Table Of Contents
What Is Batch Picking?
Batch Picking, also called multi-order picking, is a method of picking products from the same or different orders in batches from distribution centers or warehouses, sorting them, and placing them in the appropriate staging locations. The most common method of carrying out this process is by grouping orders based on Stock Keeping Units (SKUs).
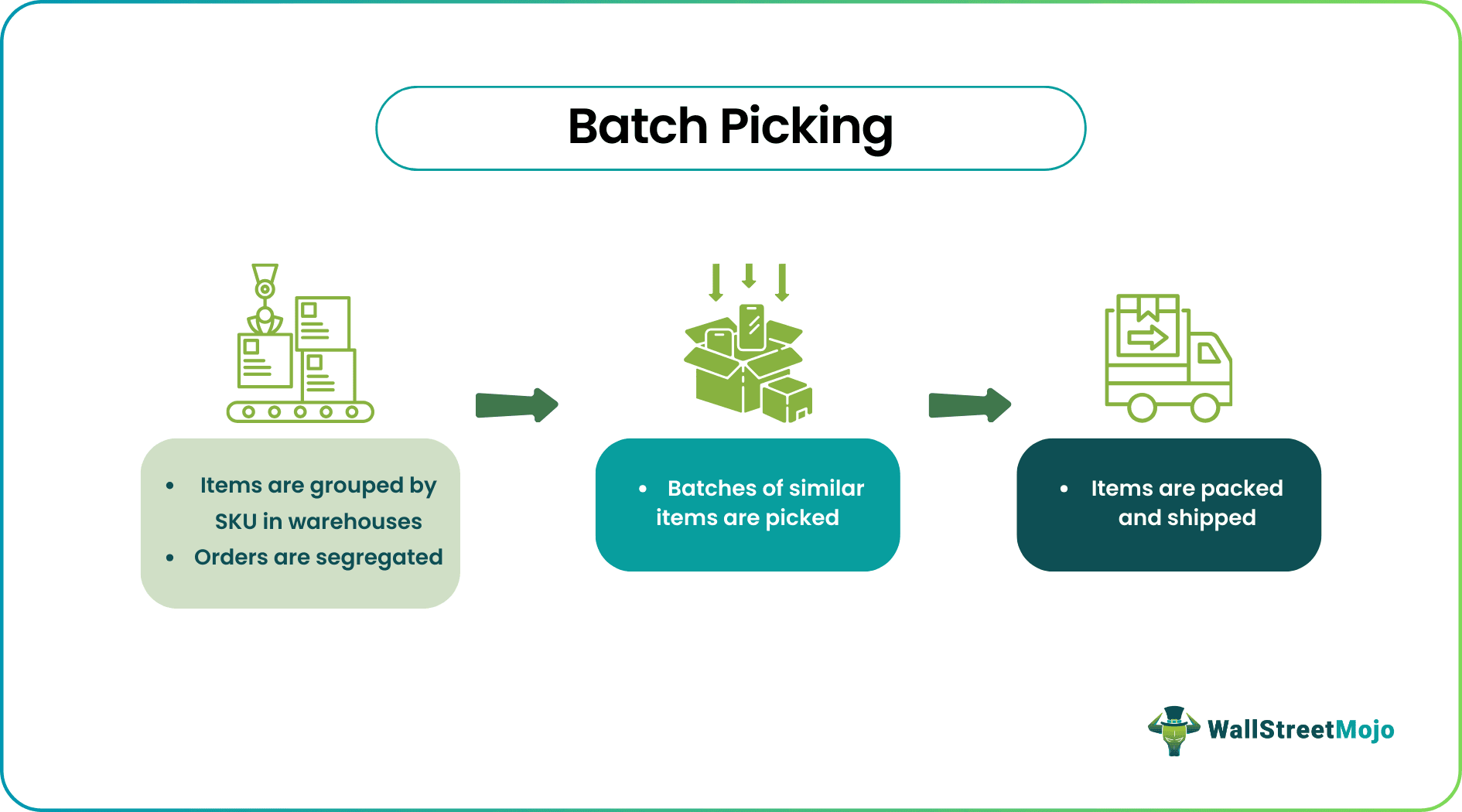
It is a method that reduces the number of store associate visits to a department by maximizing pick quantities and minimizing the distance traveled. This method is more efficient than traditional pick procedures, which involve completing the pick procedure for each order individually. It makes room for multiple orders to be fulfilled and the back room to be cleared simultaneously.
