Table Of Contents
What Is Capacity Planning?
Capacity planning determines the production capacity needed by an organization to meet changing product demands. The purpose of capacity planning is to ensure that an organization has enough capacity to meet customer demand while minimizing excess capacity that results in waste and increased costs.
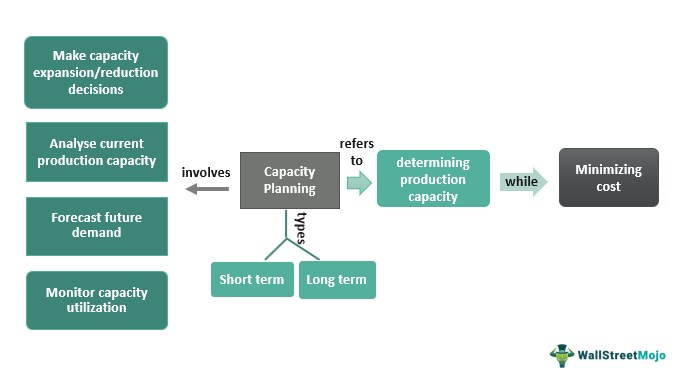
It involves analyzing current production capacity, forecasting future demand, and deciding on capacity expansion or reduction investments. By effectively implementing capacity planning, organizations can ensure they have the necessary resources to meet customer demand and remain competitive in their markets.
Table of contents
- Capacity planning determines the production capacity needed by an organization to meet changing product demands. Its types include short-term and long-term.
- Capacity planning ensures the sufficient capacity to meet customer demand, reduce costs, and improve efficiency.
- The main disadvantages of capacity planning include the difficulty in accurately forecasting demand and the need for continual monitoring and adjustment.
- Capacity planning differs from resource and demand planning, each having a different focus and purpose.
Capacity Planning Explained
Capacity planning is a crucial process for organizations. It helps ensure they have the sufficient production capacity to meet customer demand while minimizing excess capacity that results in waste and increased costs.
Organizations must understand their current production capacity and future product demand to implement capacity planning effectively. Moreover, this information can be gathered through market research, customer data, and other sources and is used to determine the necessary production capacity needed to meet demand.
Another important aspect of capacity planning is monitoring capacity utilization over time and making adjustments as needed. Also, this can involve investing in new production capacity, reducing existing capacity, or making other changes to ensure the organization has the resources it needs to meet customer demand.
Overall, capacity planning is a critical process that helps organizations maintain a balance between having enough production capacity to meet demand and avoiding the waste and increased costs resulting from too much capacity.
Process
The process of capacity planning involves several key steps:
- Analysis of current production capacity: This involves evaluating an organization's current capacity and identifying any bottlenecks that may limit its ability to meet customer demand.
- Forecasting future demand for products: This involves using market research, customer data, and other sources to estimate future demand for an organization's products.
- Determining the capacity needed to meet demand: This involves using the demand forecasts from the previous step to determine the necessary production capacity needed to meet customer demand.
- Making decisions on capacity expansion or reduction: It involves determining whether the organization needs to invest in new production capacity, reduce existing capacity, or make other adjustments to meet demand.
- Monitoring capacity utilization and making adjustments as needed: This involves tracking the utilization of an organization's production capacity over time and making changes as needed to ensure that it remains aligned with customer demand.
Types
There are two main types of capacity planning:
- Short-term capacity planning focuses on immediate capacity needs and is usually done daily or weekly.
- Long-term capacity planning focuses on capacity needs over a year or more over a longer period. It is used to make strategic decisions on capacity expansion or reduction investments.
Examples
Let us have a look at the examples to understand the concept better.
Example #1
Let us take an example of capacity planning of a bakery that produces cakes for special occasions. The bakery starts by analyzing its current production capacity, which includes the number of ovens, mixers, and other equipment available. It then forecasts the demand for cakes for the next few months based on past sales and special occasion schedules. The bakery must have enough capacity to produce 200 cakes per day to meet the demand.
Based on this analysis, the bakery decided to invest in capacity expansion by purchasing additional ovens and mixers. Also, the bakery continually monitors its capacity utilization and adjusts as needed to meet customer demand while minimizing waste and costs.
For example, if the demand for cakes decreases, the bakery may reduce capacity by selling or storing some of its equipment. The goal of capacity planning for the bakery is to ensure that it has enough capacity to meet customer demand while maximizing efficiency and minimizing costs.
