Table Of Contents
What Is Capacity Requirements Planning (CRP)?
Capacity Requirements Planning (CRP) refers to the process of matching the current production capabilities with the production goals set by the company. The goal of CRP is to align an organization's capacity with its demand to optimize efficiency and maintain customer satisfaction.
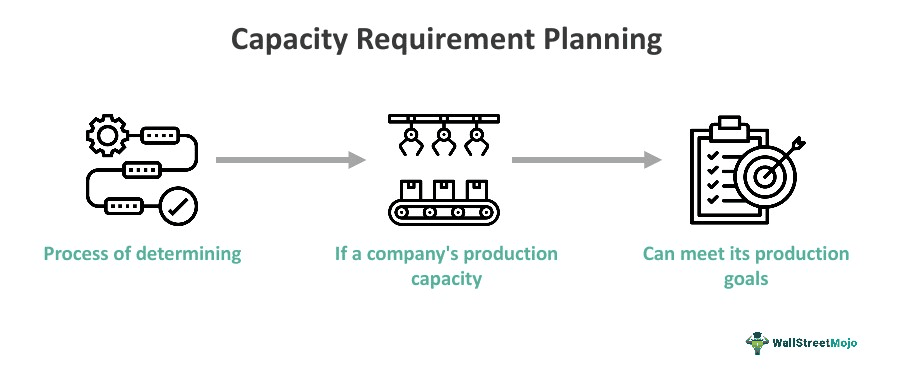
In manufacturing and production-based businesses, robust operational planning and efficient resource utilization widely employ this phenomenon as a crucial factor for ensuring profitability. Moreover, this approach facilitates the organizations' development of innovative strategies to streamline the manufacturing process. It even ensures that the company has the most productive machines and human resources. In order to deliver quality output for enhancing customer satisfaction.
Table of contents
- Capacity requirement planning is a process that organizations use to ensure that they have the resources to meet their production goals.
- This process involves forecasting future market demand, examining existing production capabilities, and implementing strategic plans for adjustments to infrastructure, staffing, or procedures.
- While it signifies a detailed resource alignment and short-term perspective. RCCP provides an initial evaluation of resource feasibility over a broader time horizon.
Capacity Requirements Planning Explained
Capacity requirements planning aids organizations in optimizing resource utilization, minimizing bottlenecks, and ensuring efficient responsiveness to customer demands. It is widely used in diverse industries including consumer products, automotive, industrial manufacturing, foods and beverages, electronics, pharmaceuticals, and tech industries. Moreover, it can be categorized as follows:
- Product Capacity Planning: It helps the firm identify the availability of sufficient and appropriate material resources. Therefore, it is important to serve the customer demand and anticipate any required changes with a rise in demand.
- Workforce Capacity Planning: This form of planning gauges the sufficiency of human resource capital, competencies, and contribution to meet production needs.
- Tool Capacity Planning: As the name suggests, this type of requirement planning analyses the overall resource availability. This includes material, staff, tools, and time for accomplishing the work efficiently.
The capacity requirements planning process, in operations management, is a comprehensive effort. It aims to evaluate and manage an organization's ability to meet both current and future demands. The key steps involved are as follows:
- Demand Forecasting: The foremost step is to identify the service level requirements. It is done by anticipating future demand for products or services which is done through the analysis of historical data, market trends, and relevant factors.
- Capacity Assessment: Next comes the evaluation of the existing resources, such as facilities, equipment, material, and personnel, to ascertain current capacity levels.
- Gap Analysis: Further, it is essential to compare the projected demand with the current capacity. Hence, to determine any gaps or potential inadequacies in the production capacity.
- Strategic Planning: The final step is the formulation of suitable strategies to address capacity gaps at present and in the future. It involves decisions related to expanding facilities, acquiring new equipment, or hiring additional staff.
Strategies
Integrating the capacity requirements planning strategies with business goals helps the organizations become competent. Given below are the various strategies:
- Demand Prediction: The foremost strategy is to utilize historical data and market trends for accurate forecasting of future demand.
- Resource Distribution: It is critical to regularly monitor resource usage and allocation to identify areas that may be underutilized.
- Technology Alignment: The companies should stay updated with technological advancements to enhance efficiency and capacity.
- Capacity Buffering: It is equally essential to maintain buffer capacity to handle unexpected demand spikes or unforeseen disruptions.
- Skill Development and Training: The company should run training programs to ensure that employees possess a versatile skill set for flexible resource allocation.
- Strategic Collaborations: A business runs through outsourcing or partnerships; thus, collaborating with suppliers for resource availability helps to eliminate shortages.
- Real-Time Monitoring: Regularly monitoring and improving the production capacity planning processes using real-time data is crucial for business success.
- Production Scheduling: Companies should have a production schedule that is realistic and data-driveo as to serve customers' needs and demands promptly.
Examples
Let us find out some examples to understand its practical implications:
Example #1
Suppose Shinola Innovations is a specialist in the production of advanced smartwatches in the US. To streamline its operations, the company employs a Capacity Requirements Planning system:
- Demand Forecast: The company estimates a future demand of 1000 smartwatches in the upcoming week.
