Table Of Contents
What Is Cost Element?
Cost Element is a specific cost category that classifies, records, tracks, and monitors the relevant expense items of the company in the charts of accounts. It is an inevitable part of cost accounting and financial reporting and contributes to accurate financial analysis and informed decision-making.
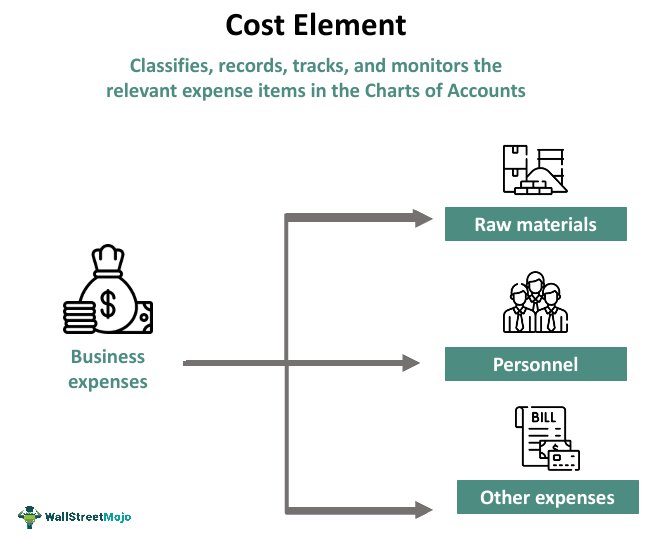
Hence, such categorization plays a vital role in financial management by providing a detailed breakdown of costs, comprising both direct costs like materials, labor, and other expenses and indirect costs such as indirect material, labor, and overheads. Moreover, it recognizes the excessive expenses and, thus, facilitates the framing of suitable cost reduction strategies while ensuring higher profitability.
Table of contents
- A cost element refers to a category within which a specific expense item of the business falls as per the charts of accounts. Such identification of different expense categories helps in robust cost framework administration.
- It contrasts with a cost center, which is a particular area, location, department, or function of a business entity where the cost is incurred or accrued.
- Primary cost elements are employed to record actual costs incurred in business activities directly, associating with specific accounts in the general ledger. In contrast, secondary cost elements serve internal purposes, facilitating cost distributions within the organization for reporting and analysis.
Cost Element In Cost Accounting Explained
A cost element in cost accounting serves as a distinct classification for expenses, including various categories like raw materials, labor, and overhead. Its primary role is to categorize and monitor costs within an organization, facilitating in-depth analysis of expenses associated with the manufacturing of goods or provision of services. Hence, they facilitate better cost allocation, effective budgeting, and managerial performance assessment.
Such components influence the overall cost of manufacturing goods or providing services. Some of the following include:
1. Direct Cost
The direct or prime cost is the total of direct materials, direct labor, and direct expenses directly linked to production. Let us discuss these components one by one:
- Direct material: This cost is associated with the raw materials directly utilized in the production process.
- Direct labor: This is the expense tied to the labor directly engaged in manufacturing or service provision.
- Direct expenses: These refer to additional costs directly associated with the production process, including specific expenses like machine-related costs or direct utility expenditures.
2. Indirect Cost
The cumulative cost of indirect materials, indirect labor, and indirect expenses incurred during the production process together form the factory overheads. It includes:
- Indirect materials: This is the cost of materials indirectly contributing to production, like supplies used across various processes.
- Indirect labor: It refers to the compensation provided to workers who are not directly engaged in the production process, including roles such as supervision or maintenance staff.
- Indirect expenses: These include additional overheads not directly attributed to a particular product or service, such as utilities, rent, or administrative expenses.
Limitations in cost categorization, including incomplete or inaccurate entries and inappropriate assignments, can disrupt budgeting and cost management. Challenges arise in tracking individual costs, particularly in scenarios with a high volume of financial transactions.
ExamplesÂ
The concept serves critical purposes in activity-based costing, target costing, process costing, and value chain analysis. Given below are some examples to help one understand the concept better.