Example #2
Consider that a manufacturing company produces a popular product that has experienced a significant increase in demand over the past few months. As a result, the company has been running at full capacity, and the production team is struggling to keep up with the growing demand.
The company decides to engage in capacity planning to ensure that it can meet the growing demand for its product in a timely and cost-effective manner. The first step is to analyze the company's current capacity and identify any bottlenecks in the production process.
Based on this analysis, the company invests in new machinery and equipment to increase its capacity. This investment is expected to increase the company's overall capacity by a certain percentage, allowing it to meet the growing demand for its product.
In addition to the new machinery and equipment, the company also decided to implement a new production schedule optimized for efficiency and cost-effectiveness. The new schedule includes changes to the company's work processes, staffing levels, and inventory management strategies.
The combination of new machinery and equipment and the optimized production schedule is expected to significantly increase the company's capacity, allowing it to meet the growing demand for its product while reducing production costs.
Importance
Capacity planning is important for several reasons, including:
- Ensuring that an organization has enough capacity to meet customer demand.
- Minimizing excess capacity and waste.
- Reducing costs associated with underutilized capacity.
- Improving overall efficiency and competitiveness.
Disadvantages
The main disadvantages of capacity planning include the following:
- Difficulty in accurately forecasting future demand.
- The high cost of investing in capacity expansion or reduction.
- The potential for capacity utilization fluctuates, leading to overcapacity or under-capacity.
- The need for continual monitoring and adjustment as demand changes.
Capacity Planning vs Resource Planning
Parameters | Capacity Planning | Resource Planning |
Definition | The process of determining the production capacity needed by an organization to meet changing demands for its products. | The process of determining the resources (e.g., materials, labor, machinery) needed to meet production demand. |
Focus | Capacity utilization | Resource utilization |
Objective | To ensure sufficient capacity to meet customer demand while minimizing excess capacity. | To ensure that necessary resources are available to meet production demand. |
Time Horizon | It can be both short-term and long-term. | Usually short-term, but may also include long-term projections. |
Key Elements | Production capacity, demand forecasting, capacity utilization. | Resource allocation, resource utilization, resource allocation optimization. |
Importance | Ensures sufficient capacity to meet customer demand reduces costs, and improves efficiency. | Ensures availability of necessary resources to meet production demand, improves resource utilization and optimizes resource allocation. |
Considerations | Balancing capacity utilization and excess capacity, minimizing waste. | Allocating resources effectively, optimizing resource utilization, and reducing resource waste. |
Capacity Planning vs Demand Planning
Parameters | Capacity Planning | Demand Planning |
Definition | The process of determining the production capacity needed by an organization to meet changing demands for its products. | Demand planning is the process of forecasting customer demand for a company's products and services. |
Focus | Production capacity | Customer demand |
Objective | To ensure sufficient capacity to meet customer demand while minimizing excess capacity. | To accurately forecast customer demand for the company's products and services. |
Time Horizon | It can be both short-term and long-term. | Usually short-term, but may also include long-term projections. |
Key Elements | Production capacity, demand forecasting, capacity utilization. | Customer demand forecasting, market trends, and demand patterns. |
Importance | Ensures sufficient capacity to meet customer demand reduces costs, and improves efficiency. | Improves demand forecasting accuracy and allows companies to better prepare for and meet customer demand. |
Considerations | Balancing capacity utilization and excess capacity, minimizing waste. | Accurately forecasting demand, considering market trends and demand patterns. |
Frequently Asked Questions (FAQs)
Capacity planning in agile involves regularly adjusting the capacity of an organization's teams and resources to meet project demands by determining team capacity, prioritizing the backlog, tracking progress, and making adjustments as needed.
Capacity planning in manufacturing determines the production capacity needed by a manufacturing organization to meet the demand for its products. It involves analyzing current production capacity, forecasting future demand, and deciding on investments in capacity expansion or reduction to ensure efficient utilization of resources and meet customer demand. The goal is to minimize excess capacity, increase efficiency, and reduce costs.
In scrum, the responsibility for capacity planning lies with the Scrum team. The team comprises the Product Owner, Scrum Master, and Development Team, who work together to plan and estimate the work that needs to be done in a sprint. The team is responsible for ensuring that they have enough capacity to meet the sprint commitments and deliver a valuable product increment at the end of the sprint.
Recommended Articles
This has been a guide to what is Capacity Planning. We explain its examples, types, process, importance, disadvantages, & comparison with resource planning. You can learn more about it from the following articles –