Table Of Contents
What Is Average Cost?
Average cost refers to the per-unit cost of production, which is calculated by dividing the total cost of production by the total number of units produced. In other words, it measures the amount of money that the business has to spend to produce each unit of output. It forms a fundamental component of demand and supply that affects the supply curve.
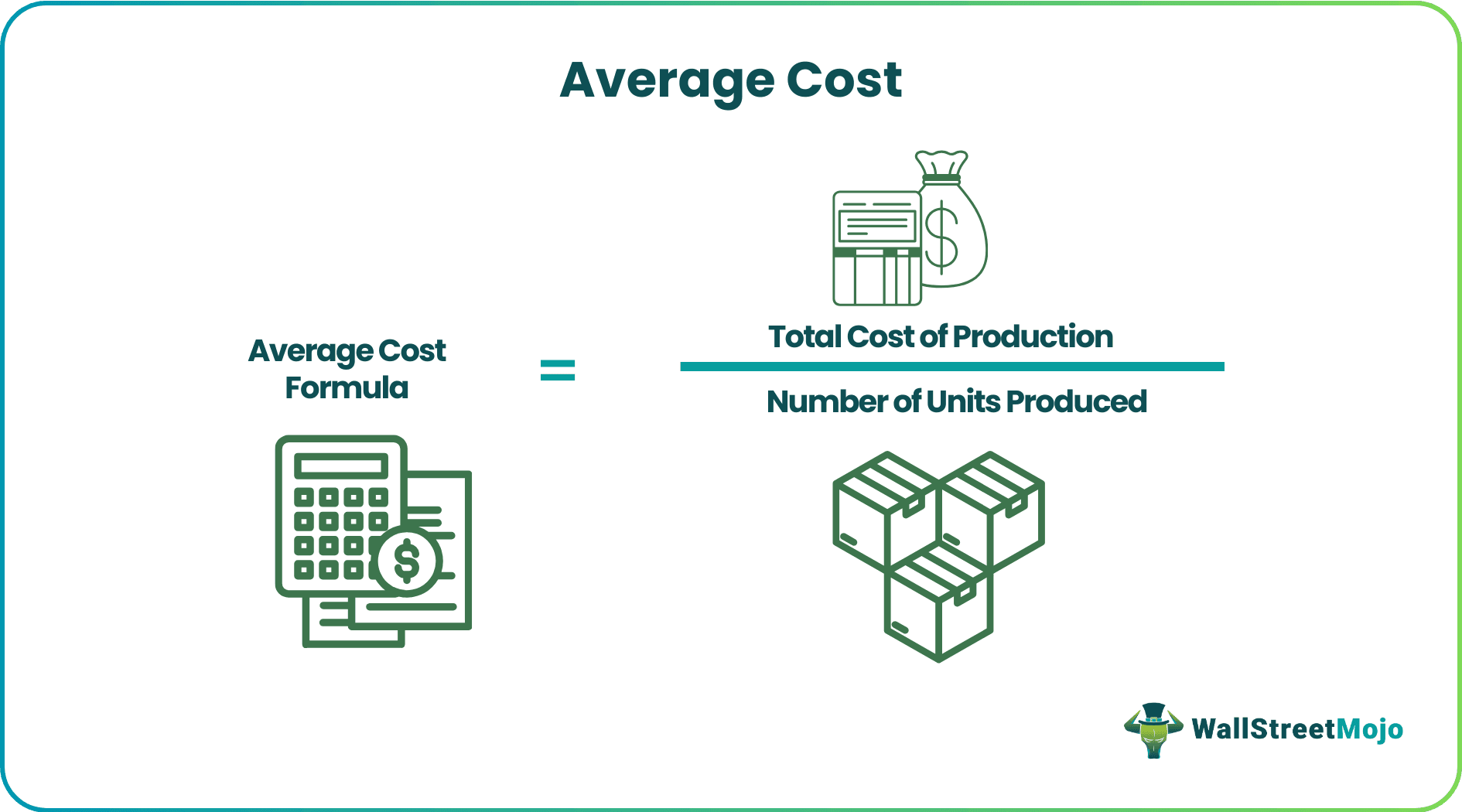
It is also known as unit cost or average total cost. We can further break down the total cost of production into fixed and variable cost components. Generally, the total fixed cost component doesn’t change, and hence the change in average cost is primarily due to a change in total variable cost. If the cost reaches the threshold, it is advisable to either increase the selling price or negotiate the variable cost component, as otherwise, it will result in business loss.
Average Cost Explained
The concept of average cost helps determine the amount spent per unit of an item. It is widely used in various contexts of finance or business to measure the price of products, expenses incurred to produce them, or the profit level that can be earned from manufacturing those products.
The average cost method accounts for the per cost including the fixed and variable ones like rent , salary, labor cost , raw material cost, etc. The average cost is calculated by dividing all the cost incurred for a process by the number of units produced. The inventory valuation and accounting process uses this concept to determine how much inventory storage is profitable, how much might lead to excess or wastage of resource, what is the minimum or maximum level to be maintained, etc. This helps manufacturers plan their production process.
Business analyse this cost to control wastage, and earn maximum profit. Product pricing is the most important decision of the business, which depends on the cost. In this way the producers take informed business decisions, thus contributing to their profitability.
Overall, the knowledge regarding average cost method in the finance and business environment helps in decision making, budgeting and increasing the profitability of the company.
How To Calculate?
We can calculate it by following these five steps:
Step 1: : Firstly, determine the fixed cost of production incurred during the given period, including salary, depreciation & amortization, lease rental, marketing & advertising expenses, etc. These cost heads don’t change with the change in production volume.