- Capacity Analysis: On examining the current capacity, it was evident the firm produced 900 smartwatches in a week.
- Identify Gap: The manager finds a capacity lag of 100 smartwatches.
- Strategic Planning: With extra working hours in the night shifts for the most competent workers in the production team. The company can manage to pull the production goal with efficiency.
Hence, the company continuously reviews and updates its capacity plans, incorporating feedback from the production floor, market dynamics, and changes in customer preferences. This iterative approach ensures that the organization remains agile and responsive to evolving conditions. Hence, this allows the firm to adapt its capacity to meet the demands of a dynamic market environment.
Example #2
Quantzig, is a global provider of data analytics and consultancy services. It has announced the conclusion of its most recent capacity requirement planning project. In this project, Quantzig worked with a US-based CPG company to increase order fill rates and workflow effectiveness.
In a recent project, Quantzig worked with a US-based maker of consumer packaged goods. It assisted them in overcoming the difficulties brought on by the spike in demand for goods during the crisis. A thorough investigation showed that the customers were having a number of supply chain issues as a result of their absence of a structured framework for capacity planning and optimization.
Advantages And Disadvantages
Capacity requirements planning in operations management is a crucial consideration. Therefore, organizations should carefully weigh its pros and cons, ensuring alignment with their specific needs and capabilities. Some of them are discussed below:
Advantages
- Efficient Resource Allocation: The importance of capacity requirements planning aids organizations in effectively assigning resources, both material and human, by determining the optimal capacity of production needed.
- Better Customer Service: It ensures consistent fulfillment of customer demands without compromising with the quality, thus leading to heightened consumer satisfaction and loyalty.
- Cost Optimization: CRP constantly tracks the production and operational costs, hence ensuring the judicious use of resources by avoiding unnecessary investments in excess capacity.
- Robust Decision-Making and Growth Planning: Provides data-driven insights for informed decision-making on business expansion, production schedules, staffing, and facility investments at new locations.
- Flexibility and Risk Mitigation: Since it involves demand forecasting, it helps curtail risks associated with demand fluctuations, market changes, or disruptions in the supply chain, allowing companies to change strategies accordingly.
- Higher Profitability: With constant practice of efficient resource utilization and cost reduction, companies can enhance their overall profitability.
Disadvantages
- Complexity: The implementation and management of these requirements planning systems can be complicated, demanding considerable time, effort, and technology.
- Prone to Inaccuracy: Such decisions majorly rely upon accurate demand forecasting and assumptions about future demand, which is the biggest challenge in volatile markets.
- Inefficient for Sudden Demand Fulfilment: The process is rigid and doesn't allow for quick adaptations to immediate demand changes or unforeseen circumstances.
- High Implementation Cost: It is difficult for small business entities to adopt this process since the initial setup costs of developing technology infrastructure and staff training are enormous.
Capacity Requirements Planning vs Rough-Cut Capacity Planning
Capacity requirements planning (CRP) and rough-cut capacity planning (RCCP) are two different concepts in operations management. Let us see how they differ:
Basis | Capacity Requirements Planning (CRP) | Rough-Cut Capacity Planning (RCCP) |
---|---|---|
Definition | It is a meticulous process of detailed analysis of production schedules, workloads, and resources to ensure the organization can meet demand effectively. | RCCP provides an initial overview of capacity requirements and constraints without penetrating specific scheduling details. |
Purpose | Aims to streamline and optimize capacity at a detailed level, ensuring specific production requirements are efficiently met | Focuses on identifying potential capacity issues at a higher level, aiding organizations in making strategic decisions about resource allocation and expansion |
Depth of Analysis | An in-depth examination of individual facilities, machines, and personnel requirements, production orders, and schedules | A more generalized view, concentrating on overall capacity needs without inspecting specific production orders or detailed schedules |
Time Frame | Performed in a short period, say every day or every week | Longer time horizon covering weeks to months |
Inputs | Uses information from production schedules, bills of materials, production orders, timesheets | Therefore, it uses aggregate production plans, forecasts, and rough estimates of resource capacities. |
Frequently Asked Questions (FAQs)
It is a strategic process of determining the overall capabilities of an organization to meet both current and future demands. In contrast, capacity requirement planning is a more detailed and tactical approach. Which involves identifying and allocating specific resources to address immediate capacity needs, considering factors such as workload and demand fluctuations.
CRP focuses on assessing and aligning the available resources engaged in production, such as labor and machines, with the production plans generated by (MRP), preventing resource overloading or underutilization.
Meanwhile, MRP is primarily concerned with the planning and control of material resources essential for production. It involves determining the quantity, quality, and time of the required material to accomplish the production efficiently.
The key components include demand forecasting, current capacity assessment, capacity gap analysis, strategic planning, resource allocation, risk assessment, monitoring and control, scenario planning, collaboration with stakeholders, and continuous improvement.
Recommended Articles
This article has been a guide to what is Capacity Requirements Planning. We explain its examples, strategies, and comparison with rough-cut capacity planning. You may also take a look at the useful articles below –