Example #1
Suppose given below is a breakdown of cost elements for a tea manufacturing company, ABC Ltd.:
Cost Element | Amount | Purpose |
---|---|---|
Raw Materials (Tea Leaves) | $500,000 | Allocated for the procurement of tea leaves essential for production |
Labor Costs | $300,000 | Designated for compensating the workforce engaged in various stages of the tea manufacturing process, encompassing harvesters and production personnel |
Factory Overhead | $150,000 | Allocated for the upkeep and operation of the manufacturing facility, covering expenses such as utilities, maintenance, and other indirect production costs |
Packaging Materials | $50,000 | Reserved for the acquisition of packaging materials, including tea bags, boxes, and labels |
Administrative Expenses | $70,000 | Allocated for general administrative costs, covering items such as office rent, utilities, and salaries for non-production staff |
Example #2
Let us consider a technology-based company, XYZ Solutions, excelling in the development and marketing of innovative electronic devices. This business involves various cost elements, including:
- Material acquisition costs: This includes expenditures for procuring essential components such as advanced microchips, circuit boards, and sleek casings.
- Workforce expenses: Involving compensation for a skilled team, including engineers, assembly line workers, and support staff contributing to the manufacturing process.
- Innovation and development investments: These involve money dedicated to ongoing research and development efforts to introduce cutting-edge features and technologies to their product line.
- Distribution expenses: It comprises costs related to packaging, shipping, and logistics to ensure timely and secure delivery of products to customers.
- Quality assurance expenditures: Resources allocated to rigorous testing and inspection processes to uphold premium quality standards for the electronic devices.
- Technology infrastructure costs: Investments in software tools and technological infrastructure to support design, manufacturing, and overall business operations.
Cost Element vs Cost CenterÂ
These are two totally different concepts in business. Let us unfold these dissimilarities below:
Basis | Cost Element | Cost Element |
---|---|---|
Definition | It is a distinct category that tracks business expenses, such as labor or materials, distinguishing various types of costs. | A particular department, function, or location within a business where costs are accrued |
Denotes | A separate category of expenses | A specific unit, department, project, or location within an organization |
Purpose | Categories costs into specific types such as salaries, raw materials, utilities, etc., thus offering detailed insights into the nature of incurred expenses. | Facilitates the tracking and management of expenses within segmented organizational structures by designating the specific area where costs are accumulated or incurred |
Used in | Cost accounting and financial reporting | Budgeting, performance evaluation, and internal control |
Difference Between Primary And Secondary Cost Element
Let us understand the differences between each of the following in the table below:
Basis | Primary Cost Element | Secondary Cost Element |
---|---|---|
Definition | It comprises expenses directly linked to fundamental business operations. | It is an internal allocation mechanism for assigning costs from one profit center to another profit center within the organization. |
Purpose | Track costs associated with manufacturing goods or rendering services | Assist in distributing costs from primary elements |
Examples | Raw materials and direct labor | Production labor activity cost |
Used in | Financial accounting for creating Profit and Loss Accounts and General Ledgers | Cost accounting and controlling purposes |
Frequently Asked Questions (FAQs)
These are the following steps:
1. Access transaction code KA01 or navigate to Accounting -> Controlling -> Cost Element Accounting -> Master Data -> Cost Element -> Individual Processing -> Create.
2. Enter the controlling area.
3. Input details like number, name, category, and other relevant information.
4. Choose the category in SAP (e.g., primary costs, secondary costs).
5. Save the cost element.
The inventory holding typically encompasses expenses such as transportation, warehousing, labor, depreciation, insurance, obsolescence, and costs related to inventory shrinkage, damage, and opportunity costs. These elements represent the comprehensive array of expenses associated with holding and managing inventory within a business.
Yes, in SAP, specific attributes can be modified. However, it is essential to adhere to SAP best practices and guidelines when making any changes. Some core characteristics may have limitations on modification to ensure data integrity and accuracy in the system.
Recommended Articles
This article has been a guide to what is Cost Element. We explain its examples, differences with cost center, & comparison between primary & secondary cost element. You may also take a look at the useful articles below –