Key Takeaways
- Batch picking is a process that arranges orders into batches to maximize pick quantities and minimize travel, resulting in improved productivity and picking efficiency.
- The advantages of batch picking include lower overheads, swift order fulfillment, reduced travel time and stock movements within the warehouse, and increased picking accuracy.
- The disadvantages of batch picking include complicated sorting and grouping processes, potential delays due to conflicting priorities within a batch, and high initial implementation costs.
- Companies may adopt different batch picking strategies, including manual operations, automated operations, and grouping.
Batch Picking Process Explained
Batch picking is a systematic process that maximizes pick quantities and minimizes distance traveled through an arrangement of orders into batches. It reduces department visits and time spent on tasks. It expedites store operations by selecting products from orders in batches, sorting them, and placing them in staging locations, ensuring efficient handling of products at various stages of production. The process reduces expenses related to manpower, inventory holding, and logistics.
After picking, orders are sorted, having been grouped according to related items, locations, or other factors. From a financial perspective, this technique can decrease labor expenses and help control operating costs. It also reduces travel time and equipment utilization while increasing picking accuracy and speed. It can effectively enhance order tracking and inventory management. However, longer sorting times, more space requirements, and higher mistake or error rates are possibilities.
Manual operations, automated operations, and grouping are the various batch picking strategies a warehouse or distribution center may consider implementing. Manual operations involve generating pick lists. Pick lists are created for every order, indicating the items that must be taken from inventory. In automated operations, batches of orders are directed to specific zones via automated processes, which are then sorted according to commonality (SKU, location, etc.). At this stage, each operator receives SKUs for picking from their assigned batch.
Orders in each batch picking warehouse should be similar in order to streamline the process and minimize needless travel. They are categorized automatically by the software according to common features. Once picked and delivered, items proceed to either the next zone for further consolidation or directly to the sorting and packaging area before shipment.
Examples
Here are a few examples to facilitate further discussion.
Example #1
Suppose Daisy is a manager in charge of a warehouse for an e-commerce website selling apparel. She receives a bunch of orders every day, and by implementing batch picking, Daisy combines orders with similar products or destinations into batches. She does this to reduce the number of trips required to her warehouse. This results in faster picking, reduced labor costs, and improved customer satisfaction due to quicker order processing and shipment.
To understand how batch picking works in an e-commerce clothing company, let us consider Daisy receiving an order. Suppose three customer orders (Eva, Jenny, and Sarah) require picking. They have placed the following orders:
- Eva: 30 pairs of socks, 20 blue T-shirts, 10 green suits
- Jenny: 20 pairs of socks, 10 blue T-shirts, 15 hand towels
- Sarah: 10 pairs of socks, 5 blue T-shirts, 2 green suits
Instead of picking each customer's order individually and moving to the next, Daisy asks pickers to follow the batch picking approach. They would start by picking all 60 pairs of socks for the three customers and placing them in a designated space on a pushcart. Next, the picker would gather all blue t-shirts, which are 35 in all, and put them in another tote on the same cart.
The individual would then collect the 15 hand towels specifically for Jenny and place them in a separate tote. Before picking the green suits for Eva and Sarah, which are larger items that cannot fit on the pushcart, the selector would transport the socks, t-shirts, and towels to the sorting area. Finally, the picker would gather all green suits into a single cart and bring it to the sorting area to be sorted and packed along with the other items for shipping.
In this way, Daisy simplifies her daily picking, sorting, and packing tasks and saves money in the form of reduced labor and logistics costs.
Example #2
In the Business-to-Consumer (B2C) setting, businesses receive multiple customer orders daily, and the order sizes vary. Many times, the order sizes are small. Due to this, the volume of shipments increases. To thrive in an environment that demands speed and efficiency, companies must streamline operations at every level. A study was conducted in this area to understand the challenges seen in the Integrated Order Picking-Vehicle Routing Problem (I-OP-VRP) in e-commerce.
It investigates two picking policies: discrete order picking and batch order picking. The study explores the benefits of integration across various problem contexts, such as limited picking timeframes, outsourcing to third-party logistics (3PL) providers, and dynamic environments.