Step 2: Next, determine the variable cost of production incurred during the given period, including the cost of raw materials, wages, electricity bill, etc. These cost heads are mainly dependent on the production volume.
Step 3: Next, calculate the total cost of production by adding up fixed (step 1) and variable cost of production (step 2).
Total Cost of Production = Fixed Cost of Production + Variable Cost of Production
Step 4: Now, determine the number of units produced during the given period.
Step 5: Finally, process of the average cost calculation of production is done by dividing the total cost of production (step 3) by the number of units produced (step 4), as shown below.
Average Cost Formula = Total Cost of Production / Number of Units Produced
Examples
Let us analyse and understand the concept with the hep of some suitable examples.
Example #1
Let us take the simple example of the manufacturing plant of ASF Inc., where the total fixed cost of production during the year was $100,000, and the variable cost of production was $20 per unit. Next, determine the average cost of production if the company manufactured 20,000 units during the year.
Given,
- Variable cost per unit = $20
- Number of units produced = 20,000
- Total fixed cost of production = $100,000
Solution:
Calculation of Total variable cost of production will be –
The total variable cost of production = Variable cost per unit * Number of units produced
Total variable cost of production = $20 * 20,000 = $400,000
Now, the calculation of the total cost of production is as follows:
Total cost of production = Total fixed cost + Total variable cost
Total cost of production = $100,000 + $400,000 = $500,000
Now, the calculation is as follows:
Average cost Formula = Total cost of production / Number of units produced
= $500,000 / 20,000 = $25 per unit
Example #2
If, in the above example, the number of units produced during the year increased to 25,000, then determine the average cost calculation of production for the increased production.
Given,
- Variable cost per unit = $20
- Number of units produced = 25,000
- Total fixed cost of production = $100,000
Solution:
The calculation of the total variable cost of production will be –
The total variable cost of production = Variable cost per unit * Number of units produced
The total variable cost of production = $20 * 25,000 = $500,000
Now, the calculation of the total cost of production is as follows:
Total cost of production = Total fixed cost + Total variable cost
Total cost of production = $100,000 + $500,000 = $600,000
Now, the calculation is as follows:
Average Cost Formula = Total cost of production / Number of units produced
= $600,000 / 25,000
= $24 per unit
Therefore, the new unit cost of production was reduced from $25 to $24 per unit, owing to the benefits of economies of scale.
Diagram
Typically, the average cost curve (blue line) results in a U-shape, as seen in the above diagram. It is primarily because the average variable cost of production (gray line) decreases with the increase in production initially and then starts increasing with the incremental production. On the other hand, the average fixed costs (orange line) continue to decrease significantly as the production volume increases.
After the initial decrease, the marginal cost (yellow line) starts to increase due to diminishing marginal productivity. It intersects the curve at its lowest point (minimum), after which the curve also slopes upward. From this point onwards, the marginal cost curve is above the average cost curve, and hence an increase in production volume increases cost.
This concept is critical as it helps determine the long-run price and supply of any commodity, and hence it influences profit significantly. For instance, if the selling price of a commodity is higher than its average cost (AC), then the company makes a profit. On the other hand, if the selling price is lower than the unit cost, it is a loss-making proposition.
Advantages
Just as every concept has its own advantage and disadvantage, so does this concept. Let us try to identify some advantages of the same.
- The average cost function considerably simplifies the process of cost calculation and record keeping. It is easy to determine it and interpret it and use it for making informed decision.
- It automatically adjusts the impact of price volatility witnessed during the given period.
- It helps in taking price related decisions which involves fixing the prices for goods and services that will be profitable as well as cover the cost of production.
- The business can control cost and raise its profit figures if it is well informed about the average cost of production. Measures can be taken to bring down the cost.
- The average cost function guides the business regarding performance assessment. A low level of cost signifies a higher efficiency and less wastage.
- It leads to identification of areas where cost control in immediate requirement and the entity can take steps accordingly. This increases profitability.
- It makes manipulation of accounting figures difficult and provides an accurate picture of the business.
Disadvantages
Some disadvantages are as mentioned below:
- Different products have different types and levels of cost. The concept of averaging all the cost overlooks this differentiation, and this leads to inaccurate allocation of the cost.
- It ignores that fact of cost advantages that can be gained in production in bulk quantity, which is called economies of scale. This may affect the pricing strategy and the production level and give ambiguous results.
- Every time a new purchase happens at a rate different from the previous one, it changes, resulting in frequent changes in selling price.
- The average cost may not reflect the prevailing market rate as it averages out the price across the period.
- Since this method has made cost calculation very easy and simple to understand, this may impact the various cost drivers. The cost structure involves may factors that directly or indirectly influence the profitability. If they are overlooked, it hinders the understanding of cost behavior and cost management.
Average Cost Vs Marginal Cost
Both the above concepts are frequently used in the business sector. However, there are certain points of differences between them.
- The calculation of the former involves total cost divided by the total number of units whereas the calculation of the latter involves change in total cost divided by the change in quantity.
- The former represents the average amount spent on the production of one item whereas the latter represents that amount spent on production of one extra unit of a product.
- The former provides a measure of the efficiency of the cot control process in a business, whereas the latter provides a guidance regarding cost related decision in the short term and evaluates whether it is profitable to produce one extra unit of a commodity or not.
Thus, both the cost concepts contribute to the decision made in businesses related to production, cost analysis, pricing strategy, level of sales, expansion and growth.