Table Of Contents
Acceptable Quality Level (AQL) Definition
The acceptable quality level, as defined by ISO 2859, is the quality level that aims to maintain an average process of the specified acceptance quality. It also provides an upper limit for the consumer in accepting any subpar quality of lots.
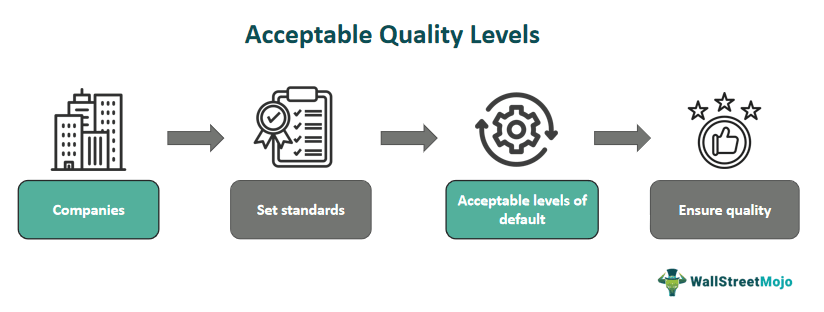
AQL is a commonly used technique for random sampling during product inspection that considers suppliers' and customers' calculated risks. It gives suppliers and customers a numerical reference point regarding accepting damaged goods. It offers a benchmark to measure a batch's or lot's quality, assisting in the decision to accept or reject.
Key Takeaways
- Acceptable quality level aims to assess quality at an average level, providing customers with an indication of the acceptable risk in accepting a subpar lot.
- Determining AQL involves considering factors such as the product's intended use, consumer expectations, industry standards, and the impact of flaws on functionality and safety.
- Determining AQL involves considering factors such as the product's intended use, consumer expectations, industry standards, and the impact of flaws on functionality and safety.
- AQL is advantageous for its economic efficiency, contribution to quality assurance, and its role in maintaining brand reputation.
Acceptable Quality Level Explained
Acceptable quality level maintains an average level of quality and provides a tolerable level of how much risk a consumer can accept in accepting a poor lot, if at all. It is designed to establish an economic and psychological effect of non-acceptance of lots. The concerned standard is ISO 2859. The sampling schemes for AQL under it are applicable to various inspections, including end items, storage supplies, components, operations, raw materials, materials in process, data or records, maintenance operations, and administrative procedures.
It is a statistical sampling method that determines the maximum acceptable number of defective products that can be found in a batch of goods. Companies can create an acceptable quality level sampling plan to conduct a normal inspection. The AQL system is popular due to its simplicity, cost-effectiveness, and reliability. The agreed-upon AQL level between the manufacturer and the customer determines the quantity of products inspected and the permissible amount of defects. Using this technique, items are guaranteed to be flawless and fulfill the necessary quality standards.
AQL-based inspections involve two types of risks: producer's risk, which involves rejecting a good lot with less or equal percentage of AQL defects. The second is the customer's risk, which involves accepting a bad lot with more defects than the consumer is willing to accept, also known as Lot Tolerance Perfective (LTPD) or Rejecting Quality Level (RQL).
Factors
Some of the factors that are important while deciding AQL are:
- Market: Selecting the proper AQL for a product is essential, particularly if it will be used and marketed internationally. Every product has acceptance quality levels that differ depending on the location and market. Understudying and knowing these requirements aids in determining the proper AQLs for the goods. Subsequently enabling producers to modify them to be more or less harsh.
- Type of products: Airplanes, drugs, and other consumables require a high defect rate due to their sensitivity to quality standards. Delays could lead to negative consequences, such as loss of life. Manufacturers must be less tolerant of defects and use tools to reduce manufacturing processes. It is common for these products to have a 1% or less defect rate, demonstrating the importance of quality control in manufacturing industries.
- Consumer preferences: Manufacturers must understand their end consumers' preferences to choose acceptable quality levels (AQLs) that align with their expectations. There is no rigid rule for choosing AQLs; manufacturers shall understand their products, target market, and end consumer to decide upon it. In a competitive market, it is crucial to choose the right AQL.