The study introduced a batch-picking policy in an I-OP-VRP, combining multiple orders in a batch to be picked on the same trip. This reduced the total picking time needed, resulting in a 37% average decrease in total labor cost, where 10 customer orders were considered. In an integrated approach, a lower number of order pickers are required to pick all goods, resulting in a decrease in total labor cost.
Another aspect discussed in this paper is an uncoordinated approach to order picking. It states that if the period between the cut-off time and the picking due date is small, integration can prove more valuable. If sub-problems are integrated, different orders can be batched, leading to a lower total picking time.
While the cost and time savings largely depend on how logistical decisions are made, the study shows that batch picking holds the potential to deliver better results that enhance cost management and improve lead time control than other warehouse management processes.
Advantages And Disadvantages
The advantages and disadvantages of batch picking have been discussed in this section.
Advantages
- Pickers can minimize commuting and maximize pick quantities by picking multiple orders in one trip, which significantly improves overall productivity and efficiency.
- When travel time is reduced, fewer pickers need to be employed per order, leading to lower labor costs.
- It optimizes space utilization, reducing the overheads of a warehouse or distribution center.
- Once picking processes run smoothly in a structured manner, order fulfillment and delivery improves. This enhances customer satisfaction and increases repeat orders.
- By grouping orders, internal activities that require manpower for movement, sorting, and packing are optimized. This reduces costs as well as labor fatigue.
- Increased precision and decreased picking errors are expected since sorting and packing processes are streamlined.
Disadvantages
- Sorting, grouping, and packing orders may become complex, particularly if picking processes are not planned and implemented well.
- When software is deployed for warehouse management, people with limited technical skills may find it difficult to follow the prescribed steps.
- When orders are batched, some may get delayed, as multiple deadlines or priorities need to be accommodated.
- The initial expenses for implementation and setup can be heavy for certain warehouses and distribution centers.
Batch Picking vs Wave Picking
The differences between these concepts are given below:
- Definition: Batch picking involves picking multiple orders or items simultaneously in groups or batches. It typically involves a single picker selecting multiple orders simultaneously, aiming for an optimal pick path. Wave picking divides orders into waves or groups, picks them sequentially, and processes them all at once. The criteria may be based on size, shipping, or location.
- Approach: It consolidates orders into a single picking trip, focusing on maximizing pick quantities and minimizing travel. Wave picking separates orders into waves and picks them one wave at a time, focusing on order prioritization.
- Picking Sequence: Items from different orders are picked together when batch picking is followed. In wave picking, items from the same order are picked together in a wave.
Batch Picking vs Cluster Picking v Order Picking
The differences between these concepts have been enumerated in the following table.
Points | Batch Picking | Cluster Picking | Order Picking |
---|---|---|---|
Definition | Batch picking is the process by which a warehouse worker receives multiple orders, each requiring them to pick up every item at once and deliver them all to the packing station. | Cluster picking is a method of piece picking where items for multiple orders are picked simultaneously by grouping them into clusters based on their physical proximity. | Order picking, on the other hand, is the process of selecting the correct products from a warehouse to fulfill a specific order. |
Grouping Logic | This groups orders together based on shared characteristics or customer requirements. | Cluster picking groups items together based on their physical proximity within the warehouse. | Order picking involves selecting individual items for each specific order. |
Picking Approach | This involves picking multiple items or orders with similar characteristics together in a consolidated trip. | Cluster picking focuses on picking items that are close to each other to minimize travel time. | In contrast, order picking entails selecting items one by one for each specific order. |
Frequently Asked Questions (FAQs)
Batch picking differs from discrete picking as it involves selecting multiple orders or items collectively in batches. Discrete picking entails picking individual orders or items separately.
Batch picking strategies include grouping orders with similar characteristics or customer requirements, optimizing order sequencing, and planning efficient picking routes to minimize travel time.
Compared to single order picking, batch picking involves picking multiple orders or items together in batches. In contrast, single order picking focuses on selecting individual orders or items one by one.
The principle behind batch picking is to consolidate multiple orders or items into batches, enhancing efficiency by reducing travel time. It also involves increasing productivity and optimizing resource utilization, such as picking equipment and labor.