Table Of Contents
Cost Efficiency Meaning
Cost Efficiency is the business strategy relating to reduction in the cost of production without hindering the quality of the product or service. It is an important feature that helps an organization's profitability by generating better results with lesser capital requirements and providing value to their customers. They also allow decision-makers to make better decisions by assessing costs, benefits, and profitability.
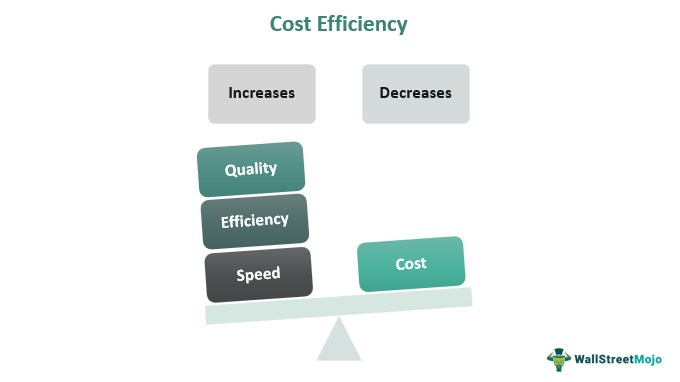
Organizations must compare output returns with input costs to carry out a cost efficiency analysis. Therefore, comparing the revenue created against expenses highlights the processes or products that have scope for improvement, can drive the overall costs down, and utilize funds optimally. For example, technological advancement, infrastructural development, or employee training programs can bring efficiency to the process.
Table of contents
- Cost efficiency is improving speed, quality, and effectiveness in producing a product or a service to reduce production
- costs.
- The difference between the total input costs in comparison to the returns from the output calculates it.
- A company being cost efficient not only aids higher revenue and profits but also helps them make better decisions regarding the betterment of the process.
- Cost efficiency can be achieved by implementing cloud-based or AI-enabled systems that help them find areas that need improvement. This process is more cost and time efficient than manually maintaining such details.
Cost Efficiency Explained
Cost efficiency is a business practice that saves money for the company by improving the process or product. Therefore, businesses must pay keen attention to details in this aspect as this cost efficiency strategy reduces procurement costs and improves efficiency in the production process.
Although cost efficiency does not address all issues for the business, it is an integral part of any business's strategy. It reduces costs and ensures processes' efficiency, saving time and effort.
As all businesses have their own needs and unique way of operating, it is crucial to conduct a cost-benefit analysis to maximize cost efficiency. The study helps them find areas of improvement and identify opportunities that, over time, help them reduce costs and increase efficiency efficiently.
The company must first prepare a list of all potential costs to conduct a cost-benefit analysis. The costs can include the following:
- Direct Cost: Labor, inventory, and raw materials.
- Indirect Cost: Overheads, rent, and utilities.
- Intangible Cost: Goodwill, Safety & security, and employee health.
- Opportunity Cost: Time constraints and outsourcing instead of in-house production.
- Risk-related Cost: Regulatory requirements, environmental effects, and competition.
Once these costs are calculated and accounted for, the business will derive a clearer picture of the potential benefits by improving the efficiency of managing these costs. The benefits include:
- Tangible Benefits: Increase in sales, revenue, and customer base.
- Intangible Benefits: Improvement in customer satisfaction, high team morale, and more efficient process.
- Competitive Advantage: Understanding the intricacies of the process helps any company gain the upper hand over its competitors, leading to a more significant market share.
How To Achieve?
The primary goal for most companies is to maximize cost efficiency. However, since the company's structure and the business's nature differ, companies adopt other techniques and strategies to become cost-efficient. A few ways for a company to become cost-efficient are discussed below:
#1 - Controlled Spending
Things that are not measured cannot be managed. Therefore, companies must take the help of software or an AI-driven tool that provides suggestions according to spending patterns. Otherwise, it is difficult for the manager to keep track of every activity within the company through the physical maintenance of these processes.
#2 - Automation
Cutting costs while continuously improving processes is one of the most sought-after ways to improve efficiency. Automation saves a significant amount of time and ensures delivery of the quality standard set by the company.