Companies can create an acceptable quality level chart or simply use an available acceptable quality level calculator online to come to a desired AQL. They could alternatively use an acceptable quality level table to understand it better.
AQL Defect Categories
They can be divided into three categories, which are given as follows:
- Critical defects: Critical defects are those that could harm customers or users and are unacceptable. They are defined as 0% AQL.
- Major defects: Major defects are likely to fail and are not acceptable by end users due to their potential failure. The AQL for major defects is usually 2.5%. They can be easily segregated with the help of an acceptable quality level table.
- Minor defects: Minor defects do not significantly reduce the product's functionality or purpose but differ from specified standards. Some end users may still buy these products, as they do not significantly reduce their usability.
How To Choose?
A product's acceptable quality level (AQL) is based on several criteria, including the product's intended use, consumer expectations, industry standards, and the effect defects may have on operation, safety, or aesthetics. The percentage or quantity of flaws acceptable per sample size is important to express it. Companies can draft an acceptable quality level sampling plan to accommodate it.
Several considerations, including product criticality, inspection effort and cost, potential customer impact, legal requirements, and product quality confidence, must be taken into account when choosing a suitable AQL. Organizations must balance quality assurance and inspection expenditures. More flaws are acceptable with a higher AQL, which lowers costs but raises the possibility of lower-quality products.
Examples
Let us look into a few examples to understand the concept better.
Example #1
Suppose Daisy, a toy manufacturing company owner, uses an acceptable quality level (AQL) as a quality control tool. AQL provides a standardized approach to evaluating product quality, ensuring consistency and meeting client expectations. It lets Daisy make informed decisions regarding toy batch acceptance or rejection, specifying the maximum allowable defect rate.
If the defect rate exceeds the AQL, she can negotiate with suppliers for rework, replacement, or corrective actions. AQL also helps Daisy manage quality-related costs by allocating inspection resources efficiently and focusing on critical areas. It also allows Daisy to evaluate the performance of her suppliers by monitoring defect rates and comparing them against the agreed-upon AQL. Overall, Daisy prefers AQL for its systematic and objective approach to quality control, decision-making, cost management, and consistency in her clothing manufacturing business.
Let's say she sets her AQl as 2.5%; after understanding the industry, consumer preferences etc., she created an acceptable quality level chart and also, to be additionally sure, used an acceptable quality level calculator online to come to a desired AQL. This means that her one batch of randomly selected goods should contain only a maximum of 2.5% of defects.
Example #2
The clothing industry is a prime example of implementing AQL as a quality control tool due to its high production volume, complex supply chains, varied product specifications, high customer expectations, regulatory compliance, brand reputation, and cost efficiency. AQL helps manage the quality control process efficiently, aligning expectations throughout the supply chain and ensuring consistent quality across various stages of production.
It also helps manufacturers balance quality assurance and cost-effectiveness, optimizing inspection resources based on acceptable defect levels. Overall, AQL is a valuable tool for the clothing industry to ensure quality, mitigate risks, and meet market demands.
Advantages
Some of the advantages of AQL are the following:
- Consistency: The AQL systems guarantee quality adherence and meeting of specified requirements. Customer satisfaction and loyalty towards the brand through a positive brand reputation can be maintained.
- Brand reputation: The AQL system reduces the possibility of lawsuits about quality, harm to one's reputation, and monetary losses due to subpar goods.
- Economical: The AQL system lowers the expense of rework, returns, and possible liability of dealing with damages' impacts. This is done by assisting in the early detection and rejection of faulty items.
- Standard measurement: The AQL system provides a universal or non-biased evaluation of quality by objectively assessing the product's quality.
- Early detection: The AQL system lowers the possibility of expensive recalls or production delays. This is because the process assists in the early identification and correction of quality concerns during production.
- Quality improvement: The company can pinpoint the underlying causes of quality problems and implement remedial measures to raise the general caliber of its output by tracking and evaluating the AQL data.