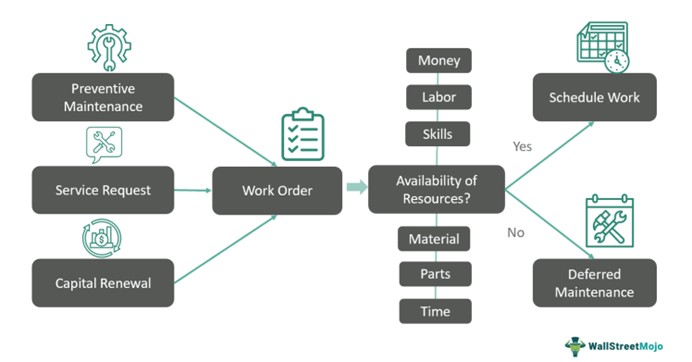
Such delays may also result in compliance issues, particularly in the healthcare, civil, construction, infrastructure, and many other sectors. Companies may also suffer heavy revenue losses on account of operational disruptions in the case of breakdowns. Additionally, reputational damage is a possibility in case of serious accidents or loss of human life. In such cases, companies might have to deal with legal complications.
Examples
Various instances of companies failing to fix issues related to office buildings, parking lots, machinery, equipment, plants, and other fixed assets can be found across different industries. Let us study some examples to understand this point.
Example #1
Suppose BuildStrong & Co. is a real estate company with multiple regional offices in the US. It faces a shortage of funds due to multiple high-value, ongoing projects. Therefore, management postponed the following maintenance tasks on the premises of its various regional offices:
- Painting the walls of Office A to address peeling paint and stains
- Waterproofing the terrace and walls of Office D
- Repairing the window glasses of Office F
- Leveling the parking area of Office H
Now, this kind of deferred maintenance in real estate can be a real problem that requires deferred maintenance appraisal. The effects of ignoring or postponing maintenance can quickly snowball into major issues that can be difficult to tackle. The following is possible in BuildStrong’s case:
- If painting is not finalized on time, mold formation is possible, along with moisture creation behind the walls, which could lead to electrical hazards.
- Water damage within the building is a real danger if the leaks from the terrace remain unaddressed.
- Damaged window glasses are a safety threat. Also, air conditioning becomes ineffective due to the outside air that enters rooms through cracked glass. This results in increased energy consumption.
- Uneven surfaces across a parking lot are a safety hazard, too.
One can see from the example above that ignoring or indefinitely rescheduling maintenance activities can be quite hazardous for a company and its people.
Example #2
Suppose UpMetals Ltd. had a total backlog of $0.5 million in deferred maintenance for its machinery as of December 31, 2021. Over the last three years, the company did not have sufficient funds to pay for machinery inspection by qualified engineers per the maintenance plan chalked out by its internal team.
On January 7, 2022, machinery worth $2 million broke down and halted production. As a result, the company had to call Stella, the engineer who led inspection and repair work at the factory. However, they had to pay Stella and her team emergency maintenance charges.
Stella then informed the managers that a key part of the machine was unrepaired and needed immediate replacement. This part cost the company $0.7 million. The production stoppage also resulted in the loss of earnings.
It is evident that deferred maintenance in machinery can cause heavy losses and expenses. Hence, scheduled and planned maintenance is necessary for the smooth functioning of a company.
Example #3
A December 2023 article about Kansas University’s building demolition decision brought certain key aspects of the deferred maintenance budget to the fore. To get rid of piled-up maintenance expenses, the Kansas Board of Regents decided to spend $16.5 million from the state treasury to demolish old buildings measuring 500,000 square feet across university campuses.
After the demolition of these 20 buildings, the board expected to save $80 million in deferred maintenance costs. The board saved money on activities like roofing, electrical, plumbing, heating, and cooling repairs. The article listed several other universities that took similar measures to avoid spending huge amounts of money on long-pending maintenance.
The article also offered insights into varied viewpoints and perspectives related to how fruitful such decisions are under different circumstances.
Deferred Maintenance vs Capital Expenditure
Delayed maintenance involves postponing asset repair and upkeep with a short-sighted view to gain immediate benefits. Capital expenditure refers to huge financial costs incurred for asset procurement. Though individuals and entities make these decisions for entirely different reasons, the former might affect the latter in specific cases.
The differences between the two are as follows.
Basis | Deferred Maintenance | Capital Expenditure |
---|---|---|
Meaning | It refers to the postponement of asset overhauling in the current period. | It is a one-time expense to purchase a fixed asset. |
Cost | It is a way of saving expenses in the current period, but it may lead to huge future costs. | It is a considerable cost a company incurs in a given period. |
Nature | It occurs due to a lack of skilled people, limited budget, material and time shortage, unavailability of parts, unnoticed defects or faults, or ignoring the importance of repair tasks in a company. | It serves crucial purposes like asset replacement or extension, investment in a capital asset, or procurement of an asset like machinery or equipment with updated features. |
Effect on Earning Capacity | It helps companies save money in the present but adversely impacts their future earning capacity. | A company incurs a high cost in the present, which increases its future earning capacity. |
Appears on Balance Sheet | Estimated deferred maintenance does not appear on a company’s balance sheet. | It is shown as a fixed asset on a company’s balance sheet, and depreciation is charged. |
Asset Improvement | It hampers asset improvement objectives. | It adds value, supports existing assets, and improves a company's assets situation. |
Frequently Asked Questions (FAQs)
The primary cause of delayed maintenance is an insufficient budget or a lack of resources like labor, material, or skilled personnel. Other reasons include the inability to detect the fault in machinery, property, or other assets. Companies that do not prioritize the upkeep of assets may ignore maintenance needs. In manufacturing units, workers intentionally delay such maintenance work to avoid production interruptions.
1. Safety hazards
2. Decrease in asset's useful life
3. Deteriorated asset performance
4. Machinery breakdown
5. Damage to property like buildings or equipment
6. Huge capital expenditure on account of replacement
7. Heavy repair costs in the future
Given below are some of the strategies to handle maintenance backlogs:
1. Regular audits
2. Categorizing maintenance tasks based on priority
3. Accelerating preventive maintenance activities
4. Allocating sufficient funds for maintenance work
5. Using asset management software
The estimated deferred maintenance amount is not documented on a company's balance sheet.
Recommended Articles
This article has been a guide to what is Deferred Maintenance. Here, we explain the concept along with its examples, and differences with capital expenditure. You may also find some useful articles here -