#3 - Innovation
In general, innovation is considered a process that aids in giving the customer a better experience. However, innovation in the production process helps reduce the company's costs, giving the company enough funds to ensure their customers a better experience. For example, manufacturing packaging material in-house instead of outsourcing it as it is cheaper to do so.
#4 - Moving To Cloud/AI Solutions
Moving data points to a cloud-based solution is tailor-made to ensure cost-cutting while keeping efficiency in mind. Moving to the cloud brings down the costs of setting up infrastructure and purchasing the equipment for storing and processing data.
Examples
Let us understand the concept better through the examples below:
Example #1
Allan Sounds manufactures customized ear monitors for musicians. They have been in the business for the last five years. In these years, they have gradually increased their presence in the market. However, upon conducting the cost-benefit analysis, they found that they spend close to 10% of their costs on packaging.
To cut down the costs of packaging, which still was one of the most important factors to attract customers, they decided to outsource this part of the process to a professional packaging company.
This collaboration gave the managers at Allan sounds more time to manage other parts of the process and saved the company $23,000 a year.
Example #2
Nikola Corporation is the market leader for heavy-duty commercial battery electric vehicles and energy solutions. In December 2022, they announced their partnership with E.ON Hydrogen to derive cost-efficient solutions for their customers across Europe.
Their partnership came in light of the costs of such trucks needing to be lowered for a few business owners.
Advantages
Let us discuss a few advantages of cost efficiency analysis through the points below:
#1 - Profitability
Among all other benefits, cutting costs helps the company grow profitably. In addition, the lower production cost gives them a better scope of using the funds available to give their customers better value.
#2 - Higher Revenue
When the costs of production or providing a service have been significantly cut down without hindering the quality levels, the company can produce more, reach more customers and thus, generate more revenue.
#3 - Value to Customers
The funds saved through optimizing and improving processes can be utilized towards better marketing, packaging, customer benefit programs, etc., ensuring better customer service. Over a while, this might enable more customer retention and improve customer loyalty.
#4 - Decision Making
Assessing the cost-benefit of a process or the overall production enables the management to make better decisions regarding how to make the whole process efficient. The analysis affects not only the production part of the business but also the sales, marketing, and logistics aspect of things. For example, if outsourcing logistics saves the company money rather than doing it alone, they shall outsource it to save time and money.
#5 - New Opportunities
When the intricacies of the process are looked upon, it gives fresh perspectives to the management and helps them explore different approaches to the daily activities within the organization. These discoveries might never have been made without analyzing the input costs compared to the outputs' returns.
Cost Efficiency vs Cost Effectiveness
The cost efficiency strategy is a popular tool to improve the process without tampering with the quality of the product or service across the globe. However, it often needs to be understood for cost-effectiveness, which despite being a similarly popular tool worldwide, has fundamental differences from the former. Let us know the differences through the table below:
Basis | Cost Efficiency | Cost Effectiveness |
---|---|---|
Function | Cost efficiency is when the company achieves the goal with minimal resources without compromising quality. | Cost-effectiveness denotes how well organizations achieve their goals. |
Relationship | It is the difference between the input costs and the returns from the output. | It is a relationship between available resources and the results achieved. |
Analysis | Quantitative | Quantitative and qualitative |
Factors | The production process, technology, and employee training. | The business facility, equipment, and vendors. |
Frequently Asked Questions (FAQs)
Cost efficiency is the net difference between the costs of input to the returns from the output. It implies that the costs involved in producing a product or service must be reduced without lowering the quality to improve efficiency in optimally handling funds.
In business, cost-efficient means improving the production process by changing a product or how the process is currently carried out. Therefore, it is analyzed and implemented to ensure better utilization of funds and lower wastage.
One of the fundamental reasons for advertisers and marketers to be stringent with cost efficiency is to ensure the marketing costs are not more than the returns per unit sold. Because often, it so happens that the marketing costs are high and do not deliver the desired level of sales, which burns a hole in the company's pockets.
Recommended Articles
This has been a guide to Cost Efficiency and its meaning. We explain how to achieve it, its examples, and a comparison with cost-effectiveness. You can learn more about financing from the following articles –