Table Of Contents
What Are Appraisal Costs?
Appraisal Costs is the cost incurred by a business unit to ensure that the products and services they supply meet the customer's expectations, i.e., they are free from defects and fulfill all regulatory requirements. Examples of such costs include the cost incurred on inspection, field tests, internal audits, etc. In simple terms, it is a quality control measure for companies.
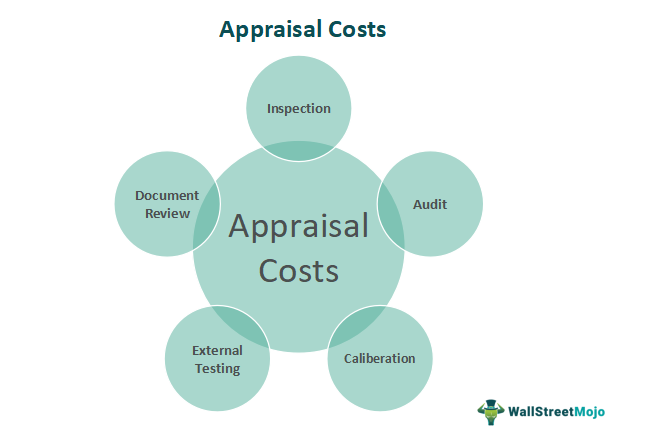
To tackle the losses due to selling faulty services or products, companies tend to incorporate the appraisal costs approach as it is a wiser way to save a larger chunk of money being lost. It helps the company raise its reputation in the market as an entity that does not compromise on quality for a few extra bucks.
Appraisal Costs Explained
The appraisal costs are the expenses incurred by the companies to ensure that the products they are selling in the market to their customers are free from material defects. These are the necessary expenses that the company incurs to ensure a higher level of customer and regulatory satisfaction, along with marinating the goodwill of the company in the market.
It is a smarter option to use an appraisal cost calculator to set aside an amount for an additional layer of quality control before the product is rolled out in the market. It not only dissatisfies the customer for the faulty product but also creates an aversion towards the brand and its other products as well, creating a block for the customer to come back and make a purchase.However, suppose the company finds the defect after the completion of the production by incurring the appraisal cost. In that case, there is no use for such extra cost, and the same will result in the complete production loss of the company. Therefore, costs must be incurred to find the defect before additional labor or material introduction. If the cost is incurred afterward, it does not solve any problem.
Appraisal costs are necessary because if there are any defects in the company's products, it can impact the goodwill of the company negatively, thereby reducing its sales in the market. The expenditure on appraisal shows that the organization is concerned about its reputation or goodwill in the market.
It is considered that the appraisal cost is much lesser than the cost of losing customers who are dissatisfied with receiving poor quality or defective products.
These are required to minimize the threat of bad reviews. In todayโs scenario, social media provides opportunities for customers to write their opinion on the products on various platforms. Customer review matters a lot in the growth of the business, and negative reviews can hinder the growth of the business.
The different areas where the appraisal cost is useful to include the cost incurred for incoming inspection and incoming tests, in-process inspection, the evaluation conducted to ensure that the requirements are met, and the final inspection.
Examples
Let us understand why businesses take the appraisal cost approach despite it adding to the costs of production with the help of a couple of examples. These examples shall give us a practical overview of the theoretical knowledge we have gained so far from this article.
Example #1
A retail shop named kitchen king, which was started by Mr. Eden in America and deals mainly with a wide variety of food processors. When Mr. Eden sold the first lot of food processors containing around 50 food processors, 45 of them were found to be defective and were returned by the customer. Due to this, the goodwill of Mr. Edenโs business was not developing.
So Mr. Eden decided to employ quality control staff who were required to check every food processor before selling it to the customer so that the returns could be minimized and a higher level of customer satisfaction. Suppose the salary of inspection staff is $500 per month and other costs related to testing and inspection of the product are $200 per month. Therefore, the total appraisal cost is $700 per month, i.e., sums of the salary of inspection staff and other costs related to testing and inspection of products.
