Table of Contents
What is Cycle Inventory?
Cycle inventory, or working stock, refers to that part of the standing inventory of a business that gets cycled continuously to fulfill the routine sales orders by the sellers. Businesses utilize it to meet the demands of customers in a timely manner while also maintaining higher-quality goods.
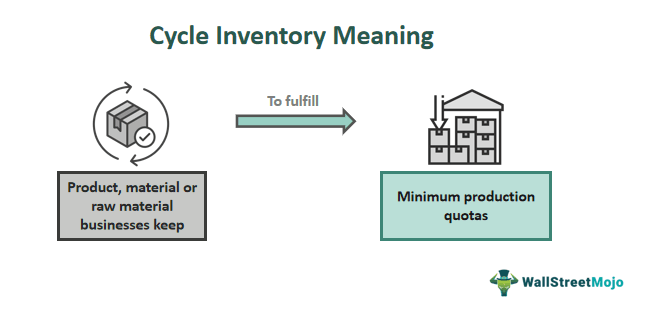
It forms an integral part of a firm's operations as it provides it with the products or materials needed for its daily operations. It also means frequent cycling of inventory so that the inventory gets replaced on a regular basis, contributing significantly to inventory tracking and production efficiency. Most business-to-business and direct-to-consumer businesses deploy it manually or using the software.
Key Takeaways
- Cycle inventory is the portion of a company's standing inventory that is continually cycled to satisfy the sellers' regular sales orders.
- Companies use it to satisfy client requests while simultaneously retaining higher-quality products quickly.
- It is that inventory anticipated to get sold per the forecast of customer demands. In contrast, safety inventory is the inventory kept in store as buffer stock for meeting any urgent excess demand beyond forecast.
- The formula for Cycle Inventory = Yearly Cost Of Sales / Average Inventory Level Throughout The Year.
Cycle Inventory Explained
Cycle inventory represents that proportion of inventory that has to be made available all the time to meet the customer demands of the product at any given point in time. Cycle inventory in the supply chain is the first option available to sellers to fulfill the immediate needs of their customers. Such a working stock helps businesses maintain the normal business cycle to maintain forecasts of sales and regular demand for products.
Cycle stock continuously replenishes the levels of stocks as the on-hand inventory levels decrease with demand from customers. Nowadays, companies conduct inventory counts along with their life cycle inventory by analyzing their inventory in the supply chain using standardized software solutions.
Nevertheless, when using any such software, companies utilize their historical data while considering seasonality, product lifecycle, and projected sales patterns to determine exact levels of cycle stock. Working stock plays a vital role in a firm's accounting systems as it leads to continuous cash flow through the replenishment of sold stocks.
Besides these, it has many benefits to the business if used wisely:
- It results in time and labor savings, leading to less time for inventory audit.
- It helps businesses discover shrinkage and variance in inventory quite quickly.
- It can be carried out during business hours to fully count the inventory without closing the business.
- One can easily focus on a particular product, causing issues with the inventory.
In order to take advantage of working stock, one has to take care of the following factors that may affect it: demand for the product, order costs, lead time, holding costs, product price, and discounts. Moreover, cycle stock helps a business survive the demands of customers and competition in the market. If the level of working stock lies on the higher side, then it means more costs for the business.
However, if the cycle stock level has a lower value, it indicates revenue loss for the company. Therefore, professional and accurate software must be used to conduct the analysis and help in company sales and revenue growth.
Formula
It remains a daunting task for businesses to keep the cost of inventory at a bare minimum while also never facing a stock crunch. In such a scenario, it becomes essential to find the working stock using the economic order quantity (EOQ).
Formula of EOQ = √
Where, in this equation:
- D = annual demand in units
- K = fixed cost per order
- H = annual carrying cost per unit
Another yet simplest, way to calculate:
Cycle Inventory = Annual Cost Of Sales / Average Inventory Level Throughout The Year
Examples
Let us use a few examples to understand the concept hidden in the topic.
Example #1
Realwood Furniture has an average sale of 5,000 study tables per year. The shop has,
To incur a cost of placing an order per study table = $300
Every study table has warehouse cost per year = $15
Therefore, EOQ = √ where in this equation:
D= 5,000
K= $300
H= $15
Or EOQ = √ = approx. 447 study tables
Hence, to maintain a level of 5000 study tables every year, Realwood shop would have to order 447 study tables every month.
Example #2
The led corporation manufactures LED bulbs in America. The company had the following:
Total amount utilized on manufacturing LED bulbs = $200,000
LED bulbs absorbed total inventory on an average basis = $50,000
Therefore, its Cycle Inventory = Annual Cost Of Sales / Average Inventory Level Throughout The Year
where,
- Annual Cost of Sales = $200,000
- Average Inventory Level throughout the Year = $50,000
- Hence, working stock = $200,000/$50,000= 4
Thus, LED Corporation has an inventory cycle of four days.
Cycle inventory vs Safety inventory
Let us understand the difference between the two terms using the table below:
Cycle Inventory | Safety Inventory |
---|---|
It is the inventor anticipated to get sold as per forecast of customer demands. | It is the inventory kept in store as buffer stock for meeting any urgent excess demand beyond the forecast. |
It is the first point of fulfilling customers’ demands. | Protect sellers from delays in stock shipments. |
Uses a specialized software to forecast the demand for the stock by the customers. | Safeguards the sellers from natural hazards or calamities. |
It accounts for a company’s net assets on its balance sheets. | It leads to some extra costs for the seller. |
Helps in the flow of cash for retailers. | It requires specialized inventory software to track these safety inventories. |