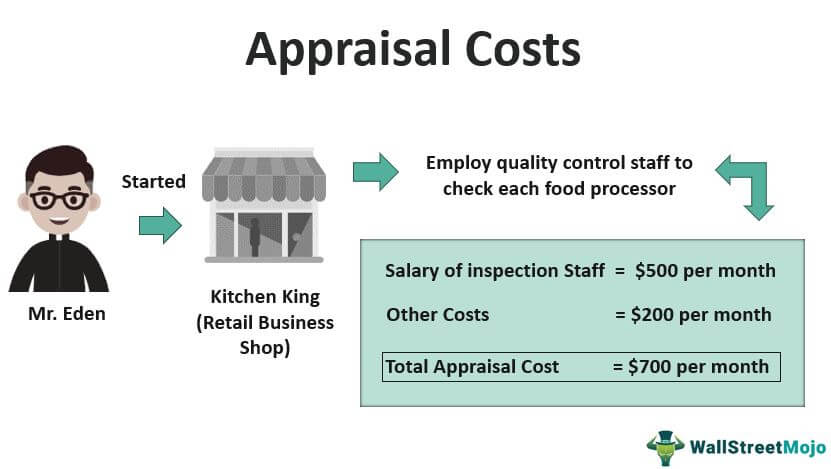
Example #2
In real estate, the appraisal of a property is one of the long list of costs homeowners incur before selling a property. It is to ensure that the price quoted by them is justified through the condition of the property.
As a result, owners spend significant amounts to get their appraisal scores better than the market average to fetch good deals. Moreover, banks also require an appraisal from an external party before sanctioning a mortgage.
In December 2022, an appraisal software company Reggora was able to cut the costs of a mortgage loan by $258 through their digital appraisal process.
Advantages of Appraisal Costs
Let us understand the advantages of using an appraisal cost calculator through the points below.
- It is the necessary expense that the company incurs to ensure a higher level of customer as well as regulatory satisfaction, i.e., it ensures that high-quality products are getting delivered to the customers of the company, thereby making them satisfied.
- Appraisal costs help organizations keep their products and services defect-free so that their goodwill can be maintained in the market. It is necessary because if there are any defects in the company's products, it can negatively impact the company's goodwill, thereby reducing its sales in the market.
- For the long-term survival and growth of the business, these costs are mandatory to maintain the quality of the products and services.
- It may help the business organization reduce the threat of bad customer reviews on social media platforms as the product quality is checked very well in advance.
Disadvantages
Despite the various advantages mentioned above, there are a few factors from the other end of the spectrum that affect the incorporators of the appraisal cost approach. Let us understand them through the discussion below.
- The company has to use the appraisal cost in the early manufacturing process. If the company finds the defect after the completion of the production by incurring the appraisal cost, then there is no use for such extra cost, and the same will result in the complete production loss of the company. So it is required that such costs to find the defect should be incurred before introducing the additional labor or material, and if the same is incurred afterward, then it will not solve any problem.
- Expenditure incurred on the appraisal cost can be very high as it requires the supervisor's salary and the purchase of expensive testing and equipment machines. So sometimes, the small industries that are working on a low budget cannot employ the personnel for the inspection and testing and are also unable to buy such testing and equipment machines. Therefore, they must sell their products without proper quality and control checks.
- If not done in the right manner, the appraisal cost can create a negative impact on the entire production facility of the company.
- Appraisal costs are incurred to determine if any material defect exists in the company's products. Still, this process is time-consuming and requires the efforts of different people.
Appraisal Costs Vs Prevention Costs
Both these costs are incurred with the aim to reduce quality-related issues leading to the dissatisfaction of customers and the disrepute of the company. However, there are differences in the fundamentals and implication of these costs which can be understood through the comparison below.
Appraisal Costs
- It refers to the costs incurred by a company to ensure the quality of the products is in line with the market standards and does not cause disrepute to the company.
- These can be in the form of external audits, document reviews, inspections, etc.
- Measurement equipment such as the weighing machines are also calibrated from time to time as a means to reduce the errors or packing materials under or above the fore-mentioned weight.
- These measures must be taken before the production as the cost would not make sense if its issues come to knowledge after the production process is completed.
- External certifications from regulatory authorities after inspecting the production unit can provide the company with an assurance of their process is good enough to meet the quality standards.
Prevention Costs
- Prevention costs refer to the expenditure incurred by a company to ensure the process set by the company has measures to reduce or ideally negate defaults.
- This can be in the form of training, designing, planning, and implementing measures to ensure the laborers and employees follow a checklist to avoid defects.
- Companies can also set checkpoints at different levels of production to eliminate errors stage-wise to avoid additional costs of rejected pieces after the production is completed.
- Educating laborers and staff of the latest technological advancement and equipment empowers them to use the equipment to its efficient best.
Recommended Articles
This article has been a guide to what are Appraisal Costs. Here we explain its examples, advantages, and disadvantages, and compared it with prevention costs. You can learn more from the following articles โ